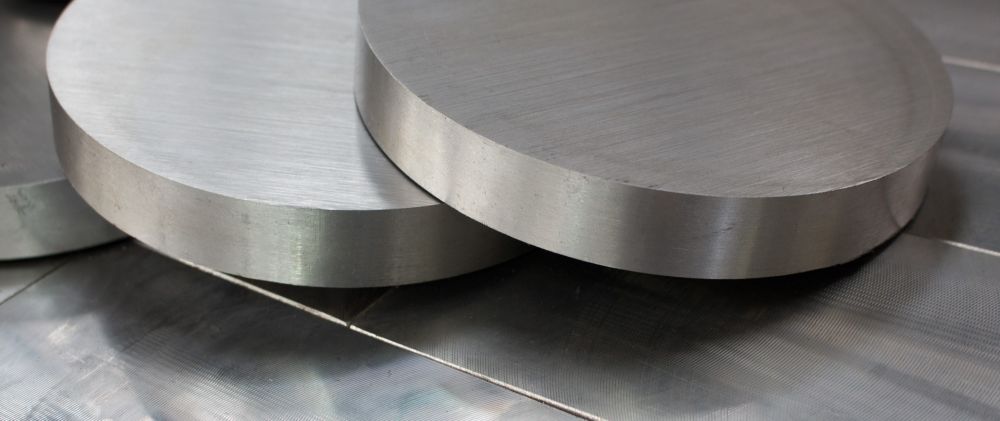
Birbirleriyle eş çalışan makina parçalarının yüzeylerinin çabuk aşınmaması için sert olması gerekir. Makina parçalarının çalışma sırasında darbeli yüklere dayanıklı olması gerektiğinden parçanın tümünün sertleştirilmesinden ziyade aşınmaya maruz kalan iç kısımlarının çeliğin normalize halinde, dış kısımlarının ise sertleştirilmiş halde olması istenir.
Bu işlemlerin gerçekleştirilmesi amacıyla yüzey sertleştirme işlemleri gerçekleştirilmiştir. Yüzey sertleştirme işlemi sonucunda parçanın aşınmaya olan direncinin artması ile hacim genişlemesi en aza iner, parçanın çarpılma tehlikesi azalır ve parçanın yanılma mukavemetinde artış gözlenir. Çünkü parçanın sertleştirilmiş yüzeyindeki tabakasında hacim artışı gözlenir ve parçanın iç kısmına doğru yüzeyi çeker ve yüzeyde basınç gerilmeleri oluşur; çalışma esnasında periyodik olarak parça eğilme veya çekmeye zorlandığında, bu basınç gerilmeleri neticesinde yüzeyde ortalama gerilme şiddeti azalacağından, parça yorulmaya karşı mukavemetli olur.
Yüzey sertleştirme işlemleri iki grup altında toplanabilir.
• Isı Birikimi ile Yüzey Sertleştirme İşlemleri
• Difüzyon ile Yüzey Sertleştirme İşlemleri
Isı Birikimi ile Yüzey Sertleştirme
Karbon içeriği %0,35-0,60 arasında olan sade karbonlu ve az alaşımlı makina yapım çeliklerine uygulanır. Bu işlem neticesinde çeliğin sertleştirilmesini sağlayan karbondur.
Çeliğin ısı iletiminin düşük olması yüzünden parçanın yüzeyine ve yüzeyinin sadece sertleştirilmesi istenen bölgesine kuvvetli bir ısı kaynağı uygulanırsa, parçanın bu bölgesi, ısı iletimi ile ısının çok az bir kısmı merkeze iletildiğinden hızla ostenitizasyon sıcaklığına ısıtılır. Bu ısınan kısımlara soğutucu bir akışkan püskürtülerek sertleştirme gerçekleştirilir. Neticede yalnızca ostenitize olmuş dış yüzey sertleşir.
Isı birikimi ile yüzey sertleştirme yöntemlerinden en çok kullanılanları alev ve endüksiyonla yüzey sertleştirme yöntemleridir.
