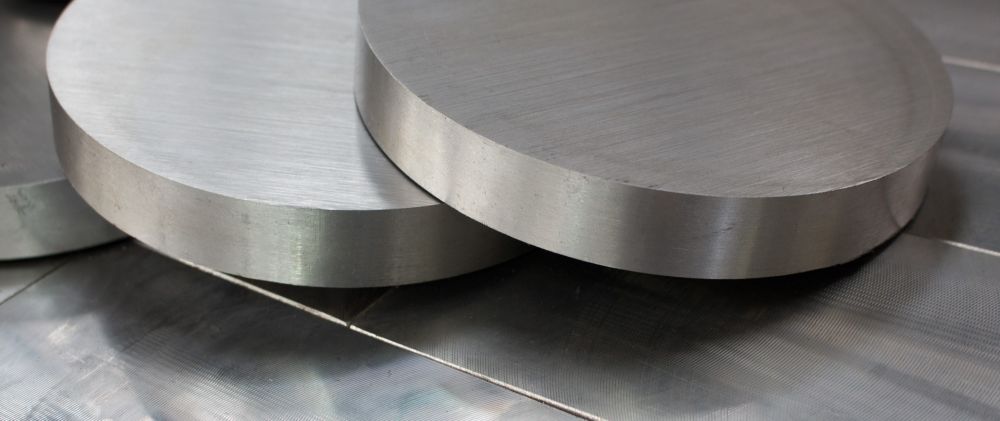
Sinterleme, birbirine temas eden parçacıkların yüksek sıcaklıklarda birbirine bağlanmasını sağlar. Bu bağlanma, ergime sıcaklığının altında katı halde atom hareketleriyle oluşabilir. Fakat, pek çok durumda, sıvı faz oluşumu ile birlikte gerçekleşir. Mikroyapı ölçeğinde, bağlanma temas eden parçacıklar arasında boyunlaşma ile kendini gösterir.
Sinterleme, yüksek sıcaklıkta atomların yayınımı ve küçük parçacıkların yüzey enerjisinin azalmasıyla gerçekleşir. Toz üretimi, malzemeye enerji vererek yüzey alanı veya yüzey enerjisi yaratma işlemidir. Sinterleme ile bu yüzey enerjisi giderilir. Birim hacimdeki yüzey enerjisi parçacık boyutu ile ters orantılıdır. Bu nedenle, daha yüksek özgül yüzey alanına sahip olan küçük boyuttaki parçacıklar daha yüksek enerjiye sahiptir ve daha hızlı sinterlenir. Fakat yüzey enerjisinin tamamı sinterlemeye harcanmaz. Kristal yapılı katılarda hemen hemen bütün parçacık temas nokta sınırlarının enerjisine sahip olan tane sınırı oluşturur. Böylece boyun büyümesi yüzey enerjisini azaltırken, tane sınırı enerjisini arttırır. Doğal olarak, bu sadece yüzey enerjisindeki azalmasının tane sınırı enerjisindeki artıştan yüksek olması durumunda meydana gelir.
Sinterleme esas olarak itici güçler, mekanizmalar ve aşamalar açısından incelenir:
• Sinterlemenin itici güçleri bağlanmaya neden olan mikroskobik eğrilikleri tanımlar.
• Sinterleme mekanizmaları itici güçlere tepki olarak oluşan atom hareketlerinin yolunu tanımlar.
• Sinterleme aşamaları atom hareketleri sonucu oluşan geometrik gelişimini tanımlar. Bu aşamalar da diğer taraftan itici güçleri değiştirir.
İtici güçler veya sinterleme gerilmeleri mikroyapıdaki eğriliklerden kaynaklanır. Sinterleme mekanizmaları genellikle yüzey, tane sınırı veya kristal kafesinde oluşan yayınım işlemleridir. Sinterleme aşamaları etkin itici gücün ve kinetiğin açıklanmasına yardımcı olur ve işlemin matematik modellemesinde kullanılır.
Sinterlemedeki geometrik değişimler atomların hareketini sağlayan ısıtmadan kaynaklanır. Atomların hareket edebilmesi için gerekli olan enerjiye “aktivasyon enerjisi” denir.
