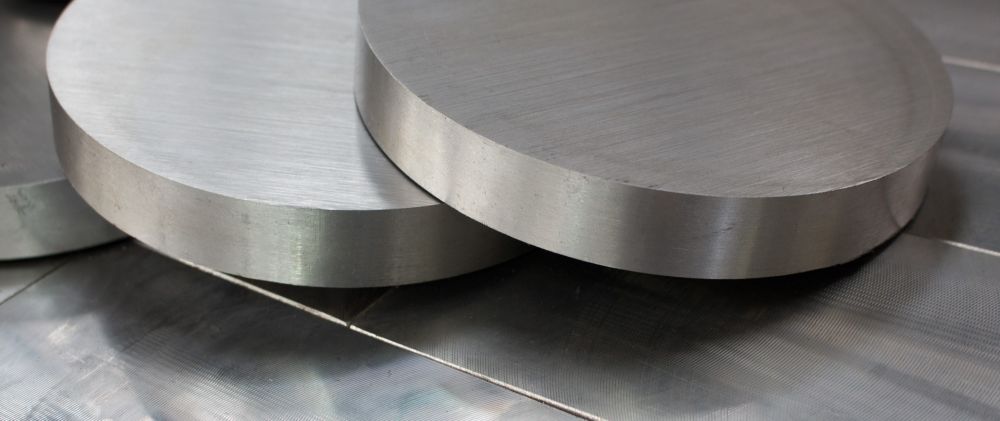
Nitemper işlemi gaz nitrürasyon işlemine çok benzer, ferritik-termomekanik işlem olup genellikle endogaz (endotermik gaz) + amonyak gazının 570-580 °C sıcaklıkları arasında yapılan bir yüzey sertleştirme işlemidir. Nitemper (düşük sıcaklıkta karbonitrürleme işlemini andıran). N
2+C verici bir ortamda çeliğin yüzeyine azot ve karbon emdirilmesi işlemidir. Nitemper işlem sıcaklığının düşük olması ve işlem süresinin kısa olması sonucu elde edilen sert nitrür tabaka derinliği 250-300 mikron arasındadır. Nitemper işlemi sonunda malzemede, çarpılma ve çatlama olasılıkları diğer yüzey sertleştirme işlemlerinden oldukça düşüktür.
Bu yöntem ilk defa 1980 yıllarında Almanya’da IPSEN firması tarafından geliştirilmiş ve 1985 yılından sonra günümüze kadar hızlı gelişme göstererek daha yaygın bir kullanım alanı bulmuştur. Nitemper ile sertleştirmede malzemenin yüzeyinde çok kuvvetli nitrürler meydana gelir. Bunlar yüksek sıcaklıkta difüzyon yolu ile azotun çelik içerisine girmesi ile oluşur. Çeliğin ostenitik yapıya geçmemesi için sıcaklığın daha yüksek olmasına izin verilmez çünkü ostenit çok fazla azot çözündürür.
Silindirik parçaların, iş millerinin ve büyük çapta parçaların nitrürlemesi için çok iyi sızdırmaz kapaklı yer ocakları - kuyu tipi fırınlar kullanılır. Küçük çapta nitrürleme işlemleri için ayrı bir nitrürleme rethortdu olan küçük fırınlar kullanılması idealdir. Alüminyum levha veya asbest flanj ile rethort kapağı arasında bir conta -sızdırmaz malzemesi olarak kullanılır. Nitemper işlemi yapılacak çeliklerin yüzeyinin karbonunun yanmaması için özel önem gösterilmelidir. Nitemperleme esnasında reaksiyon sırasında serbest kalan " N" ve "H" atomları, malzemenin karbonunun yanmasına yol açabilir. Nitemper işleminde, kullanılan gazların ( NH
3 ve N
2 ) ile reaksiyona girmeyecek "Cr-Ni " Sarj sepetler, 310 kaliteden mamul Cr-Ni malzemelerden yapılırlar. Krom- Nikel, Inconel, aşınma ve oksidasyona dayanıklı alaşımlar içeren benzeri malzemelerin kullanılması idealdir.
