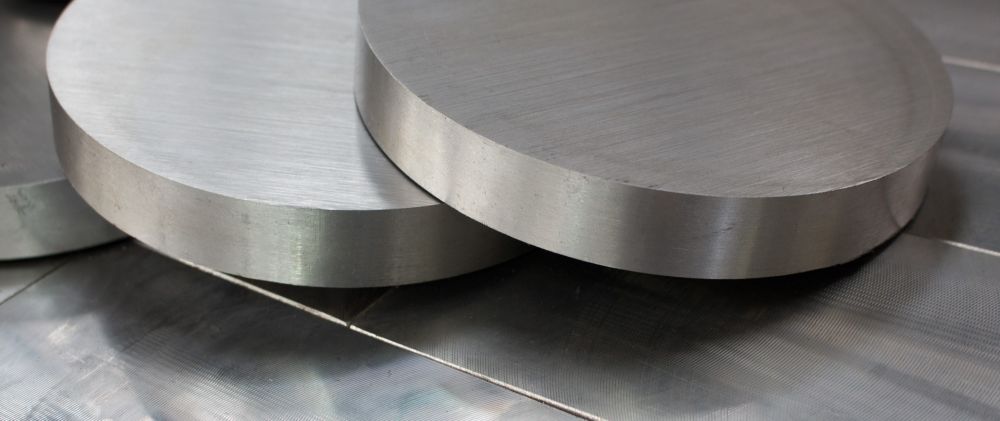
İyon nitrürasyon, metallerin kullanım alanlarında geniş bir çeşitliliğe sahip olabilmeleri için yüzeylerinin sertleştirildiği prosestir.
Proses iyonize hale gelmiş azotun yalnız veya diğer gazlarla birleşerek yüzeye nüfuz edip yayılmasıdır. İyonize olan azot kendisine has karakteristik bir renk olan erguvani akkor halinde parça üzerinde yerleşerek gözlenir.
Plazma, maddenin katı, sıvı, gaz halleri yanında maddenin dördüncü halidir. Plazmanın da maddenin diğer hallerinde olduğu gibi kendine has özellikleri vardır. Plazma, yüksek sıcaklık ve enerji yoğunluğuna, iyi elektrik ve ısı iletkenliğine sahiptir. Plazmaya elektrik ve manyetik alanla etki edilebilir. Plazma dış ortama karşı elektriksel açıdan nötrdür. Plazmayı dışarıdan termik ve manyetik olarak sıkıştırarak enerji yoğunluğunu ve sıcaklığını sınırsız bir şekilde yükseltmek mümkündür.
Bir gaz atomuna o gazın iyonizasyon enerjisinden daha büyük bir enerji verildiği zaman, o atomdan bir elektron ayrılır ve o atom iyonize olur. Bu olay bir gaz kütlesi için gerçekleştirilirse plazma elde edilmiş olur.
İyon Nitrürasyon işlemi
İyon nitrürasyon işlemindeki temel elemanlar vakum pompası, vakum kabı (fırını), gaz vericileri, güç kaynağı ve ayar ünitesidir.
0,1 - 10 torr'luk basınç verebilen vakum, 1000-1500 V'luk DC güç ünitesi; ve vakum kabı ortamın kirletici ve reaksiyona engel teşkil eden gazların ortadan kaldırılmasından oluşur.
İyon nitrürasyonunda saf azot veya azot - hidrojen karşımı içeren gazlar kullanılır. İyon nitrürasyon işlem sıcaklığı 400-600 °C dir. 350-450 °C arasında azot doymuşluğu ile iyon nitrasyon işlemi gerçekleştirilir.
Çeliğin kalitesine ve istenen sıcaklığı bağlı olarak işlem süresi 10 dakika ile 20 saat arasında değişir.
İş parçası, güç kaynağının negatif (-) kutbuna, vakum kabı da pozitif (+) kutbuna bağlanmıştır. Yüksek voltajlı elektrik enerjisi azot gazından azot iyonları elde etmek için kullanılır. Pozitif yüklü iyonlar, elektrik alan ile hızlandırılırlar ve katod olan iş parçası üzerine çarptırılırlar. İyon bombardımanı, iş parçası üzerinde "Saçınma" olarak bilinen, atomik seviyede bir temizleme yapar. Bu, iş parçasının yüzeyinin ısınmasına ve yüzeye azot yayınmasına neden olur. Bu işlem azot içeren bir atmosferde, çok düşük bir basınç altındaki vaktim kabı içerisinde yapılır. İşlem sırasındaki basınç 0.1-10 mbar arasında değişmektedir. Elektrik potansiyeli ise 500 Volt civarındadır. Sistemde doğru akım kullanılmaktadır. Bu işlem, florasanlarda ve neon lambalarda meydana gelen olaya benzemesine rağmen, özel elektronik devreler tarafından kontrol edilen yüksek akım yoğunluklarında işlem yapılır.
