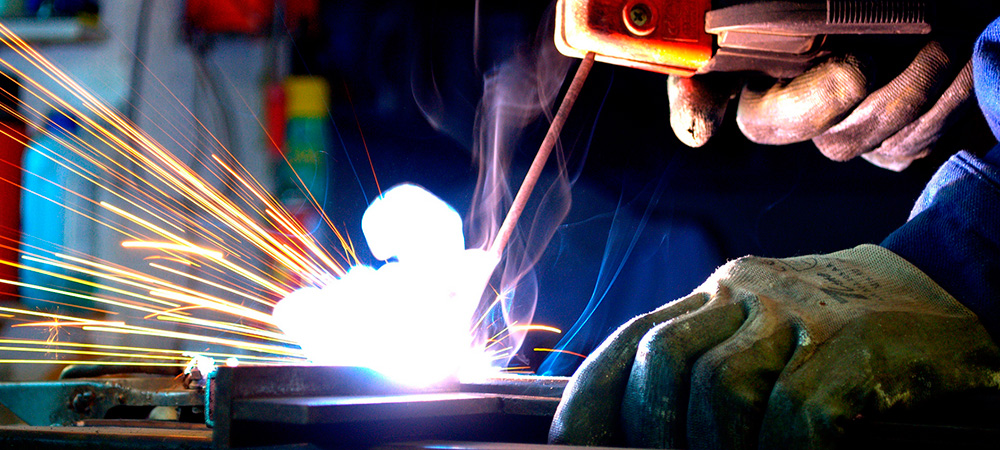
Direnç kaynağı, gerçekte oldukça eski bir kaynak yöntemidir. Bu yöntem 1877’de Birleşik Amerika’da bir rastlantı sonucu bulunmuş ve I. Dünya Savaşı’na kadar endüstride çok az kullanılmıştır. II. Dünya Savaşı’ndan sonra günümüze kadar direnç kaynağı yöntemlerinde ve özellikle elektrik devreleri ve zaman kontrol cihazlarında büyük gelişmeler olmuştur.
Otomotiv sektörü, uzay ve uçak teknolojileri, çelik yapılar, çelik eşya imalatı, hassas cihazların imalatı, elektroteknik, boru üretimi, makine sektörü gibi pek çok alanda kullanılan ince kesitli metal malzemelerin kaynağında yaşanan sorunlar, farklı kaynak türlerinin gelişimini sağlamıştır. İnce kesitli malzemeler yüksek ısı altında kaldıklarında kalıcı şekil bozukluklarına neden olur. Bu nedenle kaynaklama işleminin asgari ısıda ve en kısa sürede gerçekleştirme zorunluluğu ortaya çıkmaktadır. Kaynaklı bağlantıların hızlı bir şekilde en az deformasyonla gerçekleştirilmesi, ekonomik ve kaynak mukavemetinin yüksek olması istenilen yerlerde, elektrik direnç kaynağı ilk seçim olarak karşımıza çıkmaktadır.
Elektrik direnç kaynağı, seri imalata uygun ve oldukça yaygın kullanılan bir kaynak yöntemidir. Kaynak işlemi, bir düğmeye veya bir ayak pedalına basarak makineyi devreye sokan ve devreden çıkaran bir operatör tarafından büyük bir hızla gerçekleştirilir. Elektrik direnç kaynağı, metal parçalardan geçirilen elektrik akımına karşı, bu parçaların gösterdiği dirençten oluşan ısı yardımıyla yapılan birleştirmedir. Parçalar kısmi olarak ergitilerek kaynak için gerekli kaynak banyosu oluşturulur. Kaynak banyosunun oluşumundan itibaren elektrik akımı kesilerek iş parçalarına basınç uygulanır ve bu basınç altında soğuma gerçekleştirilerek sökülemeyen türden bir birleşim sağlanmış olur. Bu yöntemle yapılan kaynak işleminin genel adı elektrik direnç kaynağı olarak adlandırılır.
Genelde direnç kaynağı yöntemleri verimli ve az kirlilik yaratan yöntemlerdir. Özellikle ark kaynağı, gaz altı kaynağı, sert ve yumuşak lehimleme gibi diğer termik birleştirme yöntemleri ile kıyaslandığında kaynak başına düşen işçilik masrafı bu yöntemde oldukça düşüktür. Öte yandan direnç kaynak makineleri diğer kaynak yöntemleri için gerekli teçhizatın maliyetleri ile kıyaslandığında daha pahalıdır.
Direnç kaynağında Q = K x I
2x R x t ifadesi ile üretilen ısının tamamı kaynak işleminde kullanılamaz. Üretilen ısının bir kısmı kondüksiyon veya radyasyon yolu ile kaybolur. Bu denklemdeki direnç değerinin düşük olması durumunda, gerekli kaynak ısısını üretebilmek için yüksek şiddette akıma ihtiyaç vardır. Gerekli akım, yüksek gerilim ve düşük akım şiddetindeki elektrik gücünü, alçak gerilim ve yüksek akım şiddetine çeviren kaynak transformatöründen sağlanır. Basma kuvveti, kaynak akımını ileten elektrotlar vasıtası ile uygulanır. Bu kuvveti hidrolik, pnömatik veya mekanik düzenleyiciler sağlar.
Bütün direnç kaynak yöntemleri, uygun bir kaynak zamanı - akım şiddeti düzenlemesini gerektirir.