Önerilen Makale: Paslanmaz çelik sac malzemeler ve uygulamaları hakkında detaylı bilgi almak için
çelik baklavalı sac fiyatları sayfamızı ziyaret etmenizi tavsiye ederiz.
Alev ile Yüzey Sertleştirme İşlemi
Bu yöntem ile ısıtmada oksi asetilen üfleçler kullanılır. Oksi asetilen alevinin sıcaklığı kullanılan karışım oranına göre 3000-3200 °C arasında değişir. Bu işlemde nötr alev kullanılır.
Küçük yüzeylerin sertleştirilmesinde üfleç alevi sertleştirilmesi gereken tüm yüzeyi kaplar ve ostenitizasyon sıcaklığına erişen parçanın yüzeyine su püskürtülerek sertleştirilir.
Bu yöntem ile sertleştirilen yüzeylerin sertliği çeliğin karbon içeriğine ve malzemenin içerdiği alaşım elementi miktarına bağlı olarak 50-64 Rc arasında değişir.
Bu yöntem kütleli ve uniform biçimli parçalarda iyi netice vermesine karşın küçük ve karışık biçimli parçalar için uygun değildir.
Endüksiyon Akımları ile Yüzey Sertleştirme İşlemi
Bu yüzey sertleştirme türünde ısıtma amacıyla parçanın yüzey kısmında oluşturulan endüksiyon akımlarından yararlanılır.
Bu işlemde iş parçası, endüktör adı verilen ince bakır borudan yapılmış, yüksek frekanslı akını ileten bir bobinin içinde tutulur. Parçanın yüzeyinde aynı frekansta fakat ters yönde endüksiyon akımı ortaya çıkar. Endüksiyon akımı parçanın tüm kesitinde uniform olarak dağılmadığı için yüzeyde çok yoğundur. Bu olay skin effect diye adlandırılır. Bu endüksiyon akımları hızla parçanın yüzeysel olarak ısınmasına neden olur ve ostenitizasyon sıcaklığına kadar ısınmış kısımlar hızla soğutularak, yüzeyde sert bir tabaka elde edilir.
Bu yöntem ile elde edilen sertliğin derinliği malzemenin özgül direnci, manyetik permeabilitesi, bobinin formu ve bobin ile iş parçasının yüzeyi arasındaki uzaklık ve frekans ile değişir. Sert tabakanın derinliğine etkiyen en önemli faktör, akımın frekansıdır, frekans yükseldikçe sert tabakanın derinliği azalır. Yüksek frekanslı akım bir vakum tüpü veya jeneratörler yardımı ile elde edilir.
Endüksiyonla yüzey sertleştirme işleminde iki ayrı yöntem uygulanır. Küçük parçalar veya parça üzerinde sadece küçük yüzeylerin sertleştirilmesi halinde iş parçası gereken büyüklükteki endüksiyon bobini içinde ostenitize edilir ve ardından soğutucu banyoya atılır. Karışık biçimli parçalarda ise en önemli konu kenar etkisidir. Bu durumda iş parçasının bobine yakın olan kısımlarında endüksiyon akımı yoğunluğu yükselir. Parça ısındığında, bu bölgeler daha derin ısınmış olduklarından, sert tabakanın kalınlığı artar. Bu olay parçada homojenliği bozar. Bu olayın önlenmesi amacıyla parçanın dış yüzeyine uyacak şekilde bobinler yapılır.
Alev ve Endüksiyonla Yüzey Sertleştirme Yöntemlerinin Karşılaştırılması
• Endüksiyon ile yüzey sertleştirme işlemindeki ısıl işlem süresi alev ile yüzey sertleştirmeye nazaran daha kısa olduğu için verimlilik artış gösterir.
• Endüksiyon ile yüzey sertleştirmede görülen şekil değişimi alev ile yüzey sertleştirmeye göre çok dalı azdır.
• Endüksiyon ile yüzey sertleştirmede parça yüzeyinde tufalleşme gözlenmez.