İyon nitrürasyon olayı şu şekilde açıklanabilir: Anot-Katot arasındaki yüksek gerilim düşümü nedeni ile hızlanan yüklü parçacıklar çarpışma ile katod önündeki gaz atomlarını iyonize ederler. Ortaya çıkan iyonlar pozitif yük taşıyıcı halinde metal yüzeyine çarparlar. Voltaj düşümü doğrusal olmayıp, düşümün hemen hemen tamamı katodun birkaç milimetre önünde gerçekleştiği için çarpışmanın tamamı ve iyonizasyonun tamamına yakını bu bölgede oluşur. Katot (iş parçası) üzerinde oluşan çizgi halindeki parlaklık iş parçasının kenarlarını takip ettiği için bütün yüzey (delikli, düz, karmaşık vs.) homojen iyon bombardımanına maruz kalır ve sonuçta homojen bir sertlik derinliği sağlanır.
Önerilen Makale: Paslanmaz çelik sac malzemeler ve uygulamaları hakkında detaylı bilgi almak için
çelik dar bant sayfamızı ziyaret etmenizi tavsiye ederiz.
Akkor Deşarjı
Yüzey mühendisliği uygulamalarında akkor deşarjı bir doğru akım kaynağından veya alternatif akım kaynağından oluşturulmaktadır. Her ne kadar iki tipte akkor deşarjı kullanılıyorsa da yüzey sertleştirme işlemlerinde yalnız doğru akım akkor deşarjı yaygın olarak kullanılmaktadır.
Bir akkor deşarjı plazmanın, iki elektrot arasına birkaç yüz voltluk potansiyel fark uygulanmasıyla 10 mbar kadar düşük bir basınçta oluşturulabilir. Eklenen gaz oluşan elektrik alanı içerisinde iyonlaşır ve akkor deşarjı ile beraber bir parlama olayı görülür.
Yüzey Sertleştirmede kullanılan akkor deşarjın kendi kendini devam ettirebilecek bir yapıda ve iş parçasını işlem sıcaklığına ısıtabilecek bir kapasitede olması gerekir. Anormal akkor deşarj bölgesi istenen bu özellikleri kapsar ve bu bölge (G - H) yüzey sertleştirme işlemlerinde kullanılır. Fakat bu bölge durağan değildir ve olay kesilip ark meydana gelebilir. Eğer ark sürerse iş parçası ve elemanlarda birçok zararlar meydana getirebilir. Sonuç olarak, birçok plazma ısıl işlem üniteleri çok ileri devre kontrolleri (Devre Kesici Sistemler), içerir. Bunlar oluşabilecek herhangi bir arkı söndürürler.
Akkor deşarj kendine has özelliği olan birçok bölgeden oluşur. Bunlardan en önemlisi katot düşümü veya katot karanlık bölgesi olarak bilinen bölgedir. İyonizasyonun tamamına yakını bu yüksek gerilim alanı bölgesindeki elektron/gaz etkileşimi neticesinde oluşur. Bu iyonların çoğu katota çarpıp nötralize olmaktadır. Partikül bombardımanı katodu ısıtır ve parça yüzeyinden elektron çıkarmayı (Sekonder Elektron Emisyonu) oluşturur ki bu olay neticesinde akkor deşarjın sönmesine engel olan yeterli elektron sağlanır. Daha küçük önemli bir etkide saçınma ile metal yüzeyinden kaldırılan malzemelerle ilgilidir. Bu olay, işlem sırasında devam eder ve katot yüzeyinin temiz ve aynı zamanda aktif olmasını sağlar.
İyon Nitrürasyonunda Plazma Oluşumu
Saf bir termal proseste, gazın yüzbinlerce derece sıcaklığa eriştirilerek plazma fazı oluşturulur. Gazın hareketi ile katot - anot arasında voltaj düşüşü ile şarj taşıyıcı elementler harekete geçer. Çarpışma prosesi ile gaz partiküllerinin atomları veya molekülleri iyonize olurlar. Elektronlar anodik olarak yerleşen fırın duvarına hareket ederken, pozitif iyonlar katodik olarak davranan iş parçasına hareket ederler.