Kaynak sırasında çeşitli işlemlerin sırası, en genel halde şu şekilde ifade edilebilir: önce sınırlı bir metal hacminin erimesi için gerekli ısı miktarını elde etmek ve bundan sonra da bu metalin basınç altında yeniden soğumasıyla katılaşmasına olanak sağlamaktır. İş parçasının ısınma ve soğuma hızları, zaman tasarrufu ve ısı kayıplarının azaltılması bakımından mümkün olduğunca yüksek olmalıdır. Eğer soğuma hızı gevrek bir kaynak dikişi meydana getirecek kadar yüksek ise yine kaynak makinesinde gerçekleştirilen bir temperleme işlemine ihtiyaç duyulacaktır.
Önerilen Makale: Pirinç malzemeler ve uygulamaları hakkında detaylı bilgi almak için
pirinç otomat çubuğu nedir sayfamızı ziyaret etmenizi tavsiye ederiz.
Elektrik Direnç Kaynak Çeşitleri
Elektrik direnç kaynağı yapılış şekillerine ve sektörlerde en fazla kullanım alanlarına göre aşağıdaki gibi sınıflandırılır.
• Nokta (punta) direnç kaynağı
• Kabartılı nokta kaynağı
• Dikiş direnç kaynağı
• Direnç alın kaynağı
Nokta Direnç Kaynağı Yöntemi
Nokta kaynağı, direnç kaynağı türleri içerisinde en çok kullanılan türdür. Kaynatılacak parçalar iki bakır elektrot arasına alınır ve belirli bir baskı uygulanmasıyla elektrik akımının geçişi sağlanır.
Makine üzerindeki şalter ve zaman sayacı ile belirlenen süre boyunca, akım bir elektrottan diğerine akarken (1mm sac için bu süre yaklaşık 0,2 saniyedir) bu akıma karşı direnç, iki sac arasındaki temas noktasında en yükseğe ulaşır ve malzeme bu noktada ergimeye başlar. Elektrik akımının otomatik olarak kesilmesinden sonra kaynak banyosu, uygulanan basınç altında soğuyarak katılaşır ve iki sac malzeme sökülemez bir şekilde birleştirilmiş olur. Standart bir nokta direnç kaynak makinesinin temel bileşenleri, bakır elektrotlara yük uygulamak için kullanılan mekanik bir sistem, şebekeden gelen gerilimi düşüren transformatör, bazı makinelerde akım kontrol cihazları ve bir zaman sayacından oluşur.
Nokta direnç kaynağında elde edilen kaynağın şekli ve boyutları öncelikle elektrotun ucunun boyutu ve çevresi ile belirlenir. Kaynak çekirdeği iki parçanın temas yüzeylerinde meydana gelir ve dış yüzeylere kadar yayılmaz. Kesit alınırsa, uygun bir şekilde yapılmış kaynağın çekirdeğinin dış bükey mercek şeklinde olduğu görülür. Üstten görünüşü ise elektrot yüzeyinin şeklinde ve yaklaşık aynı boyuttadır.
Nokta direnç kaynak makinelerinin kullanıldığı sektörlerde değişen farklı istekler doğrultusunda farklı tipte, kapasitede ve donanımda nokta kaynak makineleri olabilir.
Nokta direnç kaynağında parça kalınlığına, türüne göre elektrot seçimi kaynağın kalitesini belirleyen önemli bir unsurdur.
Nokta kaynağı elektrotları;
• Elektriksel iletkenlikleri yüksek olmalıdır.
• Isıl iletkenlikleri yüksek olmalıdır.
• Yüksek mukavemet ve sertlikte olmalıdır.
• Kaynak edilecek malzemeyle alaşım oluşturma eğilimi düşük olmalıdır.
Saf bakır yüksek elektriksel ve ısıl iletkenliğe sahiptir ancak yumuşaktır ve aşınması kolaydır. Birçok elektrot bakır alaşımıdır. Elektrot malzemeleri 2 grupta sınıflandırılmıştır:
a) Bakır alaşımları (I, II, III, IV, V):
I. Nokta kaynağı için Cu – Cd alaşımı (iletkenlik %80): Al, Mg alaşımları, galvaniz kaplı çelik, pirinç ve bronz kaynağı için uygundur.
II. Nokta ve dikiş kaynağı için Cu – Cr alaşımı (iletkenlik %75): Düşük karbonlu çelikler, düşük alaşımlı çelikler, paslanmaz çelikler, nikel ve monel için uygundur.
III. Projeksiyon kaynağı için Cu – Zr alaşımları (iletkenlik %45, mukavemet ve sertlik II.’den yüksek): Paslanmaz çelikler için uygundur.
IV. Sert, yüksek mukavemetli alaşımdır, özel uygulamalarda tercih edilir (iletkenlik %20).
V. Döküm elektrotlardır, mukavemetleri çok yüksektir (iletkenlik %15).
Kompozisyonları sinterlenmiş bakır ve tungsten içerir. Yüksek sıcaklıklardaki aşınma dirençleri ve basma mukavemetleri için dizayn edilmişlerdir. İletkenlikleri düşüktür.
Bu yöntemle 12 mm kalınlığa kadar çelik sacların, 1 mm kalınlığa kadar bakır levhaların ve 5 mm kalınlığa kadar alüminyum levhaların kaynağı yapılabilmektedir. Bakır ve alüminyumun yüksek ısıl iletkenlikleri ve düşük elektrik dirençleri daha kalın levhalarda kaynak işlemini zorlaştırmaktadır.
Kaynak noktasının oluşumundaki temel prensip Joule yasasıdır. Bu ifadede verilen R, kaynak akımının bir elektrottan diğerine geçerken karşılaştığı elektrik dirençlerinin toplamıdır. Uygulanan akıma karşı gösterilen dirençler esas olarak iki türlüdür:
a) Kullanılan malzeme dirençleri
b) Temas dirençleri
Malzeme dirençleri, kaynak yapılacak malzemenin ve elektrotların öz direncine, akım yolunun büyüklüğüne (elektrot çapı, levha kalınlığı) ve akım yolundaki sıcaklığa bağlıdır.