Nitemper işlemi ile çelik malzemelere kazandırılan özellikler ile malzemelerde işlemler sonrası geliştirilen özeliklerini şu şekilde sıralayabiliriz;
1- Yüksek yüzey sertliğinin oluşması
2- Sürtünmelere karşı aşınma mukavemetinde artış göstermesi
3- Yüksek çalışma sıcaklıklarında sertliğini muhafaza edebilmesi
4- Yüksek yorulma mukavemeti özelliği göstermesi
5- Yüksek boyutsal kararlılık
6- Çalışma esnasında parça yüzeyinde kaygan yüzey oluşturması
Malzemelerin, kimyasal bileşimleri değiştirilerek ince kabuk bir tabakasında nitemper yöntemleri ile malzemelerin dış yüzey kısımlarının sert olan bir yapı oluşturulması amaçlanır. Nitemper işlemleri talaşlı imalatı tamamlanmış ve son taşlama işlemleri yapılmış nitemper sonrası her hangi bir nedenle talaşlı imalatı yapılmayacak parçalara uygulanır. Nitemper sonrası parça yüzeyinde aşırı sertlik : ( 820 -1100 Hv sert bir tabaka ve 0.2-0.5 mm nitemper derinliğini) olduğu için bu aşırı sert tabakadan talaş kaldırma işçiliği istenilmez veya çok zor talaş kaldırılabilinir.
Nitemper işlemi yapılmış parçalarda sadece kısmi taşlama işlemlerine müsaade edilebilir. Nitemper çok hassas sıcaklık kontrollü de çalışan bir elektrik ısıtmalı fırınında yapılır. Nitemper işlemleri düşük sıcaklıklarda : 550 – 575 °C’lerde uygulanan bir yüzey sertleştirme işlemi olduğu için malzemelerde fazla çarpılma ve iç gerilmeler-gerginlikler görülmez. Nitemper sonrası malzemenin ölçüsünde küçük ölçüsel değişiklikler olur. Ölçü değişikliği (büyüme) nitemper tabaka kalınlığının % 2 si kadardır. Nitemper işlemlerinde istenilen değerlerin elde edilememesi durumunda (başarı sağlanamaz ise) işlemin yeniden tekrarlanma imkanı yoktur.
Önerilen Makale: Sementasyon çeliği malzemeler ve uygulamaları hakkında detaylı bilgi almak için
sementasyon çelikleri nedir sayfamızı ziyaret etmenizi tavsiye ederiz.
Nitemper İşlem Prosesleri
Nitemper işlemi sonrası istenilen değerlerin elde edilmesi için aşağıdaki proses ( operasyon ) sırası takip edilerek, işlemin yapılmasında yarar vardır.
1- Nitemper işlemi uygulanacak parçaların malzeme özellikleri
2- Talaşlı imalat öncesi sert olan ve işlenmesinde zorluklar yaşanan malzemelere yumuşatma tavlaması yapılması Yumuşatma tavlaması sonucunda malzemenin işleme sertliği 22-26 HRC olmasında yarar vardır.
3- Talaşlı imalat esnasında ( işleme esnasında malzeme içerisinde oluşan ) malzeme içerisinde oluşan iç gerilmelerin, gerilme giderme tavlası ile alınması
4- Talaşlı imalatın taş paylı ( 0.2-0.6 mm paylı ) olarak yapılması
5- Malzemenin çekirdeğinin maksimum sertlik alacak şekilde sertleştirilmesi
6- Malzemenin tok yapıda olması ve iç yapısının: 28-32 HRC olacak şekilde temperlenmesi
7- Sertleştinne öncesi bırakılan taş paylarının olabilecek çarpılmaların ve taşlama operasyonu ile alınması için son taşlama işlemlerinin yapılması
8- Parça yüzeyinde oluşan pasların alınması
9- Parça yüzeyinde çalışma ortamından dolayı oluşan yağların alınması (yıkanması)
10- Nitemper işlemi öncesi 1. ön ısıtma işleminin yapılması
11- Gerekirse 2. ön ısıtma işleminin yapılması
12- Nitemperleme işlemin yapılması için parçaların fırın içerisine konularak işleme başlanılması
13- Nitemper işlem sonrası kontrollerin yapılması
14- Mekanik test işlemlerinin yapılması
15- Metalografik numunelerin incelenmesi
Nitemper İşlemi İçin Ön ısıtma işlemi
Yağdan arındırılmış ve paslı olan bölgeleri temizlenmiş nitemper işlemi sonrası sertlik istenmeyen bölgeleri koruma macunu surfatec ile korunarak kapatılmış parçalar 200-250°C deki sıcaklıkta ısınmış fan sirkülasyonlu fırının kapağı açılarak sarj sepetine yerleştirilen malzemeler fırın içerisine 1. ön ısıtma işleminin yapılması için yerleştirilir ve fırın kapağı kapatılır. Fırına start verilmeden yaklaşık 10-15 dakika bekletilir. Fırına tekrar start verilerek, saatte 35-50 °C/h ısıtma hızı malzemenin ısıtılmasına başlanılır. Fırın sıcaklığı programlanan 250 °C’ye kadar ulaştıktan sonra parça kalınlığı linç = 1 saatlik programlanan sıcaklıkta bekletilerek malzemenin iç noktalarına kadar ısının ulaşması sağlanır. Sarj sepeti içerisindeki malzemeler fırın içerisinden alınarak, 550-600 °C ısıtılmış olan fırın içerisine 2. ön ısıtma işleminin yapılması için yerleştirilir.