Voltaj düşüşü fırın duvarı ile iş parçası arasında yüksek vakum etkisi lineer olarak düşmemektedir. Gözlenen voltaj katodun birkaç mm ötesinde oluşur. Bu yüzden voltaj düşüşü "katot - fall" olarak adlandırılır. Tüm çarpma ve iyonizasyon prosesleri yüzey üzerinde "katot - fall" alanında gerçekleşir. Bu yüzden uygun plazma fazı, iş parçasının yüzeyinin ön bölgesinde oluşturulması, vakum fırınının içinde şarj taşıyıcılar içeren işlem gazını içermesiyle sağlanır. Pozitif boş şarjlar anot olarak davranır ve böylece akkor deşarjının plazma bölgesinde iş parçası ve fırın duvarı arasındaki mesafeye bağlı olarak yüzey işlemi gerçekleştirilir.
Akkor demetinin malzemenin yüzeyini saracak şekilde gönderilmesi ile yapının yüzeyinde homojen reaksiyon sağlanır.
Katot düşüşünde, pozitif azot iyonları çarpışma prosesi ile hızlı bir şekilde iş parçasına doğru hareket ettirerek gözlenir. Uygulanan voltaj ve pozitif iyon sayısına bağlı olarak kinetik enerjilerinde değişim gözlenecek ve birkaç yüz elektron voltluk enerji proseste üretilecektir. Bu bağlı olarak otomatik plazma sıcaklıkları on bin dereceden birkaç yüz bin derece sıcaklığa kadar değişim gösterir.
Uygulanan voltaja bağlı olarak iş parçasının yüzeyine iyonların çarpmasıyla sabit bir kinetik enerji ortaya çıkar.
Katoda olan kütle transferi aşağıdaki mekanizmalardan birçoğunu içerir.
• Saçınma Reaksiyonu (Sputtering)
• Kimyasal Absorbsiyon (Chemical Absorbtion)
• Birikme (Condensation)
• İmplantasyon (Implantation)
Yüzeye çarpan iyonlar, yüzeyde yüksek sıcaklıklar oluşturarak buharlaşmaya yol açar. Bunun sonucunda iş parçası yüzeyindeki demir ve diğer alaşım elementlerin atomları, metalik olmayan element atomları (Karbon, Oksijen, Azot) ile yüzeyden uzaklaşır. (Saçınma Reaksiyonu)
Yüzeye çarpan iyonların ancak çok az bir kısmı iş parçasına yayına. Bu olay direkt implantasyon olarak adlandırılır. Bu olay sayesinde elektronların büyük bir kısmı ile saçılma gerçekleşir.
Saçılan demir atomlarıyla yüksek enerjili azot atomları yüzey civarında FeN şeklinde birleşip metal yüzeyinde birikirler. (Biriktirme)
FeN sıcak metal yüzeyinde kararsızdır ve diğer kararlı nitürlere (Fe2N, Fe3N ve Fe4N) dönüşür. Dönüşüm sırasında serbest kalan azot atomları ya metale yayınır ya da plazmaya döner. (Kimyasal Absorbsiyon)
İyon nitrürasyon işleminde gaz basıncının azaltılması (Partikül yoğunluğunun azalması) yüzeyden saçılan atomların serbest hareket mesafesini arttırmakta, demir ile azotun birleşme olasılığını azaltmaktadır. Dolayısıyla yüzeyde oluşan FeN tabakası incelmektedir. Eğer basınç artırılırsa FeN tabakası kalınlaşacaktır.
İyon iş parçası yüzeyine çarptıklarında çeşitli metal atomlarıyla (Cr, Mo, V, Al, W) karşılaşırlar.
Saçınma, iş parçasının yüzeyine yerleşen sıcak iyonların, yüzeye çarpmalarıyla buharlaşmaya neden olmalarından ötürü buharlaşma prosesi olarak adlandırılır. Bu sıcaklıklar, birkaç yüz derece sıcaklıklarda birçok küçük yüzey alanlarında oluşmasına rağmen iş parçasına zarar vermeyecektir.
İş parçasının yüzeyinin ortalama sıcaklığı, iş parçasının sıcaklığını gösterir. Bu sıcaklığın tespiti ise termokupllar veya radyasyon pirometreleri ile yapılır.
Saçınma prosesi esnasında, iyon enerjisinin hem iş parçasının yüzeyine doğru hareket eden atom ve elektronlarına hem de yapışan partiküllerin kinetik enerjisine dönüşür.
Metaller, metalik olmayan elementlerde iş parçasının yüzeyine yapışabilir. Böylece yüzey karbür ve oksitler açısından zengin hale gelecektir. Tane sınırları boyunca yüzeyde bu elementler ikincil difüzyona neden olur.
Kimyasal Absorpsiyon
Azot iyonları iş parçasının yüzeyine çarpıp, üstteki birkaç atom sertleştirilecek yüzey tabakası alanına nüfuz ederek, kalan iyon enerjisini ısıya dönüştürerek iş parçasını ısıtırlar. Bu iş parçasının dıştan ısıtıldığını gösterir.