İki iletkenin temas alanı boyunca ortaya çıkan temas direnci, sadece sıcaklığa ve malzemeye değil aynı zamanda yüzey şartlarına ve elektrot kuvvetine bağlıdır. Bu direnç, yüzeylerin doğal pürüzlülükleri nedeni ile akım yollarının, temas yüzeyindeki gerçek metalik temasın olduğu çok küçük temas noktaları boyunca daralmasıyla ortaya çıkan daralma direnci ve parça yüzeyleri üzerinde mevcut bulunan oksit filmlerini meydana getirdiği film direnci toplamına eşittir. Kaynak akımı öncesi uygulanan elektrot kuvveti arttıkça, temas yüzeylerindeki oksit filmlerinin parçalanması, temas noktalarının alanlarının artması ile temas direnci azalır.
Bu dirençlerden en büyüğü levhalar arası temas direnci olduğundan başlangıçta en fazla ısı burada üretilir. Bu bölgede sıcaklığın yükselmesi, bölgenin iç direncini de artırdığından ısı üretim hızı diğer bölgelere nazaran daha büyük olur. Bu nedenle, erime ilk defa levhalar arası temas yüzeylerinde başlar ve levha içine doğru gelişir. Kullanılan elektrotların yüksek ısıl iletkenliğe ve düşük elektrik direncine sahip olması ve su ile soğutulması nedeniyle elektrotlarla levhalar arasındaki temas yerinde herhangi bir erime meydana gelmez.
Kabartılı Nokta Kaynağı
Kabartılı nokta kaynağı, yöntem olarak nokta direnç kaynağına benzer. Nokta direnç kaynağında kaynatılacak sac malzemeler üst üste bindirilip, elektrotlar arasında sıkıştırılıyor ve elektrik akımı geçiriliyordu. Bu yöntemle elektrot başlıklarının boyut ve şekilleri geçen akımı sınırlandırırken kabartılı nokta kaynağında akım kaynatılacak malzemelerin en az birinde bulunan kabartılarla sınırlıdır.
Kabartılı kaynak yönteminde kaynak bölgesi, kaynak yapılacak saclardan birinde bulunan kabartının olduğu bölgedir. Saclar üst üste bindirildiğinde sadece kabartının olduğu noktadan birbirlerine temas eder. Bu noktadan geçen elektrik akımı kabartı üzerinde yoğunlaşır ve bu nedenle kabartı hızla ısınır. Isınmadan dolayı kabartı ergiyerek çöker ve iki sac arasında erimiş bir bölge oluşur. Elektrik akımı kesilerek basınç uygulamaya bir müddet daha devam edilir ve kaynak tamamlanır.
Kabartılı nokta kaynak makineleri, temelde nokta kaynak makineleri ile aynıdır. Ancak bu yöntemde nokta kaynağında kullanılan elektrot tipleri yerine eşit basınç uygulanabilen yassı elektrotlar kullanılır. Kabartılı nokta direnç kaynağı, saç yapılara küçük bağlantı parçalarının birleştirilmesinde kullanılır. Bu yöntem özellikle otomotiv sektöründe, sabit somunların şasiye bağlantılarında, ev aletlerinin vida bağlantılarında, büro mobilyalarında, makine parçalarının imalatında, dişli saplamalarda vb. pek çok alanda kullanılmaktadır. Kabartılı kaynak yöntemi inşaat sektöründe takviyeli beton uygulamalarındaki çelik hasırların üretiminde de kullanılmaktadır.
Genellikle nokta direnç kaynağı ve kabartılı nokta direnç kaynağı seri üretimde kullanıldığından, elektrotlardan geçen akımın oluşturduğu dirençten dolayı elektrotlarda ısınma oluşur. Elektrot ısısının artması kaynağı olumsuz yönde etkileyeceğinden soğutulmaları gerekir. Kaynak makinelerinde soğutma sistemi olarak genellikle su kullanılır. Bu sistem, makine içerisinde bir düzenekle sürekli olarak su dolaşımı ile elektrotların soğutulmasını sağlar.
Kullanıma bağlı olarak zaman içerisinde kaynak elektrotları aşınır. Aşınma sonucunda elektrotun ucu bozularak akım ve basıncın azalmasına neden olur, bu da yine kaynak kalitesini olumsuz etkileyen unsurlardan biridir. Bu durum, elektrot uçlarının periyodik olarak bakımlarının yapılmasını gerektirir. Bakım işlemi bozulan uca yeniden eski formunun kazandırılması ve akım geçişini engelleyen unsurların ortadan kaldırılması ile gerçekleştirilir. Bu işlem eğe, zımpara vb. araçlarla yapılır.
• Kaynak yapılacak iş parçaları elektrik akımının geçişini engelleyecek her türlü yağdan, kirden, boyadan ve pastan temizlenmelidir. Bu temizlik işlemi tel fırça veya zımpara yardımıyla yapılır. Kaynak makinesi çalıştırılır ve kaynatılacak parçaların kalınlığına ve makine türüne göre değişen amper ve zaman ayarı yapılır. Amper ve zaman ayarı için makine üreticisinin verdiği bilgilere başvurulmalıdır.
• Saclar kaynağa hazır hale getirilerek elektrotların arasına uygun şekilde yerleştirilir.
• Elektrotlar iş parçasına doğru yaklaştırılır ve parçalar sıkıştırılır. Böylece saclar birbirine temas ettirilir.