Ön ısıtma işlemi malzemenin çalışma şartlarında istenilen özellikler dikkate alınarak koruyucu ortamda endoğaz -azot gazı altında da 2. ön ısıtma işlemi yapılabilir. Malzemelerin çalışma yerlerindeki durumu fazla özellik arz etmiyorsa ön ısıtma işlemi sızdırmaz kapaklı fırınlarla da yapılabilir.
Sarj sepeti içerisinde yerleşik olan malzemelere daha önce 1. ön ısıtma işlemi yapılmıştı. Malzemeler 550-600 °C ye kadar ısıtılmış fan sirkülasyonlu 2. fırınının kapağı açılarak içerisine yerleştirilir. Fırın kapağı parçalar yerleştirildikten sonra kapatılır. Fırına yaklaşık 15-20 dakika start verilmez bu esnada fırın sıcaklığını malzemelerin bünyesine nufüziyet etmesi sağlanmış olunur. Fırın sıcaklığı 600 °C’ye programlanır.
Nitemper işlemi sonrasında malzemede her hangi bir talaş kaldırma işlemi (taşlama) yapılmayacak ise, 2. ön ısıtma işlemi yapılan parçaların her hangi bir tufal, kav olayının oluşmaması için mutlaka atmosfer gazı altında ön ısıtma işlemi yapılmalıdır. Atmosfer gazı olarak, Endogaz, Egzotermik gaz, veya Azot gazı kullanılabilir. Fırın içerisine verilen koruyucu gazın miktarı. 3-5 m3/h olmalıdır.
Malzemelerin ısınma hızı 45-60 °C/h olacak şekilde fırın sıcaklığı programlanır ve fırına start verilerek ısıtma işlemine başlanılır. Fırın sıcaklığı 600 °C’ye ulaşınca parça kalınlığı 1 inch= 1 saat programlanan sıcaklıkta bekletilerek malzemelerin iç noktasına kadar sıcaklığın ulaşması sağlanır. 2. ön ısıtma işlemi tamamlanan malzemeler nitrürasyon işlemi yapılması için fırından çıkartılarak fazla ısı kaybı olmadan nitrürasyon fırını içerisine yerleştirilir.
Nitemperleme İşleminin Yapılması
Talaşlı imalatı tamamlanmış, çok az bir taşlama (0.020-0.050 mm taş paylı ) işlemi kalan parçaların yağ artıkları ve pası alındıktan sonra sarj sepetine koruma bölgelerine macun sürülerek ön ısıtma işlemleri yapılır. Ön ısıtma işlemi tamamlanan sarj sepetleri içerisindeki parçalar, nitemper işleminin yapılması için 570 ± 5°C ısınmış olarak hazır bekleyen fırın kapağı açılarak fırın içerisine yerleştirilir.
Fırın ölçüsü: 620x820x650 mm ölçülerinde sarj sepeti içerisinde yerleştirilen ve 350 Kg ağırlığında olan parçaların nitemper işlemleri yapılır.