Eğer gaz karışımları saf azot ve diğer elementlerin iyonlarının yerine kullanılırsa, nüfuziyet sağlanacak ve iş parçası ısınacaktır.
Kondensasyon (Yoğunlaşma)
Plazmayı oluşturan azotun iş parçasının yüzeyine gönderilmesiyle demirin kristal kafesinde değişiklik gözlenmeye başlar ve iyon bombardımanına tutulur. Azot absorbisyonu saçınım reaksiyonuna bağlı olarak gerçekleşir. Demir atomları yüksek reaktiflik özelliğine sahip azot atomları plazmada karşılaştıklarında iş parçası yüzeyinde absorbsiyon oluşmuş ve demir nitrür (FeN) halinde iş parçası yüzeyine yerleşir.
Plazmada oluşan demir nitrür (FeN) teorik olarak ağırlıkça % 20 - 25 Azot içerir. FeN iyon nitrürleme sırasında sürekli olarak ortaya çıkmaktadır.
FeN soğutulmamış katodik iş parçası yüzeyinde 400 - 600 °C arasında kondense olacak ve düzensiz düşük nitrür içeren Fe2N, Fe3N, Fe4N 'e ayrışacaktır. Azotun bu kısmı iş parçasına difüze olacak ve plazmayı oluşturacaktır.
Kondensasyon ve saçınma prosesleri kullanılan gazın cinsine göre değişir. Gaz olarak (amonyak, azot, hidrokarbon) kullanılır. Örneğin, eğer gaz basıncını düşük değerlerde tutarsak (partikül yoğunluğunu düşürerek) geniş hareket alanlarından ötürü düşük olasılıkta çarpışma gözlenir. Çünkü ayrılan atomlarla iş parçası arasındaki mesafe genişlemiştir. Eğer gaz basıncı fırın içinde yüksek ise, back - diffusion (yeniden difüzyon) yeniden artar. Gaz basıncı ile bileşim alanının kalınlığı kontrol edilir.
Malzeme transferi ve iş parçasının ağırlığının artış veya azalışı saçınma ve kondensasyon ile kontrol altına alınır.
Azot Difüzyonu (Implantasyon)
Uzun işlem sürelerinin kısaltılması için gaz ile nitrürasyon yapılmış ve azotun çarpışma prosesinde hızlanma gözlenmiştir.
İyon nitrürasyon azotun çarpışma süresini azaltmıştır. İyon nitrürasyon prosesinin başlangıcında iş parçası yüzeyinde azotça zengin FeN gazı yoğunlaşmaya başlamıştır. Oluşan ani ayrışma azotun iş parçasına doğru difüzyonuna neden olmuştur. Gaz ile nitrürasyonda, yüzeydeki azot konsantrasyonun belirlenmesinden sonra katı gazdaki çözelti ferrit ile birleşerek azot içeriğinin artmasıyla beraber Fe4N, Fe3N, Fe2N gazlar oluşur. Bu reaksiyonlar çok kısa zamanda oluşur.
Benzer olaylar aynı nedenlerden ötürü düşük sıcaklıklarda yapılan iyon nitrürasyonunda kompakt, koherant demir nitrür tabakaları kısa sürede oluşacaktır.
Yüzeye yapışan FeN yoğunlaşır ve sonuçta azot yüksek yüzey konsantrasyonuna sahip olarak başlangıçta çok küçük değişikliğe uğrar. Deneyler göstermiştir ki 10 saat ve daha uzun zamanlarda azot, iyon nitrürasyon prosesinde gaz ile nitrürasyona göre daha hızlı difüze olmaktadır.
Yine deneyler neticesinde azotun nüfuzyet derinliği, demir içinde azotun difüzyonuna etki eden sıcaklığa bağlı olarak gözlenir ve sıcaklık artışı ile nüfuzyet derinliği artar.
Elektron mikroskobunda yapılan incelemelerde gaz nitrürasyon prosesinde, tane sınırları boyunca azot difüzyonu görülür. İyon nitrürasyonunda azotun çoğu taneler arası difüzyona uğrar. Böylece plazmada oluşacak iyon nitrarasyon ile oluşacak kondensasyon iş parçası üzerinde gözlenecektir. Böylece yüzeyde kısmi karbon saçınım prosesi oluşur. Karbon tane sınırları boyunca hareket ederek karbon difüzyonuna yol açar ve yüzeye yakın bölgelerde tane yapısı de karbürizasyona neden olur ve karbonitrür fazlan tane sınırı boyunca difüze olmamıştır. Diğer bir etkide karbonitrür nüfuziyeti yüzeye yakın tane sınırlarında (100 pm'ye yakın) oluştuğunda nitrür ile sertleştirilmiş yüzey tabakasının gevrekleşmesine neden olur.