• Sıkıştırma olarak adlandırılan bu bölümde uygulanan basınç, biraz daha artırılarak elektrik akımının geçişi otomatik olarak başlatılır. Parça türü ve kalınlığına göre ayarlanan amper ve zaman dahilinde akım geçişi sürerek parçayı ısıtır. Bu süre genelde 1 saniyeden daha azdır.
• Elektrotların iş parçalarına baskı yaptığı noktadaki ara yüzeyde ergime başlar. Zaman sayacına bağlı olarak geçen akım, otomatik olarak kapanarak ergiyik baskı kaldırılmaksızın soğumaya bırakılır, bu süre birkaç saniyedir.
• Elektrotlara uygulanan basınç kaldırılarak elektrotların birbirinden uzaklaşması sağlanır. Bu süreçte kaynak işlemi gerçekleştirilmiş olur. Kaynak bölgesinin temizlenmesi isteniyorsa genelde tel fırça veya zımpara kullanarak kaynak temizliği gerçekleştirilir.
Dikiş Direnç Kaynağı
Dikiş direnç kaynağı, yapım tekniği bakımından nokta direnç kaynağına benzer. Nokta kaynağında ardışık olarak noktaların sıralanması dikiş direnç kaynağını oluşturur. Dikiş kaynağı, nokta kaynağındaki gibi birbiri üzerine bindirilen saç parçaların, temas yüzeylerinden geçen elektrik akımına gösterdiği direnç ile ergiyerek basınç altında birleştirilmesidir. Kaynağı yapılacak olan saç malzemeler, bakır alaşımdan yapılmış disk biçimindeki iki elektrot arasına konularak pnömatik veya hidrolik bir sistemle sıkıştırılır. Bakır disk elektrotlar dönmeye başladığında elektrik akımı da verilerek kaynak işlemi gerçekleştirilir. Tekerleklerin dönmesi sırasında akım kesilerek dönme devam ederse aralıklı dikiş kaynağı yapılmış olur. Sürekli elektrik akımı kullanılırsa kesintisiz bir kaynak birleşimi sağlanır. Bu tür kaynaklar sıvı ve gazlar için sızdırmazlık özelliğine sahiptir. Elektrotların soğutulması merkezi bir dolaşım sistemi ile veya elektrot üzerine su püskürtülerek yapılır. Soğutma sıvısı olarak %5 oranında bor yağı karışımı su kullanılır. Dikiş direnç kaynağında amper ayarı kaynatılan malzemenin cinsine, kaynatma hızına, kaynatılan malzemelerin kalınlığına ve soğutma suyu olarak kullanılan sıvının miktarına göre farklılıklar gösterebilir. En uygun amper ayarını deneme yanılma yoluyla bulmak, en uygun yöntemdir.
Kabartılı nokta kaynağı veya nokta direnç kaynağı ile farklı kesitli ve farklı türde malzemeler birbirlerine kaynak yapılabilir. Yuvarlak kesitli bir malzeme saca veya yine kendisi gibi yuvarlak kesitli bir malzemeye kaynatılabilir. Kaynatılacak malzeme kesiti yuvarlak, kare, dikdörtgen, bombeli vb. olabilir. Farklı kesite sahip malzemelerin kaynaklanmasın da elektrot çeşidi, amper ve zaman ayarlaması önem kazanmaktadır.
Direnç Alın Kaynak Yöntemi
Direnç alın kaynağı yönteminde, kaynağı yapılacak iş parçaları hareketli olan bakır alaşımlı çenelere sıkıca bağlanır. Bu yöntemde de elektrik akımı hareketli çeneler üzerinden iletilir. Kaynak işlem başlangıcında elektrik akım devresi açılarak, hareketli çeneler ile iş parçaları yüzeyleri arasında küçük bir boşluk kalıncaya kadar birbirine yaklaştırılır. Düzgün olmayan yüzeydeki birkaç çıkıntıdan iş parçalarının birbirine teması sağlanır. Temas eden bu noktalardan şiddetli akım geçerek temas noktalarında ergime ve kısmen buharlaşma meydana gelir. Temas noktaları kıvılcım ve patlama halinde parçalanır ve metal damlacıkları dışarı fırlatılır. İş parçalarının yüzeyini ısıtan arklar bu şekilde oluşur. Aynı zamanda oluşan metal buharı, kaynak bölgesini kaplayarak havanın olumsuz etkilerinden kaynak bölgesini korur. İş parçalarının hareketli çenelerle yavaş yavaş birbirine yaklaştırılmasıyla oluşan yeni temas noktaları da yanarak tüm kesitte kaynak ısısına ulaşılır. Bu noktadan sonra hareketli çeneler basınçla itilerek iş parçaları birbirine bastırılır ve elektrik akımı kesilir. Kaynak için geçen süre birkaç saniyedir ve akım kesildikten sonra bir müddet daha basınç uygulanmasına devam edilerek kaynaklama işlemi tamamlanır.
Direnç alın kaynak yönteminin çeşitleri:
• Basınçlı direnç alın kaynağı
• Ön ısıtmasız yakma alın kaynağı
• Ön ısıtmalı yakma alın kaynağı
Basınçlı alın kaynağında parçalar yüksek bir basıncın etkisiyle temas etmeden elektrik akımı uygulanmaz. Yakma alın kaynağında ise parçalar henüz temas etmeden elektrik akımı uygulanır. Direnç alın kaynağı yöntemi genellikle boruların, yuvarlak kesitli malzemelerin, kare kesitli malzemelerin ve düz sacların birleştirilmesinde kullanılır. Bu kaynak yöntemi ile çelik ve alaşımlarının kaynağı başarılı olmaktadır. Kaynağı yapılacak iş parçalarının doğru bir şekilde kaynatılmasındaki en önemli faktör, iş parçalarının aynı doğrultuda olmasıdır. Aynı doğrultuya getirilmeden kaynatılan iş parçalarında eksenel kaçıklıklar oluşur, bu da kaynak kalitesini düşüren bir unsurdur. Elektrik akımını ileten, doğrultuyu ve kaynak için gerekli basıncı sağlayan hareketli çenelerin iş parçasını bağlama ve hareket ettirme yeteneği vardır. Kaynak sırasında oluşan yoğun akımdan dolayı bu çeneler ısınır ve soğutulmaları gerekir. Makine üzerindeki merkezi bir su dolaşım sistemi ile hareketli çenelerin soğutulması sağlanır.
