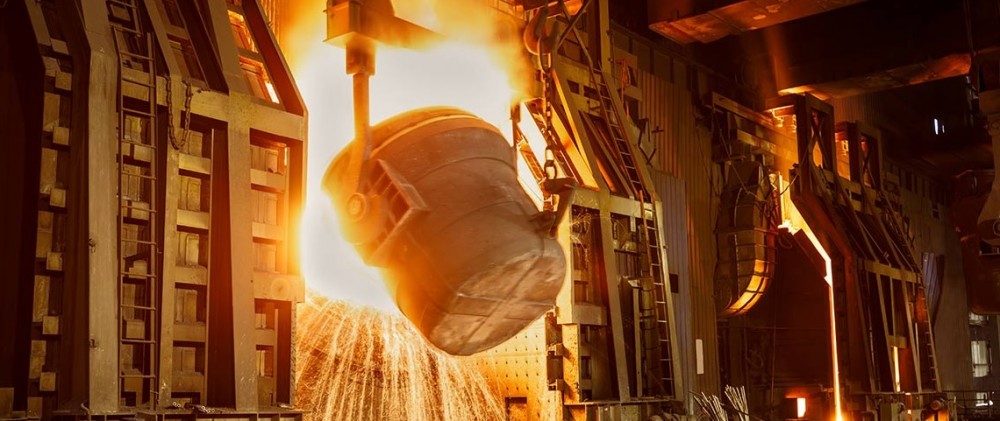
Sıvı çelik, üretimi sırasında temasta olduğu oksijen ve azot gazlarını yüksek sıcaklık etkisiyle büyük oranda çözebilir. Katılaşmadan sonra kalan oksijen miktarının %0,03'ten fazla olması çeliği yaşlanmaya karşı duyarlı,%0,07'nin üzerinde olması ise kızıl sıcaklıkta kırılgan yapar.
Metal banyosunda FeO halinde bulunan oksijen ile karbon arasında
FeO + C ⇒ CO + Fe
reaksiyonu oluşur. Sonuçta elde edilen çeliğin karbon derişikliği azaldıkça, çelikte kalan çözünmüş oksijen oranı artar. Bu ilişki yaklaşık olarak
C x O = sabit
bağıntısı ile verilebilir.
Buna göre özellikle C < %0,1 olan çeliklerde oksitleme işleminden sonra oksijen giderilmesi zorunludur. Sıvı çelikten oksijenin uzaklaştırılması, yani artık demir oksidin indirgenmesi, oksit giderme olarak adlandırılır. Bu amaçla, oksijene karşı kimyasal ilgileri (afiniteleri) demirden daha fazla olan aşağıdaki elementlerden yararlanılabilinir:
Mn - V - C - Si - Ti - B - Zr- Al (afinite soldan sağa artıyor)
İndirgeme gücü zayıf olan ve karbonun demir oksit ile CO oluşturmasını önleyemeyen mangan, öncelikle
FeS + Mn ⇒ MnS + Fe
reaksiyonunu gerçekleştirmek, yani istenmeyen demir sülfürü zararsız mangan sülfüre dönüştürmek için konverterde veya döküm potasında çeliğe (daha önce karıştırıcıda pik demire) ferromangan halinde katılır. Silisyum ve alüminyum etkin oksit gidericiler olup, alüminyum oksijenin yanında tehlikeli olan azotu da nitrür( A1N) olarak bağlar. Alüminyumunkine benzer etki gösteren Ti ve B ise, ayrıca karbona olan ilgileri dolayısıyla karbonitrür meydana getirirler: Ti (CN), B (CN).
İngot Dökümü ve Sürekli Döküm
Sıvı metalin ingot kalıplarına (dökme demir kokillere) doldurulup katılaşmaya bırakılmasına ingot dökümü, su ile soğutulan bakır kokile bir uçtan akıtılırken öteki uçtan katılaşmış durumda dışarı çekilmesine sürekli döküm denir.
Başlangıçta demir dışı metallere uygulanan sürekli döküm yöntemi son yıllarda
çelik üretiminde de teknik ve ekonomik açıdan büyük önem kazanmıştır. Yöntemin üstünlükleri şöyle sıralanabilir:
Soğuma hızı yüksek olduğundan homojen ve ince taneli çelik elde edilir.
Kokil amaçlanan yarı mamule en uygun şekilde tasarlanabilir.
Üretim hattında te, çukurlarına ve blok haddesine gerek kalmaz.
Verim ingot dökümüne göre daha yüksektir; çünkü her ingotta kafa lunkerinin kesilmesinden ileri gelen kayıp sürekli dökümün sonunda sadece bir kez ortaya çıkar.
Öte yandan CO kabarcıklarının yarattığı olumsuz etki nedeniyle yalnız durgun çelikler sürekli dökümle üretilebilirler.
Vakumda gaz alma yüksek kaliteli çeliklerin elde edilmesinde giderek yaygınlaşmaktadır. Böyle bir işlem görerek döküldükleri için gaz ve kalıntı miktarları çok düşük olan (temiz) çelikler, başta tokluk ve dinamik zorlamalara karşı dayanım olmak üzere, üstün mekanik özelliklere sahiptirler.
