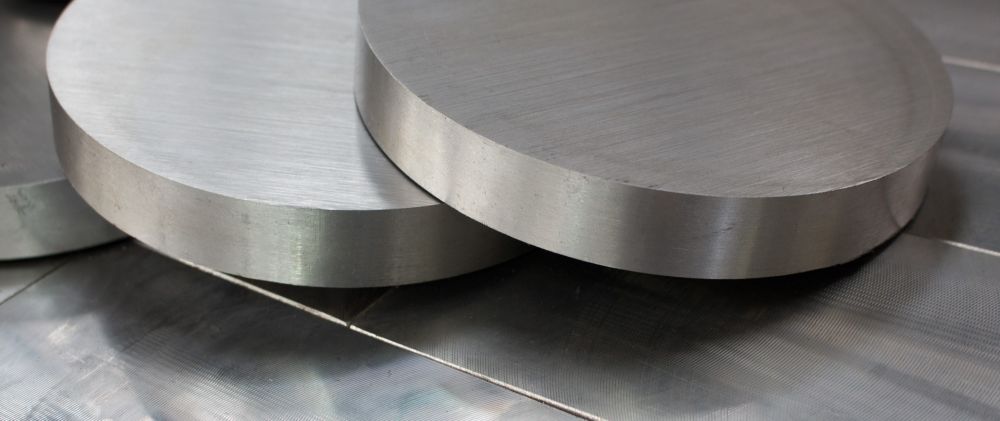
Yer kabuğunda yaklaşık %8 oranında bulunan alüminyum, oksijen ve silisyumdan sonra en çok rastlanan üçüncü element olmasına karşılık, ancak 19.yüzyılın ilk yarısında metal olarak elde edilmiş, ikinci yarısında da teknikte kullanılmaya başlanmıştır.
Bu gecikmenin birinci nedeni, alüminyumun doğada sadece oksit veya oksit karışımları biçiminde bulunmasıdır. En kararlı kimyasal bileşiklerden biri olan Al2O3'in indirgenmesi çok fazla enerji gerektirir. Bunu sağlayabilecek teknolojik yöntemler ilk kez 19.yüzyılda geliştirilmiştir. Birinci ile bağlantılı olan ikinci neden ise, yararlanılan cevherlerin Al2O3'ten daha kolay indirgenen diğer bir takım oksitleri de içermesi, dolayısıyla doğrudan cevherin indirgenmesiyle kazanılacak alüminyumun teknik açıdan kullanılamayacak kadar katışkılı olmasıdır.
Sonuçta, özellikle "bauxit" adlı cevherden kimyasal ön arıtma ile elde edilen saf alüminanın, 980°C'ta eriyen kriolit içinde çözündürülüp, elektrolitik indirgenmesiyle saf alüminyum üretimi gerçekleştirilebilmiştir. Bu gelişmelere bazı alüminyum alaşımlarının dayanımının çökelme sertleşmesiyle artırılması da eklenince, alüminyum esaslı malzemelerden yaygın şekilde yararlanma döneminin başladığı görülmektedir.
Saf Alüminyum Nedir
İlk sırada düşük yoğunluğu olmak üzere bazı temel özelliklere sahip olan alüminyum, diğer metallere göre başlıca üç noktada seçkinleşir; Alaşımlarında daha da belirgin olan dayanım/yoğunluk oranının yüksekliği, hafifleştirilmelerine öncelik verilen konstrüksiyonların çoğu için alüminyumun uygun bir malzeme olmasını sağlar. Örneğin uçak, taşıt, piyade silahı, taşınabilir kamp donatımı vb.
Elektrik iletkenliğinin yoğunluğa oranı bakımından tüm metal malzemelerin önünde gelen alüminyum, yüksek gerilim hatlarında bakırın yerini almaktadır.
Havada ve diğer birçok ortamda korozyona dayanıklı oluşu, alüminyuma dekoratif görünüm kazandırarak mimari uygulamalarda ve ev araçlarının üretiminde de geniş bir alan açmıştır.
Elektrokimyasal gerilim serisindeki konumu nedeniyle asal bir metal olmayan alüminyumun korozyona dayanıklılığı, hava da veya sulu çözeltilerde yüzeyi kaplayan oksit tabakasından ileri gelir. Bu koruyucu tabaka, bozulduğunda doğal oksitlenmeyle bile hemen yeniden oluşur; ayrıca ortamda bulunabilecek asitler ne kadar oksitleyici ise o kadar kararlı davranır. Örneğin derişik nitrik asit alüminyum kaplarda nakledilebilmektedir.
