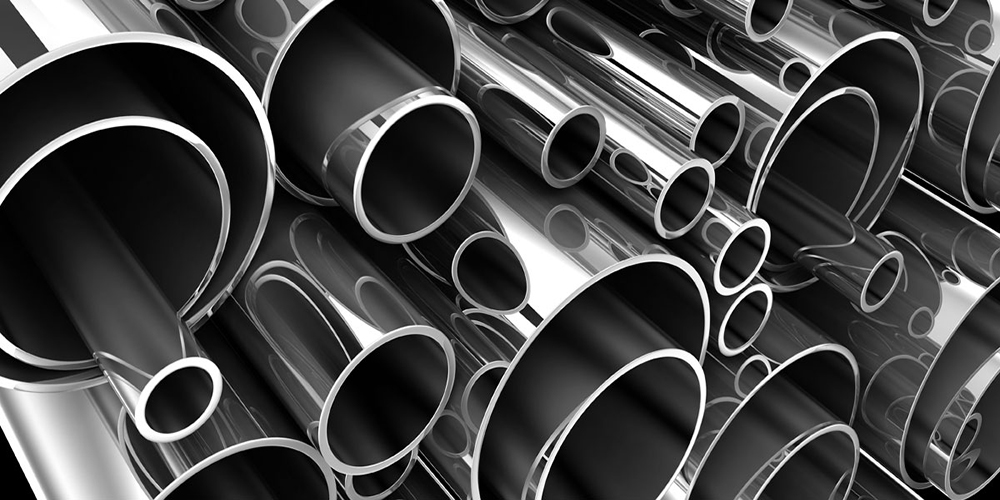
Kompozit malzemeler genel olarak devamlı bir faz (matris) içerisinde dağılmış bileşen (takviye elemanı) ile bu fazın birlikte oluşturduğu, bu yapıyı oluşturan bileşenlerin (matris ile takviye elemanı) özellikleri, geometrileri ve bu bileşenler arasındaki ara yüzeyin özelliklerinden tamamen farklı, kendine has özellikler barındıran malzeme sistemi olarak tanımlanırlar.
Kompozit malzemelerin tarihsel gelişimi incelendiğinde; insanlık tarihinde kullanımlarının çok eskilere dayandığı görülmektedir. Odun benzeri birçok doğal kompozit malzeme insanlar tarafından kullanılmıştır. Ayrıca, insanoğlu kompozit malzemelerin temel prensibi olan bir veya birden fazla malzemenin karıştırılması ve özelliklerin tek malzemede toplanması özelliğini keşfetmiş ve geliştirmiştir. Bu keşfe, çamur ve samanın karıştırılması ile elde edilen basit bir tuğla örnek verilebilir. 20. Yüzyılın son yarısı, kompozit malzemelerde dikkate değer gelişmelerin meydana gelmesi nedeniyle kompozit çağı olarak tanımlanmaktadır.
Kompozit malzemelerin bilim ve teknoloji alanındaki gelişmeler sonucunda önemi gittikçe artmaktadır. Artık tek yönlü malzemeler teknolojinin ihtiyaçlarını karşılamamaktadır. Seramik malzemelerin çoğu yüksek sertliğe ve yüksek sıcaklık dayanımına sahip olmakla birlikte, kırılgandır. Polimer malzemeler, düşük yoğunluk, nispeten düşük yumuşama ve bozunma sıcaklığı, büyük değişiklikler sergileyen dayanım ve süneklilik gibi özelliklere sahiptir. Örneklerde görüldüğü üzere, malzemeler istenen özellikleri tek başına karşılayamamaktadır. Bu nedenle kompozit malzemelerin üretim yöntemleri ve özelliklerinin geliştirilmesi konusunda yoğun çabalar sarf edilmektedir.