Sinterleme işlemi en kaba hatlarıyla “Katı hal sinterlemesi” (KHS), “Sıvı faz sinterlemesi” (SFS) şeklinde sınıflandırılabilir. Bu sinterleme mekanizmalarının hepsinde metal taşınım mekanizmaları farklılık gösterir. Tek fazlı metal tozlarından oluşan kompaktlar sinterlendiğinde olası metal taşınım mekanizmaları tanımlanabilir. Fakat temelde iki farklı süreçten oluşan sıvı faz sinterlemesinde bu metal taşınım mekanizmalarını tanımlamak daha zordur. Sıvı faz sinterlemesinde iki farklı süreçten birinde, kompaktlar sinterleme sıcaklığındayken bütün işlem süresince sıvı faz vardır. Bu sürece örnek olarak %10 veya daha az miktarda nikel ve bakır veya nikel ve demir içeren volfram ağır alaşımı ve sementit karbürlerin sinterlenmesi verilebilir.
Kompaktlar, alaşım sisteminin sıvılaşma ve katılaşma eğrileri arasında sinterlenir ve sinterleme çevriminin tamamında heterojen bir yapıya sahiptirler. Bu mekanizma “Sürekli sıvı faz sinterlemesidir”. Diğer sıvı faz sinterleme mekanizması “Geçici sıvı faz sinterlemesi “ mekanizmasıdır ve bu mekanizmada sinterleme sıcaklığında sıvı fazın varlığı sinterleme süresince değil, sadece belirli bir süre için söz konusudur. Bazı metal tozlarına küçük miktarlardaki alaşımlandırıcı elementlerin ilavesi sinterleme hızında 100 katına kadar ulaşan bir artışa neden olur. Bu işlem “aktivasyonlu sinterleme” veya aktive edilmiş sinterleme” olarak adlandırılır.
Önerilen Makale: Sementasyon çeliği malzemeler ve uygulamaları hakkında detaylı bilgi almak için
sementasyon çeliği nedir sayfamızı ziyaret etmenizi tavsiye ederiz.
Katıhal Sinterleme
Tek fazlı (saf metal) partiküllerden oluşan kompaktları sinterleyebilmek için sinterleme sıcaklığı olarak malzemenin ergime sıcaklığının yaklaşık olarak %80 civarındaki sıcaklıklar seçilir. Sinterleme sırasında mikroyapıdaki değişimler, boyutsal değişimlerle beraber parçanın fiziksel ve mekaniksel özelliklerinde değişmeler meydana getirir. Mikroyapıdaki bu değişimler önceden şekillenmiş ve mukavemetleri düşük olan ham parçalara mukavemet kazandırır.
Sinterlemenin ilk aşamasında toz partikülleri arasındaki temas alanı artar, yapıdaki mevcut gözenekler küreselleşir, partiküllerin merkezleri arasındaki temas alanı artar, yapıdaki mevcut gözenekler küreselleşir, partiküllerin merkezleri arasındaki mesafe azalır ve bunun sonucu olarak parçada çekilme meydana gelerek yoğunluk artar.
Daha sonraki aşamada partiküllerin birbirleriyle birleşmesi son bulur ve sonuçta izole gözenekler oluşur. Yapıda malzeme taşınımı ile gözeneklerin boyutları küçülür ve tane büyümesi meydana gelir.
Bazı sinterleme oluşumları sırasında parçalarda genleşme görülebilir. Bu genleşme şekillendirme sırasında gözeneklerde kalan gazların sinterleme sıcaklığında basınç artışı sonucu görülür. Yapıdaki gazın genleşmeye neden olabilmesi için sinterleme sırasında parça içerisinde yayınmaması veya metal ile reaksiyona girmemesi gerekir (örneğin oksijen metallerle oksit oluşturabilir). Preslemenin atmosferik koşullar altında yapılması halinde gözeneklerde sıkışıp kalan havadaki oksijen, hidrojen gazı altında yapılan sinterleme sırasında su buharı oluşumuna neden olabilir. Gözenek boyutu küçük olduğundan hacimsel bir genleşme meydana gelmez.