Fırın içerisi yüksek ısıya ve amonyak-azot gazlarının aşınmasına dayanıklı ısı absorbu olmayan özel preslenmiş pamuk türü fıberfraxs diye tanımlan olan malzemeler ile kaplanmıştır. Fırın içerisinde kullanılan metalik malzemelerin tamamı "Cr-Ni" alaşımlı çelik malzemelerden oluşmuştur. Ayrıca ısının düzenli yayınması ve sıcak hava-gaz karışımı sürekli olarak fan ile türbülans hareketi yapılarak karışım sağlanabilecek şekilde dizayn edilmiştir. Parçaların nitemper işlemi yapılması için fırın kapağı pönomatik olarak açılır. Kapının açılması ile birlikte pilot alevleri devreye girerek fırın içerisine havanın girişi engellenerek parçalar şarj sepeti ile birlikte fırın içerisine bant ile birlikte sürülerek kapılar kapatılır. Kapı açılması ile birlikte bir miktar sıcaklık düşmesi gözlenir.
Fırına start verilir. Fırın 45-60 °C/h’lik ısıtma hızı ile 575°C ye ayarlanır, fırın süratle programlanan 575°C sıcaklığa ulaşınca parçalanma başlamış olur. Fırın içerisine verilen % 45-50 oranında: 2.45 - 2.50 m3/h endogaz ile % 55-50 oranında : 2.55-2.5 m3/h NH3 gazı, karışık gaz olarak aynı borudan pilot alevi ile tutuşturularak fırın ortamına verilir. Fırın iç basıncı 12-15 milibar arasında baca çıkış vanası yardımıyla sabitlenir. Fırın içerisine verilen giriş gazı toplamı oranında, pilot alevi ile tutuşturularak ve pasivize edilerek fonksiyonu tamamlanmış gazlar çıkış bacası vasıtası ile fırın ortamından dışarı atılır.
20-22 mikron kalınlığında beyaz tabaka, 280-300 mikron etkili nitemper derinliği (Hv5-540) ve 810-960 Hv sertliği için 7.5 saatlik işlem süresi yeterli olmaktadır. 7.5 saat süre ile işleme devam edilir ve işlem sonrası fırın sıcaklığı 400 °C’ye programlanır. Fırın sıcaklığı 400 °C’ye kadar düşüş esnasında fırın içerisine verilen gazların miktarı değiştirilmez aynen gaz verilmeye devam edilir.
Fırın sıcaklığı 65-80 °C/h soğutma düşüş hızı ile 400°C ye (1.5-2 saat ) ulaşınca fırın kapağı pönamatik olarak açılır. Kapının açılması ile birlikte, alev perdesi kapı ağızı boşluğunu kapatarak ve fırın içerisinde bulunan gazların hava ile reaksiyonuna girmemesi ve patlamaması için dışarı gaz atılırken yakılarak atılır. 400°C ye kadar soğutulmuş ve nitemper işlemi yapılmış parçalar sarj sepeti ile fırın dışarısına çıkartılarak ortam sıcaklığında malzemelerin soğuması beklenir. Soğuyan malzemeler şarj sepeti içerisinden çıkartılarak mekanik test ve metalografik- numune nitemper yapılmış parçalar inceleme yapılmak üzere alınır.
Nitemper İşlemi Sonrası Sertleştirme Derinliğinin Tespiti
Çeliğe yüzey sertleştirme işlemi uygulandığında çeliğin yüzey sertliği ve aşınma direnci esneklik ve burma kuvvetlerine karşı dayana bilme kabiliyeti ile yorulma mukavemetinde artış gösterir. Bu özellikler için yüzey sertleştirme derinliği önemli bir etkendir. Eğer çeliğin yüzeyi düşük yüklerde yapışıcı aşındırmaya maruz kalırsa mm in onda biri değerindeki sertleştirme derinliği genellikle yeterlidir. Yük miktarı arttıkça sertleştirme derinliği de artırılmalıdır.
Sertleştirme derinliğinin seçimi çoğu kez bir deneyim meselesi olup teorik düşüncelerin bir sonucu olarak nadiren gerçekleşir. Gerçek pratikte yükün iki kütle yüzeyi arasındaki ara yüzeyin kesitinde ender olarak muntazam dağılım göstermesi yapılan hesapların iyice karışık hale sokar. Yüzey sertleştirme işlemi uygulanan dişliler için tasarım yükü dişli modülü ile orantılıdır. Yüzey sertleştirme derinliği genellikle modülün: 0.15-0.18 katı olarak alınır. 20 mm den daha büyük sertleştirme derinliği dişlilerde çok nadir karşılaşılan bir durumdur.