Kompozit malzeme genel olarak, matris ve takviye elemanı olarak adlandırılan iki bileşenden oluşmaktadır. Kompozit malzeme üretimi ile malzemelerin dayanım, korozyon ve aşınma direnci, yorulma ömrü, sıcaklığa bağlı davranışı, ısı ve ses yalıtımı, termal iletkenliği, ağırlık kazancı ve estetik özellikleri geliştirilebilir. Bu üstünlüklerin hepsini aynı anda gerçekleştirmek imkansızdır. Kullanım yerine ve özelliklerine bağlı olarak gereksinim duyulan özellikler artırılarak ve kontrol edilerek, isteğe bağlı malzemeler üretilebilmektedir. Kompozit malzemelerin eksiklikleri göz önüne alındığında, en önemli eksikliğin, üretim yöntemlerinin yerleşmemiş ve üretimin gerçekleştirilememiş olması nedeniyle oluşan yüksek maliyet olarak belirtilebilir.
Önerilen Makale: Çelik sac malzemeler ve uygulamaları hakkında detaylı bilgi almak için
çelik kalın levha sac sayfamızı ziyaret etmenizi tavsiye ederiz.
Kompozit Malzemelerin Sınıflandırılması
Kompozit malzemeler genel olarak matris malzemesi veya takviye elemanının tipine göre sınıflandırılmaktadır. Kullanılan matris malzemesine göre kompozit malzemeler; polimer matrisli kompozit malzemeler (PMK), seramik matrisli kompozit malzemeler (SMK) ve metal matrisli kompozit malzemeler (MMK) olmak üzere üçe ayrılmaktadır.
PMK malzemeler, hafiflik, mekanik dayanım gibi özellikleri yanında, insan dokuları ile uyum sağlayan ve sertlik derecesi ayarlanabilen yapay doku ve organ uygulamalarında; “optik elyaf” ve basınç ile elektrik üretebilen piezo elektrik özellikli ve istenildiği gibi işlenebilen özel sistemlerin yapımında da metal ve seramik malzemelerin yerlerine kullanılmaktadır. PMK malzemelerde matris malzemesi olarak kopma mukavemeti, yüksek aşınma direnci, kimyasal dirençlerinin yüksek olması sebebiyle sıklıkla termoset matrisler kullanılmaktadır. Termoplastik polimerlerin çeşitleri çok fazla olmasına rağmen üretimlerindeki zorluklar ve yüksek maliyeti nedeniyle matris olarak kullanılan termoplastikler sınırlıdır. PMK malzemelerde takviye elemanı olarak ise genellikle karbon, fiber ve aramid fiberler kullanılmaktadır.
Seramik matrisli kompozit malzemeler genellikle yüksek sıcaklıkta çalışması gereken parçalar için kullanılmaktadır. Sert ve kırılgan malzemeler olan seramik malzemeler, çok düşük kopma uzaması ile düşük tokluğa sahiptirler ve termal şoklara karşı dayanıksızdırlar. Bu nedenle takviye malzemesi ile takviye edilirler. SMK malzemelerde; matris malzemesi olarak Al2O3, SiC, Si3N4 ve B4C yaygın olarak kullanılmaktadır. Takviye elemanı olarak genellikle Al2O3 ve SiC gibi seramik malzemeler fiber formuna getirilerek kullanılmaktadır.
Kompozit malzemelerin içinde MMK malzemeler, yüksek sertlik, yüksek elastiklik modulü, yüksek aşınma ve kırılma direnci, düşük termal genleşme katsayısı ve yüksek mukavemeti gibi pek çok özeliklere sahip olduğundan dikkat çeken malzeme gruplarıdır.
Metal Matrisli Kompozit Malzemelerde Kullanılan Matris Elemanları ve Özellikleri
Kompozit malzeme üretiminde kullanılan matris malzemesi, takviye elemanlarının arasına emdirilmeli, takviye elemanını ıslatabilmeli, kimyasal veya belli şartlarda yapışma bağı oluşturmamalı, takviye elemanlarını bir arada tutmalı, mümkün olan düşük basınç ve sıcaklıkta hızlı şekilde katılaşma sağlayabilmelidir. Bir çok takviye elemanı gevrek ve kırılgandır. Matris bunların yüzeylerini dış ve çevresel etkilere karşı koruyup dirençlerini arttırmakta, kompozit üzerine gelen yükü takviye elemanına homojen olarak dağıtmakta ve kompozit içerisinde hata olasılığını azaltmaktadır.