Direnç Kaynaklarında Isı Dengesinin Ayarlanması
Elektrik direnç kaynak yöntemlerinde kaynatılacak parçaların aynı özellikte ve aynı kalınlıkta olması, ısının dengeli dağılımı sonucunda kaliteli bir kaynak birleşimini sağlar. Ancak kaynağı yapılacak malzemelerin özellikleri veya kalınlıkları farklı olduğunda elektriksel direnç farklılıklarından dolayı kaynak istenilen kalitede olmaz. Bu durumda kaynak kalitesini belirleyen en önemli unsurlardan biri olan ısıyı, elektrotlar yoluyla dengeli bir şekilde dağıtmak zorunlu hale gelmektedir. Bunu sağlayabilmek için de geometrik şekilli elektrotlar ve değişik malzemelerden üretilmiş elektrotlar kullanmak gerekir.
Aynı özellikte, farklı kalınlıkta iki malzemenin kaynağında kalın parçaya elektrot daha az temas yüzeyi ile basarak elektrik akımının dengesi oluşturulmuştur. Bu örnekte eşit bir ısı dağılımı sağlanarak kaliteli bir kaynak elde edilebilir.
Aynı özellikte, farklı kalınlıkta iki parçanın kaynağında elektrot malzemesinin yapıldığı malzeme farklı olarak seçilmiş ve daha dirençli bir elektrot seçimi ile yukarıdaki örnekteki durumun tersi gerçekleştirilmiştir.
Farklı özellikte, farklı kalınlıkta iki malzemenin kaynağında kaynatılacak malzemelerin elektrik dirençlerinin bilinmesi ve buna göre elektrot tercihi yapılması gerekir. Direnci yüksek kalın malzemeye, daha geniş temas yüzeyi olan elektrot tercih edilmelidir.
Kaynak Çevrimi
Nokta direnç kaynağında kaynak çevrimi dört ana zaman diliminden oluşmaktadır. Bunlar;
1. Yaklaşma ve sıkma zamanı: Elektrotların birbirine yaklaşıp iki sacı sıkması için geçen süredir.
2. Kaynak zamanı: Birleştirilen saclara düşük gerilimde yüksek akım şiddetinde akımın uygulanma süresidir.
3. Tutma zamanı: Elektrotlar içerisinde su sirkülasyonu vasıtasıyla kaynak noktasının soğutulması ve bağlantının tam olarak meydana gelmesinin sağlanması için geçen süredir.
4. Ayrılma zamanı: Oldukça kısa bir süre olup parçaların diğer nokta kaynağı için hareket ettirildiği süredir.
Bütün bu zaman dilimlerinin süreleri periyot olarak ifade edilir. Frekansı 50 Hz olan bir elektrik akımında bir periyod 1/50 saniyeye karşı gelir.
Nokta Kaynak Kalitesini Etkileyen Kaynak Değişkenleri
Nokta kaynak kalitesini etkileyen değişkenler şunlardır:
• Elektrotların malzemesi ve boyutları
• Kaynak akımı ve kaynak zamanı
• Elektrot kuvveti
• İş parçasının malzemesi
• İş parçasının yüzey durumu
Elektrot Malzemesi ve Boyutları
Nokta direnç kaynağında, parça kalınlığına ve türüne göre doğru elektrot seçimi kaynağın kalitesini etkileyen bir unsurdur.
Ticari saf bakır en iyi iletkendir, saf bakır elektrotlar üstün mekanik özellikleriyle beraber, yeterli elektrik iletkenliğine sahip malzemeler elde edilinceye kadar direnç kaynağı elektrotu olarak kullanılmıştır.
Herhangi bir uygulama için belirli bir elektrot alaşımı seçimi, onun mekanik özelliklerine göre değişen ısıl ve elektriksel özelliklerinin de göz önüne alınmasıyla gerçekleşir. Örneğin, Alüminyumun kaynağı için kullanılan elektrotlar yüksek basma kuvveti yerine yüksek iletkenliğe sahip olmalıdır. Buna karşılık paslanmaz çeliğin kaynağı için kullanılan elektrotlarda maksimum basma mukavemeti elde etmek için iletkenlikten fedakârlık edilmelidir.
Levha kalınlığına ve malzemeye bağlı olarak elektrot uç çapları aşağıdaki bağıntıya göre hesaplanır:
a) Sivri, kubbe, düz, eksantrik ve kesik koni uçlu elektrotlar için:
S ≤ 3 mm için de = 5√S
S >3 mm için de = 2S + k
S > 7,5 mm için k = 2, S < 7, 5 mm için k = 3
Burada S, mm olarak levhanın kalınlığı, de mm olarak elektrot uç çaplarıdır.
b) Küresel uçlu elektrotlar için:
r (mm) küresel ucun yarıçapı olmak üzere,
r = k1 . s + k2
k1 . s ve k2 levha malzemesine bağlı sabitlerdir. Değerleri:
Yumuşak çelik ve paslanmaz çelik saclar için: k1 = 20 mm, k2 = 50 mm.