Öte yandan anılan oksit tabakasını çözebilen derişik alkaliler alüminyumu korozyona uğratır. Benzer etki yapan maddeler arasında taze harç ve yapı kireci de sayılabilir. İnşaatlarda kullanılan alüminyum profil ve kaplamalar, bu bakımdan sıva işi bitinceye kadar bantlanarak korunmalıdır.
Yüzeydeki doğal oksit tabakası sadece 0,01 pm kalınlığında olup çok sayıda gözenek içerdiğinden, alüminyumda öncelikle bakır, demir gibi katışkılar yerel bileşim farklılıkları ve dolayısıyla korozyon pilleri yaratabilir.
Buna karşı başlıca iki önlem söz konusudur:
Katışkıların miktarları sınırlanır.
Yapay yolla gözeneksiz koruyucu tabaka oluşturulur.
Ürünlerin korozyona dayanıklılığını güvence altına alabilmek için, ingot aşamasında saflığı en az %99 ve katışkıları kontrol edilmiş olan izabe alüminyumu (H) seçilmeli, hurda kullanılmamalıdır. Uç tabakalı elektroliz ile elde edilen çok saf alüminyum (R) ise kimyasal kararlılık bakımından en üstün özelliklere sahiptir.
Alüminyumun doğal koruyucu tabakasını kuvvetlendirmek üzere kimyasal fosfatlama ve kromatlama yapılabilir. Ancak bu amaçla daha yaygın olarak uygulanan alüminyumun elektrolitik oksitlenmesidir. Sülfirik veya kronik asitli banyolarda gerçekleştirilen bu işlem sonucu, homojen şekilde kalınlaştırılmış ve yoğunluğu artırılmış saydam yüzey tabakasının değişik elektrolit katkılarıyla ayrıca renkli olması da sağlanabilir. Anılan yöntem alüminyum veya alaşımlarından üretilmiş parçaların kimyasal etkilere karşı daha iyi korunmasında büyük ağırlık taşır.
DIN 1712'de E-AlH olarak belirtilen en az %99,5 saflıktaki alüminyumun elektrik iletkenliği bakırınkinin sadece %62'sine, yoğunluğa oranlandığında ise 2,1 katına ulaşır. Bu teknik üstünlüğünün yanında fiyatının da uygunluğu nedeniyle, iletken hacminin ve lehimlenebilirliğin önemli olmadığı uygulamalarda alüminyum bakırın yerini almıştır.
Alüminyumun düşük elastik modülü, herhangi bir konstrüksiyonun çelikten yapılma durumuyla karşılaştırıldığında, rijitliğin azalmasına yol açar. Isıl genleşme katsayısının ise çeliğinkinin yaklaşık iki katı oluşu alçak sıcaklık için tank ve boru hatlarının yapımında göz önünde tutulmalıdır.
Yüzey merkezli kübik kafese sahip olan alüminyumun sıcak ve soğuk şekil değiştirme kabiliyeti çok iyidir. Ekstrüzyon yöntemiyle her türlü profil üretilebildiğinden, pencere, kapı ve otomobil gövdeleri için değişik profil serileri geliştirilmiştir. Böylece tasarımcının öngördüğü biçimler basit montajlarla gerçekleştirilebilir.
Paketlemede yararlanılan folyolar, şekil değiştirme oranı %99'a varabilecek haddeleme sonucu, birkaç mikrona kadar inen çeşitli kalınlıklarda elde edilmektedir. Bu amaçla kullanılan malzeme, üretilen folyoda küçük deliklerin meydana gelmemesi için, metal dışı kalıntılar ile demir ve silisyum gibi katışkılardan büyük ölçüde arıtılmış R kalite alüminyum olmalıdır.
Alüminyumdaki kalıntılar parlatma işlemini de güçleştirirler. Dolayısıyla far reflektörleri gibi yüzeylerde ve bitmiş parçanın parlaklığının dekoratif görünüm bakımından önemli olduğu durumlarda gene çok saf (R) alüminyum tercih edilir. Sözü edilen malzeme, bütün alüminyum türleri arasında en yüksek kimyasal kararlılığa sahip olduğundan, özellikle çökelme sertleşmesi uygulanabilen korozyona daha az dayanıklı magnezyum, silisyum veya bakırlı alaşımların giydirilmesinde de kullanılır.