Metal matrisli kompozitlerde matris malzemesi olarak genellikle Al ve alaşımları, Zn ve alaşımları, Cu ve Mg kullanılmaktadır.
Metal Matrisli Kompozit Malzemelerde Kullanılan Takviye Elemanları ve Özellikleri
Metal matrisli kompozit malzemelerin içerdikleri takviye elemanları, kimyasal içeriklerine göre karbürlü, oksitli, nitrürlü olmak üzere üç ana grupta; şekilsel özelliklerine göre ise partikül, visker, fiber ve metalik tel takviyesi olarak dört ana grupta toplanmaktadır.
Partikül takviyeli MMK malzemeler en düşük maliyete sahip olup yüksek hacimde takviye ilavesine imkan sağlamaktadır. Partikül takviyeli kompozitlerin üretimi genellikle 3-200 µm çapında partikül takviyesi (AL2O3, SiC, B4C) kullanılarak gerçekleştirilmektedir. Bu üretim için genellikle döküm ve toz metalurjisi yöntemi uygulanmakta ve partiküller bazı durumlarda kaplanmaktadır.
Visker takviyeler ise yüksek uzunluk/çap oranına sahip tek kristalli malzemelerdir. Visker takviyeli kompozit malzemeler, izotropik ve anizotropik özellikler göstermektedir.
Fiber takviyeler ise sürekli ve süreksiz olmak üzere iki gruba ayrılırlar. Sürekli fiber takviyeli MMK malzemeler yüksek sertlik ve mukavemete sahiptir ve devamlı fiber takviyesi olarak silikon karbür, grafit, alümina ve tungsten fiberler kullanılmaktadır. Kısa fiber ve partikül takviyeli MMK malzemeler ise, takviyesiz metal alaşımlarına göre daha yüksek sertlik, mukavemet ve boyutsal kararlılık göstermektedir. Fiberlerin malzemedeki ana görevi, malzemelerin yüke ve darbeye maruz kaldığı durumlarda matris üzerinde oluşan gerilimleri homojen olarak dağıtarak plastik deformasyonun oluşmasını engellemek ve kompozitlerin yapısal olarak kararlı kalmalarını sağlamaktır.
Metal Matrisli Kompozit Malzemelerin Üretim Yöntemleri
Metal matrisli kompozit malzemeler umut verici, yüksek mekanik ve termal özelliklere sahip olmalarına rağmen, sadece çok özel kullanım alanlarında uygulanmaktadır. Kompleks üretim gereksinimleri ve son ürünün yüksek maliyeti gibi eksiklikler metal matrisli kompozit malzemelerin yaygınlaşmasındaki en büyük engellerdir. Takviye elemanı imalatı ve kompozit üretim tekniklerindeki gelişmeler metal matrisli kompozit malzemelerin endüstriyel kullanımının artmasındaki en önemli sonuçlardır.
Metal matrisli kompozit malzemelerin mikroyapılarını ve mekanik özelliklerini optimize etme çabaları sonucunda her geçen yıl üretim teknolojileri evrim geçirmekte ve gelişmektedir. Üretim yöntemleri metalik matrisin üretim esnasındaki sıcaklığına göre sınıflandırılmaktadır. Dolayısıyla, metal matrisli kompozit malzemelerin üretim yöntemleri 5 gruba ayrılabilir;
- Sıvı faz üretim yöntemleri
- Katı faz üretim yöntemleri
- İki faz (sıvı-katı) üretim yöntemleri
- Biriktirme üretim yöntemleri
- In-situ üretim yöntemi
Sıvı Faz Üretim Yöntemleri
Metal matrisli kompozit malzemelerin sıvı faz yöntemi ile üretiminin günümüzde katı hal (özellikle toz metalurjisi) yönteminden daha ekonomik, avantajlı ve teknik öneme sahip olduğu bilinmektedir. Kompozit malzemelerin sıvı faz yöntemi ile üretimi genel olarak üçe ayrılmaktadır:
- Compo-casting veya karıştırma döküm
- İnfiltrasyon
- Sıkıştırma veya basınçlı döküm
Karıştırma Döküm
Karıştırma döküm yöntemi, karıştırılan ergimiş metal içerisine seramik partiküllerin katılması, partiküllerin homojen dağıtılması için yapılan partikül beslemenin tamamlanması sonrasında karışımın karıştırılması ve ergiyik karışımın dökülmesini içeren bir yöntemdir.