Alüminyum alaşımları için: k1 = 60 mm, k2 = 20 mm.
Magnezyum alaşımları için: k1 = 70 mm, k2 = 40 mm.
Küresel uçlu elektrotlar kullanıldığında elektrot temas yüzeyinin iş parçası yüzeylerine paralel olarak hassas bir biçimde ayarlanması gerekmez. Bu nedenle küresel uçlu elektrot üst, elektrotun dairesel hareket yaparak iş parçasına yaklaştığı kaynak makinelerinde rahatlıkla kullanılabilen bir elektrottur. Bu elektrot mükemmel bir sıkıştırma ve iş parçası yüzeylerinde kaynak sonrası daha iyi bir görünüm sağlar. Soğuma hızları daha yüksektir. Bu nedenle alüminyum ve alaşımlarının kaynağında kullanılır.
Kaynak Akımı ve Kaynak Zamanı
Kaynak bölgesinde belirli hacimdeki metali erime sıcaklığına ulaştırmak için ve bu sırada oluşan ısı kayıplarını karşılamak için toplam ısı ifadesindeki R direnci malzemeye, levha kalınlığına, elektrot kuvvetine ve elektrot uç çapına bağlı olup, değeri artan elektrot kuvveti ile azalmaktadır. Şu halde, verilmiş bir elektrot kuvveti ile levha için gerekli ısı miktarını elde etmek amacı ile değiştirilebilecek kaynak parametreleri, kaynak akımı ve kaynak zamanıdır. Başka bir deyişle erimenin meydana gelebilmesi için minimum akım yoğunluğu mevcut olup, bu değer malzemenin cinsine, kalınlığına ve kaynak bölgesine etki yapan elektrot basıncına bağlıdır.
Verilmiş bir elektrot basıncı için, akım yoğunluğun bir üst sınırı da mevcuttur. Bunun üzerindeki değerlerde kaynak bölgesindeki erimiş metal, levhalar arasında, bölge dışına doğru fışkırır. Bu olay kaynak dikişinde dayanıklılık azalmasına sebep olur. Elektrotlarla levhalar arasındaki temas yüzeylerinde erime meydana gelir, elektrotlar levhalara yapışarak tahrip olurlar.
Kısa kaynak zamanı ve yüksek akım şiddeti kullanılarak veya uzun kaynak zamanı, düşük akım şiddeti kullanarak aynı nokta çapı elde etmek mümkündür. Bunlardan ilkine kısa süreli kaynak, ikincisine ise uzun süreli kaynak adı verilir.
Getirdiği büyük faydalar yüzünden kısa süreli kaynak yöntemi çok gelişmiş olup, büyük ölçüde kullanılmaktadır. Önceleri çok ince levhalar için bile birkaç saniye olan kaynak zamanı, kontrol organları ve akım devrelerindeki büyük gelişmelerden sonra birkaç perioda kadar düşürülmüştür ( 1 period = 1/50 sn.dir). Kaynak zamanı azaldıkça, ısı kayıpları da azaldığından işlemin ısıl verimi artmaktadır. İşlemin hızlı olması nedeni ile sadece kaynak bölgesi erime sıcaklığına ulaşır ve levhaların dış yüzeylerinde aşırı ısınma olmadan kaynak işlemi sona erer. Bu nedenle elektrotların dokunma yüzeyleri bozunmaz.
Kısa süreli kaynak, ısının çok sınırlı bir yerde yoğunlaşmasının gerektiği özel koşullarda ve alüminyum gibi ısıl iletkenliği çok yüksek olan malzemelerin kaynağında özellikle tercih edilir.
Uzun süreli kaynakta kaynak bölgesine komşu bölgelerde sıcaklık yükseldiğinden, sıcaklık farkı, dolayısıyla da kaynak sonrası soğuma hızı düşüktür. Bu nedenle % 0,3 C’lu çeliklerde ve bazı alaşımlı çeliklerde sertleşmeyi önlemek için uzun süreli kaynak kullanılır. Diğer taraftan elektrotlar tarafından sıkıştırılması zor olan parçalarda da uzun süreli kaynak tercih edilir.
Elektrot Kuvveti
Elektrot kuvveti, levhaların elektrotlar altında belirli bir alanda temas etmesini sağlayarak kaynak noktasının kesin yerini belirler. Kaynak safhasında elektrot kuvvetinin görevi, levhalar arasından fışkırmaya çalışan sıvı metali, katı haldeki metal çukuru içinde basınç altında tutarak bu fışkırmayı engellemektir. Dövme safhasında ise kaynak dikişinin sıvı halden itibaren soğuması ve katılaşması sırasında büzülme nedeniyle ortaya çıkabilecek boşluk, çatlak gibi kusurların oluşumunu önlemektir.
Elektrot kuvvetinin artması, levhalar arası temas direncini azaltacağından kaynak akımının artırılmasını gerektirir. Diğer taraftan çok yüksek elektrot kuvveti, levhalarda istenmeyen distorsiyonlar ortaya çıkarır.