Diğer iki etki de azotun hızlandırılmış difüzyon ile yüksek yüzey konsantrasyona sahip azot farklı difüzyon mekanizmalarla yüzeye difüze olur.
İyon Nitrürasyonunda Kullanılan Gaz Karışımları
Üç tip gaz çeşidi kullanılmaktadır.
Beyaz Tabaka'nın Oluşmadığı Gaz
%5 veya daha az azot geri kalanı soygaz (Ar) olan karışımıdır. Bu bileşimde oluşan bileşik tabaka nital ile dağlandıktan sonra demir nitrürler gözlemlenir. Yüzeyde ise nitrür çökeltilerinin (Cr-Mo-Al-V-Ti) difüze hali gözlenir. Bu gaz bileşimi takım çeliklerinde kullanılır.
Gamma Primegas
% 15 - 30 azot ve diğer kısmı % 70- 85 hidrojen olan bileşik gazdır. Bu gaz bileşimi, ince bir monofaz gamma prime tabakası ve Fe4N kristal yapısı oluşturur. Burada gamma prime kristal yapısı çok ince bir tabakadır ( 0,0001 - 0,0004"). Süre uzun tutulduğu ve yüksek sıcaklıklara çıkıldığında tabakaların kalınlığında artış gözlenecektir. Örneğin nitrürlenen çeliklerde de (Nitralloy 135 - 4140) bu tabaka gözlenmektedir.
Epsilon Gas
% 60-70 azot , % 1-3 CH4 ve dengeleyici soygazın kullanıldığı bileşik gazdır. Bu gaz bileşimi, monofaz ve (Fe2-3 N) halinde kristal yapıda yer alır Fırında parça uzun süre tutulursa tabakada kalınlaşma görülür ve tabaka kalınlığı 0,0001- 0,0012" arasında değişim gösterir.
Yüksek sıcaklıklarda istenen kalınlığa çok kısa zamanda geçilir. Bu gaz bileşimi, alaşım elementi içermeyen (Cr, Mo, V, Al, Ti) çeliklere uygulanarak nitrürasyon işlemi gerçekleştirilir.
Tabakanın kristal yapı formasyonunun gazın veya banyonun bileşimine bağlı olduğu saptanmıştır. Bu yapılar her ne kadar metalurjik açıdan fakirseler de tek fazlı yapıya sahip oldukları için yüzeyi %100 istenen bileşimde tutmakta veya beyaz tabakayı oluşturmaktadırlar.
Bazı gaz karışımları ile yüzey özelliklerinde artış sağlanmaktadır. İyon nitrürasyonuna uğrayan yüzeyler gözeneksizdir. Böylece parça hem aşınmaya hem de korozyona dayanıklı hale gelmektedir.
İyon Nitrürasyonu Sonucu Elde Edilen Yüzey Özellikleri
İyon nitrürasyon iş parçasının aşınma özelliklerine etki eder. İyon nitrürasyon yumuşak çelik (Mild steel) veya Takım çeliklerinin aşınmaya karşı olan dirençlerine olumlu etki eder. Nitrürasyona uğramış parçalarda kama tipi aşınmaya karşı dayanıklı olup birazda çarpmadan doğan aşınmaya direnç gösterir.
Yüzeyde gözenekleşme, yüzeyde mevcut olan yağların aşınacak yüzeylerin temas noktalarında bulunmasıyla başlar. Kavitasyon aşınması ise yağların ortadan kaldırıldığı yüzeylerde gözlenir. Yüzeye amonyak eklenmesi gözenek oluşumunu hızlandırır.
İyon nitrürasyonu ile klasik nitrürasyondan % 40 daha iyi yorulma özellikleri elde edilmiştir.
Birçok nitrürasyon işleminde az veya çok hacimsel büyüme işlemi tespit edilir. 500°C in üstündeki bir Plazma iyon nitrürasyon işleminde gerilim giderme tavlaması yapılmıyorsa, plazma iyon nitrürasyon'da distorsiyon oluşmaz. Bu, dövme ve makine ile üretilmiş parçalar için aynıdır.
İnce uzun parçalar çeşitli biçimlerde ağırlıklar baz alınarak gerilim giderme işlemine tabi tutulurlar. Bu şartlar altında distorsiyon minimuma indirilir.