Karıştırma döküm yöntemi, özellikle endüstriyel açıdan gelecek vaad eden bir yöntem olarak kabul edilir. Basit, esnek ve yüksek miktarda üretime olanak sağlaması başlıca üstünlükleridir. Bunun yanında, geleneksel metal üretim yöntemi kullanıldığından, ürünün son maliyeti az olmaktadır. Bu sıvı metalurji tekniği, metal matrisli kompozit malzeme üretim yöntemleri arasında en ekonomik olanıdır ve çok büyük boyutlarda malzeme üretimine olanak sağlamaktadır.
Karıştırma döküm yöntemiyle hazırlanan metal matrisli kompozit malzemelerde, dikkat edilmesi gereken faktörler:
- Takviye elemanının homojen dağıtılmasının zorluğu
- Takviye ve matris malzemesi arasındaki ıslatılabilirlik
- Döküm metal matrisli kompozit malzemelerdeki gözeneklilik
- Takviye ve matris malzemesi arasındaki kimyasal reaksiyonlar olarak sıralanabilir.
Üretilen kompozit malzemenin ideal özellikleri kazanması için; takviye elemanının matris alaşımı içerisinde homojen dağılması ve aralarındaki ıslatılabilirliğin optimize edilmesi gereklidir.
İnfiltrasyon Yöntemi
nfiltrasyon yöntemi devamlı veya kısa fiber, whisker ya da partiküllerden üretilmiş gözenekli kompakt yapının içerisine sıvı metalin infiltre edilmesi olarak tanımlanabilir. Đnfiltrasyon yönteminde etkin olan parametreler; takviye elemanının başlangıçtaki bileşimi, morfolojisi, hacim oranı ve sıcaklığı, infiltre edilen metalin başlangıçtaki bileşimi ve sıcaklığı ile dışarıdan uygulanan kuvvetin büyüklüğüdür. Kullanılan infiltrasyon yöntemine göre, metal matrisli kompozit malzemelerde kullanılan takviye elemanının hacim oranı % 10-70 oranında değişmektedir. Bu teknikle üretilen malzemelerde bazı kademelerde gözeneklilik ve lokal takviye elemanının heterojen dağılımı benzeri istenmeyen durumlar oluşabilmektedir.
Bu yöntem genel olarak basınçlı ve basınçsız infiltrasyon olmak üzere ikiye ayrılır. Bazı kaynaklar vakumlu infiltrasyon yöntemini de üçüncü bir yöntem olarak tanımlamaktadır. Basınçsız infiltrasyon yönteminde ergimiş metal herhangi bir kuvvet uygulanmadan infiltre edilmektedir. Bu teknik uygulanırken, pahalı ekipmanların kullanılmaması ve takviye elemanının hacim oranının kolaylıkla kontrol edilmesi gibi özellikleri ekonomik olmasını sağlar. Basınçsız infiltrasyon yönteminde azot veya argon gibi özel atmosferik koşullar gereklidir.
Basınçlı infiltrasyon yönteminde ise, ergimiş metal ile önceden şekillendirilmiş fiber arasında oluşan ıslatma sorununun üstesinden gelmek için mekanik bir kuvvet uygulanır. Dıştan uygulanan basınç ile ilk amaçlanan kılcal (capillary) kuvvetleri bertaraf etmek olmasına rağmen, yüksek basınç üretim hızının artışı, kimyasal reaksiyonların kontrol edilmesi, matris mikroyapısının düzenlenmesi ve katılaşma büzülmesinin beslenmesi esnasında ürünün daha sağlam oluşu gibi faydalar sağlamaktadır. Presleme kuvveti hidrolik bir pres vasıtasıyla 10-100 MPa kuvvetle ergimiş metal üzerine uygulanarak ergimiş metalin önceden şekillendirilmiş fibere infiltre edilmesini sağlar. Kuvvetin gaz vasıtasıyla tatbik edildiği uygulamalarda bulunmaktadır. Bazı çalışmalarda takviye elemanının etrafında vakum oluşturmak suretiyle ergimiş metal önceden şekillendirilmiş fibere infiltre edilmektedir.
