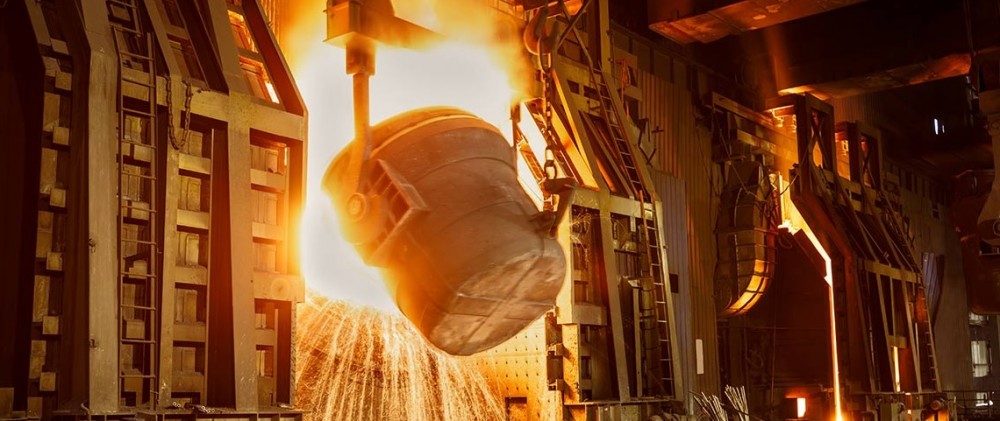
Martensitik dönüşüm, bazı demir ve demir dışı malzemelerin mevcut kristal yapısını aşırı soğutma sonucu başka bir kristal yapıya, fiziksel olarak kayma ile (difüzyon olmaksızın) dönüşümünü içeren bir katı hal dönüşümüdür. Aşırı soğutmanın yüksek oluşuyla ses hızına yakın bir hızla oluşan dönüşüm, tamamen ara yüzey kontrollü olup difüzyon şartlarına bağlı değildir.
Çeliklerde martensit oluşumu, östenit bölgesine ısıtılan çeliğin hızlı soğutulmasıyla yüzey merkezli kübik kristal (YMK) yapının aşırı gerilmeler sonucu distorsiyona uğrayarak hacim merkezli tetragonal dönüşümüyle gerçekleşmektedir.
Östenit (YMK) kristali kafesindeki değişim, C ve N gibi ara yer atomlarının varlığına bağlı olarak değişmektedir. C ve N atomları ara yer katı eriyiği olarak kristal kafesi içine yerleşmesiyle tetregonalin c eksenini a ve b eksenine dik yönde arttırarak dönüşüm sonrası hacim artışına neden olmaktadır.
c/a= 1.00 + 0.045C
c/a= 1.00 + 0.032N
C= % karbon oranı
N= % azot oranı
Dönüşüm esnasında oluşan kayma gerilmeleri kristal kafesin de elastik deformasyonlar meydana getirirken mikro derecede plastik deformasyonlar da meydana gelmektedir. Bu mikroplastik deformasyonlar da martensit sertliğini arttırmaktadır.
Maksimum %2 C çözünürlüğüne sahip olan östenit denge dışı ayrışmasıyla, bileşime ve soğutma şartlarına bağlı olarak belirli sıcaklıklarda martensit oluşumu başlar. T.T.T diyagramlarında gösterilen bu sıcaklığa Ms ve dönüşümün tamamlandığı sıcaklığa da Mf denilmektedir. Ms sıcaklığını belirleyen en önemli kriter ise malzemenin bileşimidir. Ms sıcaklığı değişen bileşim oranına bağlı olarak aşağıdaki bağıntıya göre hesaplanabilmektedir.
Ms (°C)= 561-474 [C]-33[Mn]-17[Ni+Cr]-21[Mo]
Ms-Mf aralığında dönüşüm devam ettiği için alaşım elementlerine bağlı olarak oda sıcaklıklarında ve hatta sıfır altı sıcaklıklarında dönüşüm tamamlanabilmektedir. Dolayısıyla oda sıcaklıklarındaki dönüşümlerde yapıda dönüşmeyen östenit kalabilmektedir. Su verme sonrası yapıda kalan dönüşmemiş östenit kararlı olmadığı için kullanım esnasında mekanik olarak martensite dönüşmektedir. Dönüşüm esnasında hac imsel olarak artma meydana geldiği için yapıda kalıcı gerilmelere neden olmaktadır.