• Endüksiyonla yüzey sertleştirme işleminde sert tabaka kalınlığı daha kolay kontrol edilir. Frekans ayarı ile milimetrenin çok küçük bir kesrinden 75 mm kalınlığa kadar sert bir tabaka elde edilir. Alevle sertleştirmede sert tabaka kalınlığı bir milimetreden daha az yapılamaz ve kalınlık 10 mm'den daha fazla olamamaktadır.
Difüzyon ile Yüzey Sertleştirme
Alaşımsız az karbonlu bir çelik kullanmak ve sonrada yüzeyi difüzyon yolu ile alaşımlandırmak ve gerektiğinde ısıl işlem uygulayarak sadece alaşımlandırılmış yüzeyi sertleştirmek amacıyla yapılır.
Difiizyonla yüzey sertleştirme işlemleri çeşitli biçimlere aynlabilir.
• Sementasyon
• Nitrürasyon
• Karbonitrürasyon
• Borlama
Sementasyon
Az karbonlu çelik parçasının yüzeyine karbon emdirilmesine dayanan bir yüzey sertleştirme işlemidir. Karbon emdirilmesi işlemi çelik parçasının karbonmonoksit içeren bir ortamda, ostenit sıcaklığında tutulması olayına dayanır. Bu sıcaklıkta gaz, çeliğin yüzeyine difüze olur. Bu işlemin gerçekleştiği 850-950 °C arasındaki sıcaklığa sementasyon sıcaklığı adı verilir.
Bu sıcaklıkta oluşan karbonmonoksit, semente edilen çeliğin yüzeyinde 850-950°C' de parçalanır ve açığa çıkan atomsal karbon çelik tarafından absorbe edilir ve çeliğin içine difüze olur. Bu iki reaksiyon tersinir reaksiyonlardır.
Birinci reaksiyon olan karbondioksitin karbonmonoksite dönüşümü, sıcaklık düşüşü ile başlar. Çelik karbondioksit bakımından zengin bir atmosfer içinde kalacağı için, iç yapısındaki karbon, karbondioksit ile birleşerek karbonmonoksit oluşturur ki böylece yüzeyde karbon azalması ortaya çıkar. Bu olay dekarbürizasyon olarak bilinir.
Çeliğin yüzeyinde dekarbürizasyon tabakasının oluşumu yüzey sertleştirme işleminin başarısız olmasına yol açar. Dekarbürizasyon tabakasının oluşumunu önlemek için endotermik gaz karışımı kullanılır.
Çelik parça seçilmiş olan sementasyon sıcaklığında, yüzeyde istenilen karbonca zengin, sertleşebilir kabuk tabakası elde edinceye kadar geçen süreye sementasyon süresi denir. Sementasyon süresi boyunca, parçanın yüzeyinden itibaren iç kısımlara doğru ilerleyen karbonun ilerleme miktarına veya su verme neticesinde yüzeyde oluşan sert tabakanın kalınlığına sementasyon derinliği adı verilir.
Sementasyon işlemi özellikle sementasyon çeliğinden imal edilen dişliler, piston pimleri, zincirler, zincir dişlileri, makaralar, diskler, kılavuz yataklar, rulmanlı yataklar, orta şiddette zorlanan makina parçalarına uygulanır.
Semente edilen az karbonlu çelik, yüzeyde aynı sertliği veren yüksek karbonlu çeliğin kullanımına göre bazı avantajlara sahiptir:
• Parça kısmen veya tamamen son şeklini aldıktan sonra şekillendirilmesi oldukça kolay ve ekonomiktir.
• Semente edilen parçanın iç kısmı kolaylıkla işlenebilir.
• Sementasyon işlemi sırasında parçanın iç bölgeleri tokluğunu ve sünekliğini koruduğu için sertleştirme sonrasında ortaya çıkan çarpılmalar azalmıştır.
• Parça yüzeyinde sonradan işlenecek sertleştirilmesi istenmeyen kısımlar varsa, bu kısımlar özel bir pasta ile korunarak sementasyon esnasında karbon difüzyonundan korunur ve su verme işlemi sonrasında sertleşme göstermezler.