Katıhal Sinterleme Aşamaları
Sinterlemenin ilk aşaması, her parçacık üzerinde birkaç noktada boyun büyümesi ile tanımlanır. Fakat boyunlar birbirinden bağımsız olarak büyür. Sıkıştırma olmadan parçacıklarda temas küçük noktalar ile başlar. Başlangıçta gözenekler düzensiz ve köşeli şekildedir. Boyun zamanla dışbükey bölgedeki atomlar tarafından doldurulan bir içbükeyliği temsil eder. Boyun büyüdükçe kavis azalır ve işlem yavaşlar. Sinterlemenin ara aşamasında gözenekler yuvarlaklaşır, fakat gözenekler etrafındaki kavis kütle transferi için itici güç oluşturmaya devam ederek içbükey bölgeleri doldurur. Sinterlemenin ara aşamasında, boyunlar birbiri ile etkileşecek ve örtüşecek ölçüde büyümüştür. Her ne kadar gözenekler yuvarlaklaşıp düzgün hale gelse de hala dışa açıktırlar. Diğer bir ifadeyle akışkanlar ham parça içine girip çıkabilir. Sinterlemenin ilerlemesiyle taneler büyür ve gözenekler küçülür. Sinterlemenin son aşamasında gözenekler kapalı ve küreseldir. Tam yoğunluğa yaklaşılırken tane sınırı hareketini zorlaştıran gözenek sayısı azaldığından tane büyümesi hızlanır. Gözenekler, sadece önemli oranda bulunduklarında tane büyümesine engel oluşturur.
Bir toz kompakt (sıkıştırılmış toz yığınında) bulunan her bir partikülde buna benzer birçok temas noktası vardır. Sinterleme prosesinin ilerlemesiyle temas eden partiküller arasındaki bağlar genişler ve birleşir. Her bir temas noktasında katı-buhar arayüzeyi yerine bir tane sınırı büyür.
Uzun süreli bir sinterleme sonucunda iki partikül tamamen birleşerek başlangıç çapının 1.26 katı büyüklüğünde tek bir küre oluşmasına neden olur. Boyun büyümesi parçacıklar arası temas noktasında tane sınırını oluşturur. Eğer süre yeterli ise iki parçacık birleşerek sonunda iri bir parçacık oluşturur.
İyi sinterleme için, hızlı tane büyümesi aşamasında dahi, gözeneklerin tane sınırı ile bağlantılı olmasının sağlanması önemlidir.
Parçacıklar arasındaki temas noktaları büyüyerek boyun oluşturur. İlk aşamadan sonra, tane sınırı ve gözeneklerin düzenlenmesi sinterleme hızını kontrol eder. Ara aşamanın başlangıcında, gözenek geometrisi oldukça girintili-çıkıntılı olup gözenekler tane sınırlarının kesişme noktalarında yer alır. Sinterlemenin ara aşamasının devamında, gözenek geometrisi silindirik hale gelir ve sonra yoğunlaşma ile birlikte kapalı küre şeklinde gözeneklere dönüşür. Çünkü yoğunlaşma gözenek çapını küçültürken tane büyümesi gözenek boyunu arttırır.
Sinterleme ilerledikçe, gözenek tane sınır etkileşimi üç şekil alabilir:
• Gözenekler tane sınırlarında kalarak tane büyümesini engeller
• Gözenekler hareket eden tane sınırları tarafından sürüklenerek tane büyümesini yavaşlatır.
• Tane sınırları gözeneklerden koparak ayrılır.
Son durumda, tane içinde izole edilmiş gözenekler oluşur ve yoğunlaşma ilerlemez. Tipik sinterleme sıcaklıklarında, malzemelerin çoğu orta veya aşırı düzeyde tane büyüme hızları gösterir.
Yüksek sıcaklıklarda, tane sınırı hareketi gözenekten ayrılmaya yol açar. Düşük sıcaklıklarda, tane büyümesi yavaş olduğundan gözenekler tane sınırına bağlı kalır. Gözenekler hareketi yüzey yayınımı ve buharlaşma-yoğunlaşma ile mümkündür. Sonuç olarak, sinterlemede mikroyapı gelişiminin ana belirleyicisidir.
Sinterleme İçin İtici Kuvvetler
Sinterleme için itici güç sistemin serbest enerjisinin düşürülmesidir. Partiküllerin (veya tanelerin) büyümesi, toplam tane sınırı alanının azalması serbest enerjide düşmeye neden olur. Metallerde tane sınırı hareketi eğrilik merkezinden doğru olan yönde meydana gelir.
Tane sınırlarının konkav tarafında (iç bükey) yer alan atomlar konveks (dış bükey) taraftaki atomlara göre daha sıkı bir sıralama gösterdiklerinden atomsal hareket (sınır hareket) sınır konkav tarafına doğrudur.
Sınırın eğrilik derecesinin büyük olduğu ölçüde sınırın hareket hızı artar. Atomların ve sınırın hareketine etki eden önemli bir faktör de sıcaklıktır. Sıcaklığın artması atom yayınımını hızlandırır. Tane sınırlarının bu şekilde hareketi sonucu, küçük taneler kaybolurken, büyük taneler oluşur.