İş Parçası Malzemesi
Metallerin bileşimi, onların özgül ısılarını, erime sıcaklıklarını, gizli erime ısılarını, ısıl ve elektrik iletkenliklerini ve yoğunluklarını etkiler. Metallerde elektrik ve ısıl iletkenlik genelde aynı yönde paralel olarak değişir. Bu nedenle yüksek elektrik iletkenliği ve yüksek ısı iletkenliğine sahip bakır, gümüş, alüminyum gibi metallerde yüksek akım yoğunluğunda dahi üretilen çok az ısı çevreye hızla yayılır ve erime için gerekli ısı birikimini engeller. Bu ise kaynak işlemini imkansız veya zor bir hale getirir. Diğer taraftan mevcut birçok metalin birim kütlelerini erime sıcaklığına yükseltmek için gerekli ısı miktarı aynı mertebededir. Örneğin Alüminyum ve Paslanamaz Çelik gibi oldukça farklı nokta kaynağı özelliklerine sahip iki metali erime sıcaklıklarına getirmek için birim kütleleri başına yaklaşık aynı miktarda ısı vermek gerekir. Bununla beraber alüminyumun elektrik ve ısıl iletkenliği paslanmaz çeliğe nazaran sırasıyla yirmi ve on defa daha büyüktür. Bu nedenle, alüminyum için gerekli kaynak akımı paslanmaz çelik için gerekli olandan oldukça fazladır.
İş Parçasının Yüzey Durumu
Kaynaklanacak iş parçalarının yüzey durumu temas dirençleri yoluyla ısı üretimini etkiler. Eğer yüzeyler temiz ise belirli bir uygulamada daima aynı kalitede kaynak noktası elde edilir. Yüzeyi üzerinde oksit, pul gibi oluşumlar bulunan iş parçası, değişik kalitelerde noktaların oluşumuna yol açar, bu maddeler akımın iletimini zorlaştıracağı gibi elektrotların yüzeylerine yerleşerek elektrot ömrünü azaltırlar.
Kaynak Noktasının Mukavemeti
Nokta kaynağının statik mukavemetini tayin için aşağıdaki deneyler yapılmaktadır.
a. Çekme – makaslama deneyi
b. Haç biçimi çekme deneyi
c. U biçimi çekme deneyi
d. Burulma deneyi
Elektrik Direnç Kaynağında Kaynak Kabiliyeti
Elektrik direnç nokta kaynağında kaynak kabiliyeti deyimi kalite ve ekonomiklik açısından arzu edilen nokta kaynağının yapılabilmesi anlamına gelir. Elektrik direnç kaynağında, birleştirilecek parça, malzemenin cinsine göre elektrik akımının geçişine büyük bir direnç gösterir. Ohm kanununa göre ısıya dönüşen elektrik enerjisi aşağıdaki ifade ile belirlenir.
Ns = I2 x R
Burada; Ns: Isı enerjisine dönüşen elektrik enerjisi I: Kaynak yapılan parçadan geçen akım şiddeti, R: Kaynak yapılan parçanın elektrik direnci.
Bu ifadeyle birlikte, elektrik direncinin düşük olması durumda kaynak kabiliyetinin düşeceği sonucuna varılmaktadır.
Kimyasal bileşim kaynak kabiliyeti üzerinde 1. dereceden etkiye sahiptir. Nokta kaynak bağlantısının içyapısını, sertleşmesini, çekirdek oluşumunu, çatlak oluşumunu ve dayanımını etkiler.
Birçok durumda karbon eşdeğeri Ceş çeliklerin kaynak kabiliyetinin belirlenmesinde etkilidir. Alaşımsız ve düşük alaşımlı çeliklerde kaynak çekirdeğinin setliği karbon eşdeğeri yardımı ile belirlenir.
Karbon dışında diğer elementler de malzemenin kaynak kabiliyetini etkiler. Alaşım elementleri ilavesi, malzemenin nokta direnç kaynak kabiliyetinde düşmelere neden olabilmektedir.
Nokta kaynağında hızlı bir ısınma-soğuma çevrimi alaşımsız ve düşük alaşımlı ferritik/perlitik çeliklerde denge şartları altında oluşmayan faz dönüşümlerine yol açar. Kaynak çekirdeğini ve ısı tesiri altındaki bölgenin formu ve içyapısı, kimyasal bileşimi ve kaynaktan sonraki soğuma hızına bağlıdır.
Çeliğin yapısında buluna ve metalik olmayan oksit, sülfür gibi katışıkların biçimi, miktarı ve yapıdaki dağılımı, safiyet derecesini belirler. Kabul edilir sınırlar dahilindeki safiyet derecesi ve bunun kaynak esnasında ergimesi kaynak kabiliyetine olumsuz bir etki yapmaz ancak aşırı miktarlarda ergimelerde akım geçişi ve dolayısıyla kaynak çekirdeği oluşumu bozulabilir.
Elektrik ve ısıl iletkenlik malzeme direnciyle doğrudan ilgilidir bu nedenle nokta kaynağı kabiliyetini önemli oranda etkiler. Örneğin östenitik içyapılı çeliklerin elektrik iletkenliği, alaşımsız çeliklerinkine göre 6 kat daha düşüktür.
Çeliklerin yüzey durumu da direnç kabiliyetini etkilemektedir. Nokta kaynağında elektrot-iş parçası ve iş parçası-iş parçası arasındaki geçiş dirençleri sıcak hadde sonrasında çelik sacların yüzeylerinde düzensiz dağılmış cüruf ve hadde atıklarından etkilenmektedir. Örneğin bu atıklar eriyerek elektrot baskı yüzeyine yapışırlar ve yüzeyi düzgünsüzleştirirler.
Alaşımsız levha ve saclarda korozyona karşım koruma sağlayan ince yağ filmi gibi uygulamalar nokta kaynağı kabiliyetini veya elektrot ömrünü azaltmaz.