Sementasyon işlemi değişik karbon verici ortamlarda yapılabilir ve bunu göre yöntemler şöyle gruplandırılır.
• Katı ortamda sementasyon veya kutu sementasyonu
• Tuz banyosunda sementasyon
• Gaz sementasyonu
Kutu Sementasyonu
Semente edilecek iş parçaları çelik veya dökme demirden yapılmış olan kutu içinde odun kömürü ve reaksiyonu hızlandırıcı maddelerden oluşmuş karışımın içine gömülür ve hava atmayacak şekilde kapatıldıktan sonra fırına konur. Reaksiyon hızlandırıcı olarak baryum karbonat veya kalsiyum karbonat kullanılır.
Fırında sıcaklığın yükselmesi ile kutu içindeki odun kömürü havanın oksijeni ile birleşerek CO2 oluşturur. Oluşan CO2 odun kömürü ile tekrar reaksiyona girerek atomar karbon ve CO' ye ayrışır.
Atomar karbon ostenit yapıdaki çeliğin yüzeyine nüfuz ederek yapı içinde çözünür. Böylece çelik parçanın yüzeyinde karbon zenginleşmesi oluşur. Bu yöntem özellikle büyük ve tek parçalara uygun bir yöntemdir. Yöntemin dezavantajı ısıtma ve soğutma süresinin uzunluğu ile sementasyon tabakası kalınlığının O. 75 mm' den ince yapılamamasıdır.
Tuz Banyosunda Sementasyon
Tuz banyosunda yapılacak sementasyon için NaCl ve Na2CO3 karışımı tuzlar içine %25'i aşmayacak şekilde karbon verici olarak sodyum veya potasyum siyanür eklenir.
Bu yöntemde semente işlemi siyanür tuzlarının havanın oksijeni ile reaksiyona girmesi ile başlar.
Tuzun bileşimi ve karışım oranı sementasyon derinliği ve çalışma sıcaklığına göre değişir. İşlem sırasında yüzeye bir miktar azot gireceğinden bu işlemle semente edilen parçalar diğer yöntemlerle semente edilen parçalara göre daha dayanıklıdırlar. Bu yöntem özellikle seri imalatta küçük ve orta boy parçalar için kullanılır.
Gaz Sementasyonu
Gaz sementasyonu işleminde karbon verici olarak metan, etan, propan gibi hidrokarbonlar kullanılır. Aşağıdaki reaksiyonlar neticesinde ortaya çıkan atomar karbon, ostenit yapıdaki çeliğe nüfuz ederek karbonca zengin bir tabaka oluşturur.
Sementasyon tabakası kalınlığı parçanın fırın içerisinde kalma süresini göre değişir. Sementasyon sıcaklığından doğrudan sertleştirme işlemine geçilebilir. Çok temiz bir ortamda çalışmak mümkündür.
Nitrürasyon
Nitrürasyon işlemi azot içeren bir ortamda 480-650 °C'de parçanın yüzeyine azot emdirilmesi işlemidir. Bu işlem çeliğin yüzeyinde yüksek derecede sertliğe sahip bir tabaka oluşturmasının yanı sıra malzemenin yorulma mukavemetini, atmosfer, su ve buhar gibi ortamlardaki korozyon dayanımını arttırır. Nitrürlenmiş tabaka sertliği semente edilip sertleştirilen çelikten daha yüksek, boyutsal bakımdan daha kararlı ve sertliğini 500 °C'ye kadar koruma yeteneğine sahiptir.
Çeliğin bileşiminde nitrür yapıcı elementlerin bulunması işlemin etkinliğini arttırdığı için nitrürasyon çeliklerinin bileşimine alüminyum, krom, molibden katılır.