Önerilen Makale: Çelik profil malzemeler ve uygulamaları hakkında detaylı bilgi almak için
hea çelik profil sayfamızı ziyaret etmenizi tavsiye ederiz.
Kalıntı Östeniti Etkileyen Faktörler
Alaşım Elementleri
Alaşım elementleri Ms-Mf sıcaklık aralığını, kalıntı östenit miktarı ve kararlılığını da etkilemektedir. Co ve Al hariç diğer tüm elementler Ms-Mr sıcaklığını düşürerek kalıntı östenit miktarını arttırmaktadır. Özellikle karbon tayinin % 1’lik artışında Ms sıcaklığı diğer elementlere göre on kat daha fazla azalırken, kalıntı östenit miktarı %50’ye kadar artmaktadır.
Östenitleme Sıcaklığı
Östenitleme sıcaklığı, Ms sıcaklığını ve kalıntı östenit miktarını önemli derecede etkilemektedir. Kuvvetli karbür yapıcı alaşım elementleri, östenit alanındaki serbest C oranını karbürler yaparak azalmaktadır. Östenit içindeki çözünmeleri sıcaklığa bağlı olduğundan düşük östenitleme sıcaklıklarında çözünmeler sınırlı olduğundan östenit içindeki C oranı nispeten düşüktür. Sıcaklığın yükselmesiyle alaşım karbürlerin çözünmesi ile östenit alanındaki C oranı artmaktadır. T alanında artan çözünmüş C oranı, Ms sıcaklığını düşürürken kalıntı östenit miktarının da artmasına neden olmaktadır.
Özellikle Cr oranı arttıkça, östenitleme sıcaklığının artışı ile kalıntı östenit miktarı oldukça arttırmaktadır. Östenitleme sıcaklığı serbest C'un yanı sıra serbest alaşım elementleri de Ms sıcaklığını düşürürken kalıntı östenit miktarını arttırmaktadır.
Soğutma Ortamı ve Sıcaklığı
Soğutma ortamı sıcaklığının değişimi östenitin kararlılığını etkilemektedir. Ms oda sıcaklığının altındaysa T-α dönüşümü tamamen tamamlanamadığı için yapıda dönüşmeyen östenit kalmaktadır. Benzer şekilde Ms-Mf aralığında Ms sıcaklığına yakın bölgelerde östenitin daha az dönüşümünden dolayı kalıntı östenit miktarı daha da fazla olmaktadır. Soğutma ortamının sıcaklığı Mf sıcaklığına yaklaştıkça kalıntı östenit daha az kalmaktadır.
Ms sıcaklığına bağlı olarak, kalıntı östenit miktarının soğutma ortamının sıcaklığı ile değişimi Koistinen ve Merburger tarafından bağıntısıyla açıklanmaktadır. Bağıntıya göre de dönüşüm sıcaklığı arttıkça kalıntı östenit miktarı da artmaktadır.
Kalıntı östenit miktarı su verme ortamı gibi soğutma spesifikasyonlarından da etkilenmektedir. Yağ ve tuz banyolarında kesikli su verme sonrası soğutma kalıntı östenit miktarını etkilemektedir.
Su verme ortamının sıcaklığı yanında su verme ortamının türü de kalıntı östenit miktarını etkilemektedir. Bu etki ortamın soğutma gücüyle de bağıntılıdır. Suyun soğutma gücünün aynı sıcaklıktaki yağa göre daha fazla olmasından dolayı kalıntı ostenit miktarı daha azdır.