Basınçlı Döküm Yöntemi
Basınçlı döküm yöntemi, son şekline yakın döküm kompozit malzemeler üretmek amacıyla, hidrolik plakalar arasına yerleştirilmiş kapalı kalıplarla uygulanan presleme basıncı altında ergimiş metale şekil verme tekniğidir. Pres uygulanmadan önce sıvı metalle doldurulacak önceden şekillendirilmiş seramikler önceden ısıtılmış kalıba yerleştirilir. Uygulanan presleme basıncı 100-200 MPa aralığındadır. Eğer metal, partikül, kısa fiber veya metal sıcaklığı gerekli değerden düşük ise, döküm ürünlerinin kalitesi de düşük olabilir. Bu proses ilk olarak devamlı fiberlerin basınçlı dökümü için geliştirilmiştir, ancak günümüzde partikül ve kısa fiberlerin ergimiş metal ile karıştırılması ve üretimi işleminde de kullanılmaktadır.
Püskürterek Biriktirme Yöntemi
Püskürterek biriktirme yöntemi, ergimiş metal damlacıklarının takviye elemanı ile birlikte bir altlık üzerine püskürtülerek biriktirilmesi yöntemidir. Buna alternatif olarak, takviye elemanı altlık üzerinde bulunmakta ve ergimiş metal bu yüzey üzerine püskürtülmektedir. Ergimiş metalin püskürtülme metodu ve takviye elemanı ile ergimiş metalin karışma yöntemi, çeşitli püskürterek biriktirme yöntemleri arasındaki farklardır. Püskürterek biriktirme yönteminde en önemli parametreler; metal damlacıklarının akma hızı (velocity), boyut dağılımı ve başlangıç sıcaklığı, takviye elemanının besleme hızı ile altlık malzemesinin sıcaklığı ile pozisyonudur. Çoğu püskürterek biriktirme yönteminde, ergimiş metalden istenen düzeyde damlacıklar üretmek için (genellikle 300 µm çapına kadar) gazlar kullanılır. Partiküller damlacık akışının içine veya damlacık akışıyla kullanılan gaz arasına enjekte edilmektedir.
Püskürterek biriktirme yönteminin sağladığı üstünlükler arasında, matris mikroyapısında küçük tane boyutu ve düşük segregasyon sayılabilir. Bunun yanında, ergiyik metal ve takviye elemanı kısa bir süre temas ettiğinden, ara yüzey reaksiyonları minimize edilir. Bu yöntem esnasında kullanılan gazların maliyetinin yüksek olması, toplanması ve giderilmesi gereken atık toz miktarının çok olması diğer yöntemlere göre eksiklikleridir.
Katı Faz Üretim Yöntemleri
Katı faz üretim yöntemlerinde matris ile takviye elemanı arasındaki kimyasal etkileşim çok azdır. Katı faz yöntemlerinde matris ile takviye malzemesinin birbiriyle tam olarak karıştırılması gerekliliği vardır. Basit olarak ele alındığında, bu yöntemler matris tozunun takviye elemanı ile karıştırılması ve karışımın klasik toz metalurjisi yöntemleri ile (soğuk presleme ve sinterleme, sıcak presleme, sıcak izostatik presleme) numune eldesini amaçlar. Katı faz üretim yöntemleri arasında bulunan toz metalurjisi dışında sıklıkla kullanılan bir diğer yöntem de, difüzyonla bağlanma yöntemidir.