Yüksek saflıktaki erimiş alüminyum, katılaşmada çubuksu ve iri taneli bir içyapı oluşturma eğilimindedir. Böylece çoğunlukla sürekli döküm yoluyla üretilen kütüklerde belirgin bir döküm dokusu (tekstür) ile karşılaşılır. Söz konusu oluşum haddelemenin ilk pasolarında giderilirse de, şekillendirme sürdürüldükçe bu kez haddeleme dokusu ortaya çıkar. Ancak uygun bir paso programı ve ara tav uygulanarak buna engel olunabilir. İstenmeyen bir diğer olay ise, sıvı alüminyumda hidrojen çözünürlüğünün yüksek olması, bu nedenle katılaşma sonrasında elde edilen yarı mamulde veya bitmiş parçada gözeneklerin bulunabilmesidir.
Önerilen Makale: Çelik profil malzemeler ve uygulamaları hakkında detaylı bilgi almak için
çelik profil fiyatları sayfamızı ziyaret etmenizi tavsiye ederiz.
Alüminyum Alaşım Sistemleri
Alüminyumun düşük yoğunluk, yüksek korozyon direnci gibi üstünlüklerinden makina, taşıt ve yapı endüstrisinde geniş oranda yararlanılması, ancak dayanım özelliklerinin alaşımlama yoluyla iyileştirilmesinden sonra gerçekleşebilmiştir. Dayanımın çökelme sertleşmesiyle artırılabileceğinin bulunması da alüminyum alaşımlarının geliştirilmesinde çok büyük rol oynamıştır.
Alüminyumun en önemli alaşım elementleri bakır, magnezyum ve silisyum olduğundan, alaşımların özelliklerini açıklayabilmek için önce Al-Cu, Al-Mg ve Al-Si ikili sistemleri ayrıntılı olarak incelenecektir;
Eriyikten ayrışan ve en azından ötektik yapı bileşeni niteliğinde olan Al2Cu ara fazı, malzemenin gevrekleşmesine yol açtığı için, döküm tekniği bakımından ötektik bileşime yakın olması gereken Al-Cu alaşımlarının pratikte kullanılmasını engeller. Öte yandan katılaşma aralığının genişliği nedeniyle yapısal aşırı soğuma dikkate alınarak, teknik Al-Cu alaşımlarının bileşimindeki bakır miktarı, ötektik yatayının başladığı %5,7 değerinin daha da gerisinde kalmak üzere yaklaşık %4,5 ile sınırlandırılmıştır.
Ötektik sıcaklığın altında bakırın alüminyum kafesindeki çözünürlüğü azaldığından, çökelme sertleşmesi için gerekli ön koşullardan biri yerine gelmiş olur. Malzemeyi gevrekleştirmeden dayanım artışı sağlayan çökelme sertleşmesi ilk kez bu tür alaşımlarda bulunmuştur.
Alüminyum-Magnezyum sisteminin çok sert ve gevrek olan, ayrıca korozyona dayanıklılığı da azaltan Al3Mg2 ara fazından ötürü, söz konusu alaşımların kuIlanılabilirliği Mg oranının teorik %15 sınırından bile oldukça düşük tutulmasına bağlıdır.
İkili Al-Mg alaşımlarında dayanım artışı yalnız katı çözelti oluşumuyla ilgilidir. Solvüs eğrisinin elverişliliğine karşın önemli bir çökelme sertleşmesi görülmez. 8 fazı öncelikle tane sınırları boyunca iri parçacıklar halinde çökeldiğinden, %7 den fazla magnezyumlu alaşımlar taneler arası korozyona uğrayabilir. Tane sınırlarındaki bu Al3Mg2 ağı çökelme sertleştirmesine benzeyen homojenleştirme işlemiyle dağıtılarak, malzemenin anılan korozyon türüne eğilimi ortadan kaldırılır.
Ötektik alaşım yaklaşık %80 oranından gevrek Al3Mg2 azı içerdiği için, her ne kadar 451°C gibi düşük sıcaklıkta erime avantajına sahip olsa da, teknik açıdan yararlanılamaz durumdadır. Ötektik bileşimden sola doğru uzaklaşılırsa, Al3Mg2 iktarı azalmakla birlikte bu kez katılaşma aralığı genişler. Dolayısıyla Al-Mg döküm alaşımlarında da magnezyum derişikliği, dar aralıklı ve α-alanında sonuçlanan bir katılaşmayı gerçekleştirmek amacıyla, %2 ila 11 arasında seçilir.