Nitrürasyon yöntemleri dört grupta incelenir:
• Gaz Nitrürasyonu
• Tuz Banyosunda Nitrürasyon
• Toz Nitrürasyonu
• Plazma Nitrürasyonu (İyon Nitrürasyon)
Gaz Nitrürasyonu
Nitrürasyona tabi tutulacak çelik parçalar özel nitrürasyon fırını veya özel sızdırmaz nikel, inkonel gibi alaşımlardan üretilen kumlar içine konularak elektrik fırınına yerleştirilir. Parçalar üzerinden amonyak gazı geçirilir. Amonyak gazı sıcaklığı 510- 520 °C’de tutulur, bunun nedeni amonyağın 500 °C'nin üstündeki sıcaklıklarda ayrışmaya başlamasıdır. 500-520 °C arasında amonyağın %15-25'i, 600-650 °C arasında ise %40-50 'si ayrışır.
Kullanılan gaz nem içermemelidir. Çünkü nem parçaların oksidasyonuna neden olur. Bu yüzden amonyak gazı sönmemiş kireç filtresinden geçirilir. Fırın ısıtılmaya başlandıktan sonra parçalar üzerindeki gaz akışı kontrol edilir. Fırından çıkan gazın bileşimi kontrol edilerek ayrışan amonyak miktarı tesbit edilir. Bu tesbitte esas alınan olay amonyağın su içinde çözünmesidir.
Nitrürasyon işlemi parçada istenilen sert tabaka kalınlığına bağlı olarak 10-90 saat sürer. Yalnız endüstrideki uygulamalarda 24 saatin üzerine çıkılmaz. Günümüzde nitrürasyon işlemlerinde amonyak azot hidrojen veya amonyak ve hidrokarbon gazlarının yakılması ile elde edilen endogaz karışımı atmosferleri kullanılır. Bu tür gazların kullanıldığı fırınlar özel türde olup bir gaz jeneratörü ile beraber yapılmıştır.
Tuz Banyosunda Nitrürasyon
Bu işlem esnasında sodyum, potasyum siyanür ve bir miktar karbonattan oluşan banyo kullanılır. Banyo 575 °C'de yaşlandırılır. Yaşlandırma sonucunda banyodaki siyanat miktarı istenilen seviyeye yükselince, parçalar içine daldırılır. Parçayı banyoda tutma süresi 2 saat olup banyo aşağıdaki reaksiyonlara göre parçaya azot verir.
Toz Nitrürasyonu
Parçalar nitrürasyon ve nitrürasyonu hızlandırıcı toz karışım içine gömülerek kutulara yerleştirilir. Kumlar kapatıldıktan sonra 520-570 °C'de 10-12 saat tutulur. Parça üzerinde oyuklaşma ve pullanma görüldüğünden tercih edilen bir yöntem değildir.
İyon Nitrürasyonu
Parçaların nitrürasyona tabi tutulması vaktim altında azot ve hidrojen gazlarının sisteme gönderilip iyonize olup parça yüzeyinde sert tabaka oluşturması esasına dayanır.
Karbonitrürasyon
Çelik parçalar karbon verici ve azot verici bir atmosferde 850-860 °C'de 2-10 saat tutulurlar. Parça yüzeyinde hem karbon hem de azot bakımından zengin bir tabaka oluşur. İşlem neticesinde su verme uygulanır. Karmaşık şekilli parçalara uygulanır.
Borlama
Borlama işleminde yüzeyi iyi temizlenmiş malzemelere 700-1000 °C'de 1-10 saat süreyle uygulanmaktadır. Borlama ortamı bor kaynağı dolgu ve deoksidantlardan oluşur. Aktivatörler tabakanın büyümesine etki eder. Dolgu ve deoksidantlar ise borlama sıcaklıığındaki oksijeni tutarak redükleyici ortam oluştururlar. Ayrıca borlama maddelerinin ana malzemeye yapışmasını önlerler.
Bor ile yüzey sertleştirme işleminin diğer yüzey sertleştirme yöntemlerinden üstünlüğü, yüzey tabakasının çok sert olmasının yanı sıra sürtünme katsayısının düşük olması, bazı baz, asit, metal eriyikleri ve yüksek sıcaklık korozyonuna direnç göstermesidir.