Et kalınlığı 10 mm' den küçük parçalar nitrürasyona uğramış yüzeyde kendi kendilerine etkili distorsiyona uğrarlar. Bu yüzden parça yüzeyinde sıkı kuvvetler altında dengeli bir şekilde işlem görürler.
Azotun difüze olması ile hacimde bir artış gözlenir. Yalnızca maraging çeliklerinde zaman tesiri altında hacimde azalma gösterirler.
Çapaklanma, azotun absorbsiyonu parça yüzeyinde pürüzlülüğün artışına neden olur. Yüzeydeki pürüzlülüğün miktarı 0,2 - 0,5 pm dir. Genel olarak bu durum basit bir polishing (parlatma) ile ortadan kaldırılır.
Statik burulma testleri yüzey sürekliliğinin ölçülmesine yarar. İlk çatlağın burulma açısı ile yüzeydeki bağı) süreklik ölçülür. Açık renkli beyaz tabakanın mevcut olmadığı süreklilik, gamma prime ve onu takiben epsilon gas’dan yüksektir.
Yüzeyde oluşan tabaka korozyon direncine olumlu etki eder. Plazma iyon nitrürasyon işlemi kromnitrür şeklinde kromun tüketilmesiyle krom alaşımlı çeliğin spesifik korozyon direncini azaltır.
Plazma iyon nitrürasyon yüzeyi porozitelidir. Çatlak yüzeyli ve diğer nitrürlenmiş yüzeylere göre korozyon direnci artmış yüzeydir.
Otomotiv endüstrisinde kullanılan dönel motorlara iyon nitrürasyon uygulanmış ve buradan çıkan hurdanın değerlendirilmesine çalışılmıştır. Otomotiv şirketleri hurdanın % 28'den %2'ye düşürülmesiyle performans ve parçanın boyutsal kararlılığında artış görmüşlerdir. Bu iyon nitrürasyonunun başarısıdır.
İyon Nitrürasyonun Uygulama Alanları
Parçaların aşınmaya olan dirençleri arttırılır. Plazma ile iyon nitrürasyon avantajları şunlardır:
1. Potansiyel çevrim sayısının düşürülmesi (%33-50) Nitrürasyon çeliklerinden düşüktür.
2. Distorsiyonun azaltılması.
3. Son yüzey taşlama işleminin azaltılması veya elimine edilmesi.
4. Düşük maliyetle parçaların metalurjik özelliklerinin iyileştirilmesi.
5. Bakır plakanın ve maskelemenin uygulanmaması
6. Gevrekleşme veya pullanmaya sebep vermeden yüksek oranda aşınmaya karşı direnç.
7. Kompleks şekilli parçaların homojen bir işleme tabi tutulması.
8. Çalışma maliyetlerinin azaltılması.
9. Çevresel problemlerin kontrol altına alınması.
10. Hurda çevriminin azaltılarak birçok kere tekrar edilmesi bu avantajlar yüzeyde oluşan oksit tabakasının kontrolüyle sağlanır. Bilinen banyolar ve gaz nitrürasyonunda, iyon nitrürasyon ile oluşan kristal yapının kontrolü mümkün olmamaktadır. Bu çeşitlilik gaz karışım bileşiminden ileri gelmektedir.
İyon nitrürasyonun endüstriyel uygulamaları plastik ve otomotiv sanayinde yaygınlaşmıştır. Buna göre kullanım yerleri şöyledir:
Plastik Sanayii
Krom kaplamalı kalıplar
Bimetal yüzey sertleştirilmiş vida
Paketlenmiş kalıplar
Otomotiv Sanayii
Valfler
Krank mili
Dişliler
Dövme kalıpları
İyon nitrürasyon prosesi aşınma veya mukavemet problemi gösteren parçalara uygulanır.
Plastik proses makinaları ve dönel motor pistonlarında kullanılan yöntemdir. Valfler, dişliler matkaplar vb. parçalara iyon nitrürasyon uygulanabilir. 42 Cr Mo4 çeliğinde 0,02 inç derinliğine iyon nitrürasyon yapılarak aşınma ve mukavemet problemi önemli ölçüde ortadan kaldırılmıştır. İyon nitrürasyonuna uğrayan dökme demir malzemeler en yüksek aşınma ve sürtünme direnci olan malzemelerdir.
Ck 45 ' ten imal edilen krank millerinin iyon nitrürasyon sonrası maksimum yorulma mukavemetine bakılmış, eğer gözenekli ise şafta su veya yağda su verme işlemi uygulanmıştır. Sıcak işlem gören çelik malzemelerle, takım çelikleri 530 °C de yaklaşık 20 dakika iyon nitrürasyonuna tabi tutulduğunda çalışma koşullarında yüksek çekme yeteneğine sahip olmaktadırlar.