Çeliğin Katılaşması
Çelikler oksit gidermenin etkinlik derecesiyle ilişkili olarak, kokilde katılaşma sırasındaki davranışlarına göre kaynar, durgun ve özel durgun diye sınıflandırılırlar.
Kaynar Çelik (İşareti: U)
Çeliğe sadece mangan verilir; kükürt ve oksijen MnS ve MnO olarak bağlanır. Katılaşmanın kokil duvarında başlamasıyla, önce karbonca fakir katı çözelti kristallerinin ayrışmasından ötürü, kalan eriyik karbon ve düşük sıcaklıkta eriyen diğer elementler bakımından zenginleşir. Böylece eriyikte karbon ile az da olsa hR1/1 bulunan FeO arasındaki denge bozulur. Meydana gelen ve N2,H2 gibi diğer çözünmüş gazları da sürükleyen CO kabarcıklarının neden olduğu "kaynama" sıvı/katı bileşim farklılığının giderilmesini engeller.
Sonuçta özellikle fosfor, kükürt gibi yavaş yayınan elementler ile karbon ve manganın homojen olmayan bir dağılımı ortaya çıkar (makrosegrecıasyon). Çelik ingotun ortasında fosfor ve kükürt miktarları ortalama derişikliğin 3 ila 4 katı olabilir. İngot kenarında meydana gelen gözeneksiz, karbon ve katışkıları çok az olan demir tabakası kaynar çelikler için karakteristiktir.
Durgun çelik (İşareti: R)
Silisyum katılması (ve kükürt giderme için ayrıca mangan), oksijeninçelikte Fe0 yerine Si02 olarak bulunmasını sağlar:
2 FeO + Si + SiO2 + 2Fe
Silisyumun oksijene afinitesi karbonunkinden fazla olduğun-dan karbon ile indirgenme yani CO oluşumu söz konusu değildir.
Böylece CO gazının çıkışından ileri gelen banyo hareketi görülmez. Çelik "durgun" olarak katılaşır ve makrosegregasyon kaynar çeliktekine göre yok denecek kadar azdır. Ancak gözeneksiz katılaşma, büyük ve çoğunlukla içeri doğru uzayan bir lunker yaratır. Katılaşma sırasında ingot kafasının ısıtılması, çeliğin bu bölgede daha uzun süre sıvı durumda kalarak söz konusu boşluğu doldurmasına yardım eder. Kafa lunkeri blok haddesinde kesilir. Dolayısıyla durgunlaştırılmış çelikte üretim verimi durgunlaştırılmamıştan %15-20 daha düşük olur. Lunkeri tümüyle uzaklaştırılamamış bir ingotun haddelenmesi, kesinlikle istenmeyen katmer oluşumuna yol açar.
SİO2’in bir bölümü yükselerek cürufa geçer; ancak önemli miktarı eriyikte asılı kalır. Katışkılar ve oksit giderme işleminin ürünleri (SiO2) ingot içinde oldukça homojen bir dağılım gösterirler. Kaynar çelik ingotlarındaki gibi bir demir tabakası bulunmadığından, durgun çeliklerden haddelenen yarı mamullerin yüzey kalitesi iyi değildir. Bu nedenle derin çekme saçları çoğunlukla kaynar veya. ekil değiştirme kabiliyetine büyük önem veriliyorsa düşük karbonlu özel durgun çeliklerden üretilir.
Aşağıdaki hallerde çelik durgun olarak dökülmek zorundadır:
Dökme Çelikler: Dökülen parçalara daha sonra haddeleme veya dövme gibi şekil verme işlemleri uygulanmayacağından gözeneksiz yapı istenir.
Sert Çelikler: %0,25'den fazla C içeren çeliklerde oksijen miktarı düşük olduğundan, katılaşma sırasında çıkan CO gazı ingotu terkedemeyecek kadar azdır. Rasgele dağılan gözenekler kenar tabakada da yüzeye çok yakın şekilde yer alır. Kalite açısından sakınca yaratan bu durumu önlemek için eriyik durgunlaştırılır.
Alaşımlı Çelikler: Alaşım elementlerinin homojen dağılmasına sağlamak üzere daima durgun olarak dökülmelidirler.
Özel Durgun Çelik (İşareti: RR)
Sıvı çeliğe mangan ve silisyuma ek olarak alüminyum katılıp kalan oksijen Al203’e, azot ise A1N'e dönüştürülür. Böylece oksijenin yanında, şekil değiştirme yaşlanmasına neden olan azotun gevrekleştirici etkisi de giderilmiş olur. Ayrıca A1N parçacıklarının katılaşmada çekirdek rolünü oynaması içyapının ince taneli olmasını sağlar. Sonuçta dayanım ve tokluk büyüklükleri olumlu yönde değişir. Akma sınırı ve çentik vurma tokluğu artar, geçiş sıcaklığı düşer.