Alüminyum-Magnezyum-Silisyum üçlü sisteminin magnezyum-silisyum kenarında Mg2Si ara fazı ortaya çıkar. Mg2Si ayrı bir alaşım bileşeni gibi düşünülerek, bu bileşikle alüminyum elementi arasında ikili faz diyagramı görünümünde bir kesit elde edilebilir. Bu bölgedeki uygun bileşimli alaşımlar, Al-Mg veya Al-Si sistemlerinden farklı olarak çökelme sertleşmesi gösterirler. Benzer davranışa MgZn2 ara bileşiğinin bulunduğu Al-Mg-Zn üçlü sisteminde de rastlanır. Her iki sistem esas alınarak çökelme sertleştirmesinin uygulanabildiği birçok önemli alüminyum alaşımı geliştirilmiştir.
Çökelme Sertleşmesi
Teorik esasları bu işlem yardımıyla belirli büyüklük ve dağılımda çökeltilen fazlar, dislokasyon hareketlerini engelleyerek dayanım artışı sağlar. Alüminyum alaşımlarında söz konusu çökeltilerin çapı yaklaşık 1 nm aralarındaki uzaklık ise 10..20 nm dolayındadır. Böylece 1 mm3 hacmindeki alaşımda çökelmiş parçacık sayısı 1010 1020 değerine ulaşır.
Burada örnek olarak alüminyum-magnezyum-silisyum sistemi için ele alınan ısıl işlemin ilk adımı, 520°C 'da yapılan çözme tavıdır. Çözme tavının süresi, döküm içyapısından veya daha önceki ısıl işlemlerden gelebilecek iri Mg2Si çökeltilerinin α-KÇ içinde tümüyle çözünmesine yeterli olmalıdır. Bu olay genellikle 1/2 ilâ 2 saat arasında gerçekleşir.
İkinci adım malzemeye su verilerek oda sıcaklığında aşırı doymuş α-katı çözeltisinin elde edilmesidir. Aşırı doymadan ileri gelen sertlik artışı önemsiz olduğundan, parçaya gerekiyorsa bu durumda soğuk şekil verilebilir. Son adım olan yaşlandırma, 125°C ila 175°C arasında seçilecek sıcaklığa göre, 4 saatten 3 güne kadar değişen sürelerde uygulanır.
Dövme Alüminyum Alaşımları
Bu malzemelerden, çökelme yoluyla sertleştirilemeyen Alüminyum-magnezyuma alaşımları soğuk şekillendirilme, mekanik parlatılma ve kaynak edilmeye elverişlidirler. Çekme dayanımları Pekleşmeyle 300 N/mm2'ye kadar artabilir. Yüksek saflıkta alüminyumdan üretilen örneğin AlRMgl özellikle kimyasal parlatma ve anodizasyon için uygundur.
Deniz suyuna da dirençli olan Al-Mg alaşımları, yüksek korozyon dayanıklılığı ve kolay şekillendirilebilme istenen, dayanımın ise fazla önemli olmadığı, atmosfer etkisine açık yapı elemanları gibi yerlerde kullanılırlar. Çökelme sertleşmesi gösteren alaşımlar başlıca dört grupta toplanabilir:
- AlCuMg-alaşımlarında çekme dayanımını 440 N/mm2 ve 0,2 sınırını da 290 N/mm2 dolayına yükseltmek mümkündür. Magnezyumun etkisiyle hızlanan yaşlanma oda sıcaklığında gerçekleşir. Bakır miktarının fazla olması korozyona dayanıklılığı azaltır. Bu sakınca malzeme yüzeyine saf alüminyumdan ince bir tabaka giydirilerek giderilebilir.
- AlMgSi-alaşımları en çok 320 N/mm2 düzeyinde orta dayanımlı malzemelerdir. 0,2 sınırı sıcak yaşlandırmada 260 N/mm2, soğuk yaşlandırmada ise 110 N/mm2'ye ulaşabilir. Korozyona dayanıklılıkları iyi olup, parlatma ve anodizasyona elverişlidirler.
- AlZnMg-alaşımları, yaklaşık 350 N/mm2 lik çekme dayanımlarıyla AlCuMg alaşımlarının altında kalmakla birlikte, kimyasal etkilere karşı daha dirençlidirler. Bu grup mekanik özellikler ve korozyon davranışı bakımından optimum çözümü yansıtır.
- AlZnMgCu-alaşımları sadece çökelme sertleştirmesi uygulanmış durumda, 530 N/mm2 ile en yüksek dayanımlı grubu oluştururlar. Ancak korozyona dayanıklılıkları bakırdan ötürü pekiyi değildir. Soğuk pekleştirmeden sonra sıcak yaşlandırma yapılırsa malzemenin kendi ağırlığıyla kopma uzunluğu 25 km'yi bulur. Aynı sonucun çelikte elde edilebilmesi ise çeliğin çekme dayanımının 1900 N/mm2 olmasını gerektirir.