Atomsal Taşınım Mekanizmaları
Taşınım mekanizmaları itici güçlere karşılık olarak kütle akışının nasıl olduğunu belirler. Yüzey taşınım mekanizmaları kütle akışının iki sınıfıdır. Aralarındaki fark atomların boyun bölgesini nerden doldurmaya başladıkları ile ilgilidir. Yüzey taşınımında atomlar boyun bölgesini yakınındaki gözenek yüzeylerinden başlayarak doldurur. Hacim taşınımı ise tane sınırlarındaki atomları kullanarak bunları boyun bölgesinde yeniden konumlar.
Yüzey taşınımı çekme veya yoğunluk artışı olmayan boyun büyümesi içerir. Yüzey yayınımı ve buharlaşma-yoğunlaşma, yüzey taşınımı kontrollü sinterlemede en önemli katkı yapan iki olaydır.
Birçok malzemenin düşük sıcaklıkta yapılan sinterlemesinde yüzey yayınımı baskındır. Buharlaşma-yoğuşma, kurşun içeren düşük kararlı malzemelerin sinterlenmesi dışında pek önemli değildir. Buna karşılık, hacim-taşınım-kontrollü sinterleme çekmeye neden olur. Kütle, tane sınırından bazen de tane içinden gelir ve boyun yanındaki gözeneğin yüzeyinde toplanır. Hacim-taşınım mekanizmaları hacim yayınımı, tane sınırı yayınımı, plastik akış ve viskoz akış içerir. Özellikle preslenmiş tozlarda plastik akış ısıtma sırasında son derece önemlidir.
Ancak toz tepe sıcaklığına ulaştığında plastik akış önemini kaybeder. Bunun tersine, cam ve plastikler gibi amorf malzemeler viskoz akış ile sinterlenir. Bu durumda parçacıkların birleşme hızı parçacık boyutuna ve malzeme viskozitesine bağlıdır.
Metallerde viskoz akış tane sınırında sıvı fazların olması durumunda mümkündür. Kristalli malzemelerin yoğunlaşmasında tane sınırı yayınımı oldukça önemlidir ve pek çok metalin yoğunlaşmasında esas yayınım mekanizmasıdır. Yüzey ve hacim taşınım işlemleri boyun büyümesine neden olurken, aralarındaki en önemli fark sinterleme esnasındaki yoğunluk veya çekmedir. Hacim taşınım mekanizmaları genelde yüksek sıcaklıklarda baskındır.
Sıvı Faz Sinterlemesi
Sıkıştırılan metal tozları, mutlak ergime sıcaklıklarının yarısı üzerindeki sıcaklıklara kadar ısıtıldıklarında sıkı bağ oluştururlar. Sinterleme şekillerinin hepsinde bulunan ortak bir özellik tane yüzey alanında meydana gelen bir azalma ve bunu takiben parça mukavemetinin artmasıdır. Bu durum sinterleme sıcaklığındaki atomik hareketlerin neden olduğu parçacıklar arası bağların oluşumu ile meydana gelir.
Sıvı faz sinterlemesi sırasında, sıvı bir faz sinterleme sıcaklığında katı bir toz kümesiyle aynı anda bulunur. Genellikle sıvı faz, sinterleme esnasında parçacıklar arası bağ oluşumunu arttırır ve de en önemli avantajı, sinterleme hızına olan katkısıdır. Sıvı fazın oluşturduğu kılcal çekim kuvvetleri partikülleri birbirlerine doğru çeker ve dışarıdan bir basınç olmaksızın hızlı bir yoğunlaşma meydana getirir.
Bunun dışında oluşan sıvı faz katı parçacıklar arasındaki sürtünmeyi azaltarak yeniden düzenlenmeyi hızlandırır. Katı partiküllerin kenarları ve köşeleri yüksek kimyasal potansiyele sahip oldukları için sıvı faz içerisinde çözünmekte ve böylelikle partiküller yeniden düzenlenmektedir. Parçacıklar arası bağlanmaya eşlik eden mukavemet, süneklik, iletkenlik, manyetik geçirgenlik ve korozyon direnci gibi faktörler gözenek yapısında ve parça özelliklerindeki önemli değişikliklerdendir.
Kaliteli parça üretiminin bir yolu da sıvı faz sinterlemesidir. Sinterleme sırasında oluşan sıvı faz kapiler etki ile parçacıklara yeterli iç basınç uyguladığından dış basınca gerek kalmaz. Kapiler kuvvet büyük ölçüde dış basınca eşit etki yapar.