Östenitik paslanmaz çeliklerde sacların düzgünlüğü kaynak kabiliyeti açısından çok önemlidir. Yüzeyinin her yanı düzgün olmayan saclar kaynak esnasında homojen olmayan ısınmalar ve dolayısıyla ergime sırasında yüzeyde kuvvetli tav rengi gösterirler ve düzgün kısımlar ile tav rengi gösteren kısımlar arasında bir elektrokimyasal potansiyel ortaya çıkar. Bu ise korozyon direncin azalmasına neden olabilir. Kaynak sıcaklığına erişen bağlantı bölgesi üzerinde buluna herhangi bir yağ tabakası kaynak sıcaklığı nedeniyle eriyerek yüzeyin karbürlenmesine neden olur; bu ise malzemenin yüzeyi ile iç kısmı arasındaki kimyasal dengenin bozulmasına yol açar.
Çeliklerde sac kalınlığı da nokta direnç kaynak kabiliyetini etkilemektedir. 3 mm’ye kadar sac kalınlıkları nokta kaynak kabiliyetine sahiptir denilebilir. Aynı kimyasal bileşime sahip ve 3 mm’den kalın saclar nokta kaynağında sertleşmeye karşı daha büyük bir eğilim gösterirler. Bu durum kalın sacların daha yüksek ısı girdisi gerektirmesiyle ilintilidir. Sonuç olarak elektrotların soğuması için daha kısa süre kalması ve bu nedenle de elektrotların ısıyı iyi iletememesi sonucunda parçanın ısınsın düşmesi için daha uzun sürelere ihtiyaç doğması, saç kalınlığı arttıkça daha yüksek ısıl ve mekanik dayanıma sahip elektrotların kullanılması gerekliliğini doğurur.
Çeliklerin yüzey kaplamaları nokta direnç kaynak kabiliyetini etkileyen bir diğer faktördür. Metalik kaplamalar bakır elektrotların kalınlığının, homojenliğinin, bileşiminin, elektriksel iletkenliğin ve alaşımlanmasının nokta kaynağı işlemine etkisini artırıcı bir rol oynarlar. Elektrot yüzeyinin mekanik kaplama nedeniyle alaşımlanması, elektrot dayanımının azalmasına neden olur. Temas direncinin değişmesi, kaynak verilerinin uygun bir şekilde ayarlanması ihtiyacını doğurur. Organik kaplamaya sahip çelikler çinko tozu veya başka hafif pigmentler içeren yağlayıcı lak ile kaplanmış kaplamalar halinde olduklarından şartlı olarak nokta kaynağı yapılabilirler. Diğer lak türleri ile veya termoplastik malzemelerle kaplı çelik saclar nokta kaynağına uygun değildirler. Bunun gibi plastik ara tabakaya sahip kompozit malzemeler de son derece sınırlı bir nokta kaynağı kabiliyetine sahiptirler.
Malzemelerin ısıl iletkenlikleri, elektrik iletkenlikleri ve erime noktaları göz önüne alınarak nokta direnç kaynak kabiliyeti aşağıdaki şekilde ifade edilebilir:
S=104 / αλte
Burada ; S:Kaynak kabiliyeti faktörü α: Elektrik iletkenliği (m /Ω mm2 ) λ: Isı iletkenliği (cal /cm sn °C) te: Erime noktası (°C)
Yukarıdaki ifade ile kaynak kabiliyet faktörünün durumu aşağıdaki biçimde değerlendirilir.
0.25’e kadar Kötü
0.25-0.75 arası Yeterli
0.75-2 arası İyi
2.0’dan yukarısı Çok iyi
Çeliğin 1/3’ü, alüminyumun 2/3’ü ağırlığa sahip en hafif ticari metal olan magnezyum ve magnezyum alaşımları nokta direnç kaynağı ile hızlı, ekonomik ve korozyon tehlikesinden uzak bir şekilde kaynak edilebilirler. Ancak magnezyum alaşımları çelik, alüminyum ya da diğer metallere direnç kaynağı ile birleştirilemezler. Magnezyum alaşımları sadece kendileriyle özdeş veya benzer magnezyum alaşımları ile kaynak edilebilirler. Magnezyumun alüminyum veya diğer metallerle birleştirilme girişimleri gevrek intermetalik bileşik oluşumları ve korozyon teşvik edici kombinasyonların oluşum durumları nedenleriyle başarısızlıkla sonuçlanmıştır.
Magnezyumun nokta direnç kaynağında malzeme ve elektrotların yüzey temizliği oldukça önemlidir. Bunun için zımparalama uygulanır. Bu işlem, magnezyum ile elektrot arasındaki kaynama olayını azaltacaktır. Elektrottan magnezyum alaşımına kaynama sonucunda gerçekleşen bu alaşımlaşma olayı, magnezyumun korozyon dayanımını düşüren bir etkendir.
Bakırın kaynağı ise aşağıda belirtilen özelliklerinden dolayı özel bir önem arz eder:
• Yüksek ısıl iletkenliği,
• Yüksek ısıl genleşme,
• Sıvı halde gazları absorbe etmesi ile gözenek oluşumu.
Bakır ve alaşımları dokuz ana grupta toplanır:
• Saf bakır (minimum 99.3% bakır içerir),
• Yüksek bakırlı alaşımlar (en fazla 5% alaşım elementi içerebilir)
• Bakır-çinko alaşımları (Pirinç ya da sarı, en fazla 40% çinko içerebilir)
• Bakır-kalay alaşımları (Fosfor bronz, en fazla 10% kalay ve 0.2% fosfor içerir)
• Bakır-alüminyum alaşımları (Alüminyum bronz, en fazla 10% alüminyum içerir)
• Bakır-silis alaşımları (Silis bronz, en fazla 3% Si içerir)
• Bakır-nikel alaşımları (en fazla 30% nikel içerir)
• Bakır-çinko-nikel alaşımları (en fazla 7% çinko ve 18% nikel içerir)
• Özel alaşımlar (spesifik bir özelliği geliştirmek için alaşımlanmış malzemeler)