Dökme Alüminyum Alaşımları
Bu alaşımların en önemlilerinde, Al-Si faz diyagramındaki ötektik noktanın bileşimi esas alınmıştır. Ötektik Alüminyum-Silisyum alaşımları dayanım özelliklerinin iyi olması yanında, üstün döküm özelliklerine de sahiptirler. Basınçlı döküm, kokil döküm ve kum döküm için uygun malzemelerdir.
Kum kalıptaki yavaş soğuma nedeniyle silisyumun iri taneli olarak ayrışmasını önlemek üzere, döküm öncesinde eriyik yaklaşık % 0,1 Na ile aşılanır. Söz konusu katkı, aşırı soğumayı artırıp çok sayıda çekirdek oluşturarak, ince taneli bir iç-yapı elde edilmesini sağlar. Aşılama işleminin bir diğer sonucu da ötektik noktanın daha yüksek silisyum miktarlarına kaymasıdır. Dolayısıyla içyapının tümüyle ötektik olması istendiğinde, kum döküm alaşımlarının aynı türden kokil döküm alaşımlarına göre yaklaşık %1 daha fazla silisyum içermeleri gerekir.
Al-Si alaşımları, öncelikle eriyiğin akıcılığının önemli olduğu ince etli, basınç altında sızdırmaz elemanların dökümünde tercih edilirler.
Ötektik Alüminyum-Silisyum-Magnezyuma/ alaşımlarına çökelme sertleşmesi uygulanabilir. Silisyum miktarının azalması döküm özelliklerini olumsuz yönde etkiler. Kum kalıba dökülen parçalar kokil döküme göre kaynağa daha elverişlidir.
Alüminyum-Silisyum-Bakır alaşımları da çökelme sertleşmesi gösterirler. Böylece 0,2 sınırı 200 N/mm2'ye ulaşabilir. Silisyum miktarı yüksek, bakırı düşük alaşımların döküm özellikleri daha iyidir. Ayrıca titan katılarak ince taneli içyapı oluşturulması süneklik, vurma dayanımı ve işlenebilme bakımından yarar sağlar.
İçten yanmalı kuvvet makinaları için geliştirilen alüminyum piston alaşımlarından bazıları ötektik üstü bileşimdedir. Al-Si ötektiğinin 20°C ile 200°C arasında ortalama 20.10-6K-1 olan ısıl genleşme katsayısı, silindirlerde kullanılan dökme demirinkinin yaklaşık iki katını bulur. Ancak artan silisyum miktarıyla, örneğin %25 Si için (16..17). 10-6K-1 dolayına düşer. Bu alaşımlara yüksek sıcaklık dayanımını iyileştirmek amacıyla bakır ve nikel de katılır. Pistonlar kokile dökülürler. Metal kalıpta soğuma hızlı olduğundan parçada iç gerilmelerin ve aşırı doymuş katı çözeltinin oluşması beklenmelidir. Her iki olgu işletmede zamanla hacim değişikliğine yol açabilir. Bu nedenle döküm parçalara ısıl işlem uygulanarak iç gerilmeler giderilir ve içyapı mümkün olduğu kadar termodinamik denge durumuna yaklaştırılır.
Alüminyum alaşımlarının erime sırasında hidrojen alma eğilimleri çok kuvvetlidir. Hidrojen, havadaki nemin alüminyumun yüzeyinde aşağıdaki reaksiyonla indirgenmesi sonucu ortaya çıkar:
3H2O + 2Al → Al2O3+ 6H
Dolayısıyla döküm parçalarda gözenekliliği önlemek üzere, yarma gazlarında nem bulunan gaz veya sıvı yakıtlı pota ocaklarında eritmeden kaçınılmalı; elektrikli ocakların kullanılması halinde de, dökümden önce gaz giderme işlemi gerçekleştirilmelidir. Bunun için eriyiğe daldırıldığında nötr süpürme gazı veren maddelerden yararlanılır. Al2O3 ise erimiş metalin yüzeyinden tuz türü cüruf yapıcılar yardımıyla uzaklaştırılabilir. Soğumanın çok hızlı olduğu basınçlı dökümde, atomsal hidrojen fazla olsa bile ayrışmaya zaman bulamayarak katı çözeltide kalacağından, gözenek oluşumu kum ve hatta kokil döküme göre büyük ölçüde azalır. Ancak bu davranışın bir sonucu olarak, basınçlı döküm parçalar kaynağa elverişli değildir. Malzemenin erime sıcaklığına yeniden ısıtılmasıyla, daha önce aşırı çözünmüş olan hidrojen birden serbest hale geçerek kaynak dikişinde gözenek meydana getirir.