İyon nitrürasyon düzeneği vakum kabı, vakum ve gaz soğutma ünitesi, doğru akım güç ünitesi ve kontrol ünitesinden oluşur.
Vakum kabının çapının yükseltilmesi, yüksek doğru alam veren güç üniteleri ile işlem hızlı olarak gerçekleştirilerek işlemin maliyetinde azalma gözlenir.
Aşınma olmadığı ve kabin duvarlarında nitrürasyon olmadığı takdirde maliyetlerde düşüş gözlenecektir.
Çabuk ve kolay maskeleme yöntemlerinin kullanıldığı iyon nitrürasyon yöntemleri hem maliyet hem de zaman açısından tercih edilir.
İyon nitrürasyon işlemi özel sertleştirme problemi olan parçalara uygulanır. Mükemmel aşınma, yüksek yorulma dayattım', ölçü kontrolünün gerektiği ve çekirdek (ana malzeme) özelliklerinin korunmasının istendiği yerlerde kullanılmalıdır. Parçalarda istenen özellikler daha geniş kontrol aralığı ile ayarlanır.
İyon Nitrürasyon İşleminde Elde Edilen Yüzey Tabakalarının Yapısı
İyon nitrürasyon sonrası, yüzey tabakaları makroskopik incelemeye tabi tutulmuş, iyon nitrürasyona uğramış demir esaslı malzemeleri maximum %10 alaşım elementi içeren malzemelerle elde edilmiş yapı ve olası tabaka modifikasyonlan makroskopik olarak rahatlıkla incelenir. En dış tabaka çok ince olup iyon nitrürler içermesine rağmen nital ile dağlanamadığı için mikroyapı fotoğrafında beyaz olarak gözlenir. Bu tabakaya beyaz tabaka adı verilir. Bu tabakanın hemen altındaki tabaka ise bileşim tabakasıdır. Diğer alan ise difüzyon alanı olarak adlandırılır. Azot demir kafesi içine dağılmış veya çökmüştür. Difüzyon bölgesinin kalınlığı, sıcaklık, zaman ve çeliğin alaşım içeriğine göre değişir. Çeşitli yapılarda iyon nitrürasyonuna uğramış yüzey tabakasının eldesi, voltajın, basıncın ve gaz karışımın kontrol edilerek saçınma oranı kontrol altına alınır.
Beyaz Tabaka
Nitrürasyon işlemi görmüş çeliğin yüzeyinden alınan kesit incelendiğinde yüzeyde beyaz bir tabaka gözlenir. Bu tabaka kesintisiz bir şekilde oluşmuştur. Yüzeyde azot miktarının azalması ile nitrür miktarı azalacağı için beyaz tabakanın altında nitrürler tane sınırlarında çökelir.
Çelik bileşiminde nitrür yapıcı elementlerin mevcudiyeti işlemin etkinliğini artıracağı için nitrürasyon çeliklerinin bileşimine alüminyum, krom ve molibden katılır. Nitekim deneyde kullanılan 8620 çeliği bu elementlere sahip bir çeliktir.
İş parçasının içerdiği alaşım elementi miktarına bağlı olarak ve işlem değişkenleri kullanılarak beyaz tabakanın kalınlığı 0-0.05 mm arasında değiştirilebilir. Beyaz tabaka, sürtünme ve yorulmaya karşı çok yüksek bir dayanıma sahiptir. Diğer nitrürasyon yöntemleri düşük sünekliğe sahip ve daha kalın şekilde gözlenir. Ayrıca beyaz tabaka kendi kalınlığına ve esas malzemenin yapısına bağlı olarak korozyon direncinde artış gösterir.
Azot veya azot-hidrojen gaz karışımları nitrürasyonda kullanıldığından Fe-N, hidrokarbonlar işlem esnasındaki gaza eklenirse Fe-C-N sistemleri dikkate alınır.
Bileşim tabakasına etkiyen en önemli faktörler nitrürasyona uğramış yapının düzgünlüğü ve tabaka kalınlığıdır.
Tabaka kalınlığının artışı tabakanın sünekliğini düşürür. Yukarıdaki faktörler dikkate alındığında, optimum özelliklerin bileşim tabakasının tek fazlı olması ve gerekli minimum tabaka kalınlığı eldesiyle sağlanabileceği gözlenerek aşınma korozyon dirençlerinde artış gözlenmiştir.
Difüzyon Bölgesi
Beyaz tabakanın altında sertliği ve azot konsantrasyonu az olan bölgedir. Bu bölge yüzeyden çekirdek malzemeye geçiş sağlar. Difüzyon bölgesi malzeme çıkışına ve işlem değişkenlerine bağlı olarak 0,75 mm veya daha fazla derinliğe sahiptir. Bu tabaka, mikrosertlik değeri çelik sertliğinden iki kat daha fazla olan ve yüzeyin altında uzanan bir tabaka olarak gözlenir.