Toz Metalürjisi Yöntemi
Toz Metalurjisi yöntemi daha çok partikül takviyeli kompozit malzemelerin üretiminde kullanılmaktadır. Bunun iki nedeni vardır: matris malzemesinin visker ve fiber takviye malzemeleri ile karıştırılması zordur ve presleme esnasında fiber takviye malzemesi nedeniyle kırılmaların gerçekleşmektedir. Matris ve takviye elemanının karıştırılmasından sonra, gözenekli yapıyı ortadan kaldırmak ve mukavemet sağlamak için presleme ve sinterleme işlemi yapılır. Sinterleme işleminde seramik takviye elemanının yoğunlaşma hızı metal matristen düşüktür ve seramik partiküller bu sıcaklıkta sinterlenmez ve yoğunlaşmaya katkıda bulunmazlar. Bu nedenle partikül takviye oranı % 40’ın üzerinde olan MMK malzeme üretimi oldukça zordur.
Difüzyonla Bağlanma Yöntemi
Difüzyonla bağlanma aynı veya farklı metallerin birleştirilmesinde sıkça kullanılan katı faz üretim yöntemidir. Bu yöntemin genel üstünlükleri, çok çeşitli matris malzemelerin kullanımı, fiber yönlendirilmesi ve dağılımının kontrolüdür. Eksik yönleri, uzun üretim zamanı, yüksek üretim sıcaklığı ve presleme kuvveti ile karmaşık parça üretimindeki zorluklardır. Difüzyonla bağlanma işleminde mekanik özelliklerin kontrolünde fiber dağılımı en önemli etkendir. Fiberlerin birbirine yakın ve temas halinde oluşu, fiber kırılması ve/veya matris hasarı ile sonuçlanmakta, sonuç olarak çok büyük ve lokal stres birikimleri oluşmaktadır. Bu parçaya uygulanan herhangi bir basınç, parçada kırılmalara ve hatalara yol açar.
Difüzyonla bağlanma yönteminde, matris alaşımdan üretilmiş folyolar, matris tozu ile organik bağlayıcıdan oluşan toz karışımı ile fiberler önceden belirlenmiş şekilde dizilir. Dizilmiş tabakalar vakum ortamda, sıcak presleme işlemiyle şekillendirilir. Bu işlem dışında sıcak izostatik presleme işlemi kullanılmakta, kalıp içerisine konan parçaya her yönden eşit miktarda presleme kuvveti uygulanarak, karmaşık şekilli parçaların üretimine imkan sağlanmaktadır.
İki Faz (Sıvı – katı) Üretim Yöntemleri
İki faz teknikleri matris elemanının faz diyagramında hem katı hem sıvı bölgede bulunduğu matris ve takviye elemanının karıştırılması işlemidir. İki-faz teknikleri; ospray biriktirme, compodöküm, çok fazlı malzemelerin değişken biriktirilmesi teknikleridir.
Biriktirme Üretim Yöntemleri
Metal matrisli kompozit malzeme üretimi için biriktirme teknikleri, kompozit formunu oluşturmak amacıyla fiberlerin matris malzemesi ile kaplanması ve yapısal şeklini sağlamak için difüzyon bağlama işleminden oluşmaktadır. Bu yöntemler ile üretilen kompozit malzemeler döküm yöntemi ile üretilen kompozit malzemelerden daha homojendir. Biriktirme teknikleri; daldırma kaplama, elektrokaplama, sprey biriktirme, CVD (kimyasal buhar biriktirme), PVD ( fiziksel buhar biriktirme), sprey biçimlendirme teknikleri olmak üzere 6 ana gruptan oluşmaktadır.
In-situ Üretim Yöntemi
In-sıtu üretim yöntemleri, ergimiş metal ile kullanılan gaz arasındaki reaksiyonun kontrolü ve takviye elemanlarını oluşturmak amacıyla bileşenler arasında endotermik reaksiyonları oluşturma olmak üzere iki safhadan oluşur. Kontrollü reaksiyonlara örnek olarak laxide prosesi verilmektedir. Bu proseste Al ve Al2O3 karışımını elde etmek için ergimiş Al okside edilir.