Yüksek soğuma hızlarında parçanın göbek bölgesi ile yüzey arasındaki sıcaklık farklılığından dolayı oluşan çekme gerilmeleri malzemenin çekme dayanımını aşması durumlarda çatlama meydana gelmesi muhtemel olduğu için soğutma ortamının seçimi yalnızca kalıntı östenit miktarı açısından değil malzemede oluşabilecek distorsiyon ve çatlama riski açısından da göz önüne alınmaktadır.
Kalıntı Östenitin Mekanik Özelliklere Etkisi
Çelik yüzeyindeki düşük sertlikler kalıntı östenitin tipik karakteristiğidir. Temperleme veya diğer termo mekanik işlemlerle martensite veya beynite dönüşme eğilimlerinden dolayı boyutsal kararsızlığa da neden olurlar. Kalıntı östenitin bazı etkileri aşağıdaki gibi sıralanabilmektedir:
-Yüksek karbonlu çeliklerde sürtünme ve yorulma ömrünü artırır.
-Yine aynı çeliklerde hem eğme mukavemetini ve hem de erozyon dayanımını arttırır.
-Kalıntı gerilmelere neden olduğu için darbe mukavemetini düşürür.
-Çalışma koşullarında termo mekanik etkiden dolayı başka bir yapıya dönüşerek hacim değişimlerine neden olurlar.
Kalıntı Östenitin Giderilmesi
Sıfır Altı İşlemi
Alaşımlı takım çeliklerinde su verme sonrası yaklaşık % 0-30 arası kalıntı östenit kalabilmektedir. Kalıntı östenit ısı ve mekanik etkileşimlere karşı karasız olduğu için daha kararlı bir yapı olan beynit veya martensite dönüştürülmektedir.
% Martensit= 100-100exp-[1.10x10-2(Ms-Tq)]
Bağıntısına göre Tq (su verme ortamının sıcaklığı) arttırıldığında kalıntı östenit miktarı azalmaktadır. Dolayısıyla soğutma ortamı sıcaklığı düşürüldükçe kalıntı östenit miktarı da azalmaktadır. Ancak, her zaman az miktardaki östenit dönüşmeden kalabilmektedir.
Su verme sonrası oluşan yüksek çekme gerilmelerine ilaveten sıfır altı işlemle de yeni artık gerilmeler meydana gelebileceğinden çelikte mikro ve/veya ve makro çatlamalara yol açabilir. Bunun için sıfır altı işlem öncesi, 150-160°C sıcaklık aralığında 15-20 dakika bekletilerek su verme gerilmeleri azaltılmaktadır.
Su verme sonrası sıfır altı sıcaklıklara hızlı soğutmada martensite dönüşüm daha zor olduğundan soğutmanın yavaş yapılması yanında, artık gerilmelere neden olmaması için oda sıcaklığına da aynı derecede yavaş çıkarılmaktadır.
Kalıntı östenitin dönüşümü -70°C civarındaki bir ortamda belirli bir süre tutmayla dönüşümü sağlanabilmektedir. -100,-200 °C gibi düşük sıcaklıklarda uzun sürelerde tutmakla kalıntı östenitin tamamen dönüşmediği de çeşitli çalışmalarda görülmüştür.
Çeliklerde sıfır altı işlemi; genellikle sıvı azot, helyum, metanol, aseton ve katı karbondioksitle yapılmaktadır. Katı karbondioksitle -80°C civarında soğutma yapılırken sıvı azot içinde -196°C’ye kadar, helyum gazı içinde (sıvı halde) -268°C’ye kadar soğutma yapılabilmektedir.
Soğuk Deformasyon
Yüksek gerilmeler uygulandığında kalıntı östenit martensite dönüşmektedir. Özellikle östenitik Mn çeliklerinin üretiminde (Hadfield çelikleri) bu yöntem kullanılmaktadır. Soğuk deformasyon ve martensite dönüşümden dolayı oluşan gerilmeler temperleme ile giderilmektedir.
Temperleme
Yüksek C’lu ve alaşımlı çelikler, sertleştirme sonrası çok serttirler ve düşük tokluğa sahiptirler. Temperleme sonrası gerilmeler azalarak, sertlik düşerken çökelen karbürlerle de tokluk artmaktadır.