Nitrürasyon boyunca alaşımlı nitrürlerin çökmesi neticesinde difüzyon alanındaki optimum sertlik ve süneklilikteki küçük düşüş ile gevreklik problemi önlenebilir.
Alaşımlı çeliklerin uygun yüzey sertleştirmesi; düzgün dağılmış ve çökelmiş alaşımlı nitrürler ile sağlanır. Eğer demir kafesi çözünmüş alaşım elementleri ki, örneğin Al, Cr, Mo, V içeriyorsa çökme, azot ve nitrürasyon sıcaklığına bağlı olarak yüzeydeki FeN kondensasyonuna ve yüksek orandaki kristaller arası azot difüzyonuna göre yüksektir. Böylece işlem esnasında kullanılan gazın içeriği de azot içeriğine etki eder.
Azotun demir kafesi içinde çözünebilmesi ve en yüksek konsantrasyona ulaşması için optimum iyon nitrürasyon sıcaklığı karbon çelikler için 550 - 850 °C'dir. Alaşımlı çelikler ise aynı şekilde nitrürasyona tabi tutulursa sıcaklık 400 - 550 °C olup çeliğin seçimi istenen sertlik aralığında tespit edilecektir.
İşlem süresi, alaşım içeriği ve nitrürasyon sıcaklığı difüzyon bölgesinin sertlik ve derinliğine etki eder. Malzemenin sahip olduğu süneklik değerindeki düşüşte akma noktası, su verilmiş ve temperlenmiş çeliklerin iyon nitrürasyon sırasında sünekliğinde bir kayba yol açar. Bu karbonitrür çökeltilerin ostenit tane sınırları boyunca yerleşmesinden kaynaklanır. Karbonitrür çökeltileri tanelerin mekanik özelliklerinde çökelti içermeyen bölgelere göre bir fark gösterirler. Kritik gerilmeler altında mikro çatlaklara ve sonunda yorulma kırılmasına yol açabilir. Bu karbonitrür fuları tane sınırları boyunca görüldüğü için gevreklik yaratabileceği dikkate alınarak karbon içermeyen gazın iyon nitrürasyonunda kullannılasıyla dekarbürizasyon denilen olay sağlanmaktadır. Saçınma oranı, işlemde kullanılan gazın bileşimi ile difüzyon bölgesinde düşük karbonitrür çökeltilerini oluşturabileceği için etki eden diğer bir faktördür. Karbonitrür çökeltileri ve bileşik tabaka; yüksek oranda saçınma oranı ile karbon içermeyen gaz kullanıldığında iyon nitrürasyon yapıldığını gösterir.
Nitrürasyona uğramış parçanın sünekliğinde nitrürlenmemiş yüzey dışında düşüş olduğu görülmüştür. Nitrürasyona uğramış yüzeylerin gevreklik testi burulma deneyi ile yapılır. Nitrürasyon ile sertleşme gösterecek yüzeylerde oluşacak maksimum gerilmelerden dolayı çapta artış gözlenecek ve burulma kesme gerilmelerini artıracaktır.
Tek fazlı bileşik tabaka ve difüzyon tabaka karışımı, tane sınırları boyunca geniş oranda serbest bir şekilde karbonitrür çökeltisi mevcut ise bu iş parçasının sünekliğini düşürür. Çok fazlı difüzyon ve bileşik tabakalar bir arada ise çok miktarda çökme oluşacağı için iş parçasında gevreklik yaratacaktır.
Termokimyasal dengeye bağlı olarak özel yüzey reaksiyonlarıyla oluşacak güçlü elektriksel alanla plazma fazını oluşturmak mümkündür.
Yüzey reaksiyonları; saçınma, iyonizasyon, vaktim kondensasyonu, gaz bileşimi, gaz basıncı, voltaj ve akıma göre gerçekleşmektedir. Proses şartları iyon nitrürasyonunda, azotun absorbsiyon ve difüzyon mekanizmalarına direk etki gösterir.
Azotla beraber diğer elementlerin yüzeye yerleştiklerinde kontrolleri mümkündür. Karbon plazmanın içeriğin etki ederek, Fe-N veya Fe-C-N sisteminde yer aldığı için azot kadarda önemli bir elementtir.
Yapının optimum adaptasyonu ve özellikleri kullanılan malzemenin tipine ve iş parçası üzerindeki yerel gerilimleri ve iyon nitrürasyon haline etki eder.