Sıvı faz sinterlemesinde sıvı faz oluşumu için iki ana mekanizma vardır. Bunlardan birincisi, farklı kimyasal bileşimlerde toz kullanmak olup en yaygın olarak kullanılan yöntemdir. Sinterleme sırasında farklı bileşimdeki tozların etkileşimi ile sıvı faz oluşur. İkincisi ise sıvı fazın toz karışımında bulunan bileşenlerinden bir tanesinin ergimesi veya ötektik faz oluşumu ile oluşmasıdır. Oluşan bu sıvı faz çözünme durumuna göre sinterleme sırasında alaşım oluşumu ile ortadan kalkabilir (geçici sıvı faz sinterlemesi veya reaktif sinterleme) veya sinterleme süresince içyapıda sürekli olarak bulunabilir (sürekli sıvı faz sinterlemesi). Farklı bir yöntem de ön alaşımlı tozun solidüs-liküdüs sıcaklığı arasında sinterlenmesi suretiyle sıvı+katı karışımı oluşturarak yapılan solidüslü sinterlemedir.
Sıvı faz sinterlemesi elektronik seramikler, abrazivler, ferritler, yüksek sıcaklık seramikleri, elektrik kontak malzemeleri, sinterlenmiş karbürler, bronz yataklar, süper alaşımlar, otomotiv yapı parçaları gibi birçok uygulamada kullanılmaktadır.
En önemli avantajı sinterlemeyi hızlandırmasıdır. Sıvı fazda difüzyon hızlı olur ve ıslatan sıvının oluşturduğu kapiler çekme kuvveti hızlı yoğunluk artışı sağlar
Sıvı faz parçacıklar arası sürtünmeyi azaltarak yeniden düzenlemeyi hızlandırır. Katı parçacıkların sivri uçları sıvı tarafından çözündürüldüğü için parçacıkların daha iyi yerleşmesini sağlar.
Tane büyüklüğünün kontrolü mümkündür. Sıvı faz sinterlemesine uygun birçok sistemde ergime noktası yüksek olan faz aynı zamanda sert fazdır. Sert ve gevrek fazın yüksek oranda olmasına rağmen iki fazlı sünek kompozit üretebilir.
Sıvı faz sinterlemesinin en önemli sakıncası fazla oranda sıvı faz oluşumuyla ortaya çıkan şekil bozulmasıdır. Mikro yapıyı kontrol eden bazı parametreler üretilen parçanın özelliklerini de kontrol etmektedir. Sinterlemenin başlangıç aşamasında sıvı, katı ve buhar olmak üzere üç faz vardır. Buna göre arayüzey enerjileri, çözünürlük, viskozite, difüzyon etkileri ile birlikte sıvı faz sinterlemesinin analizini güçleştirmektedir. Hızlı sinterleme işlemin kontrolünü ve elde edilecek özelliklerin önceden tahminini zorlaştırmaktadır.
Sıvı Faz Sinterleme Aşamaları
Başlangıçta, ısıtma sırasında taneler katı hal sinterlemesi ile birbirine bağlanmaktadır. İlk sıvı oluştuğunda, tanelerin yeniden düzenlenmesi ile hızlı bir yoğunluk artışı olmaktadır. Oluşan sıvı katıyı ıslatarak oluşmuş olan katı bağlarını çözer ve yeniden düzenlenmeyi sağlamaktadır. Bundan sonra, çözelti tekrar çökelme olarak bilinen işlemde, sıvı katı atomların taşıyıcısı olmaktadır. Bu aşamada daha küçük tane kütleleri sıvı içinde çözünür, sıvı içinden yayınır ve daha sonra büyük tanelerin üzerine çökelir. Katı tane çözünürlüğü tane boyutu ile ters orantılıdır. Dolayısıyla, öncelikle küçük taneler sıvı faz içinde çözünür. Zamanla tane sayısı azalır ve tane boyutu artar. Ana toz proses sırasında katı olarak kalırken katkı tozu sıvı faz oluşumunu sağlar.
Çözelti-tekrar çökelme işlemi, küçük tanelerin çözünmesi ve daha sonra büyük tanelerin üzerine katı-faz çökelmesi ile tane büyümesini sağlar. Tane büyümesinin yanı sıra, işlem tane şekli yerleşimine imkan tanır, katının daha iyi paketlenmesini ve kalan boşlukların doldurulması için sıvının serbest bırakılmasını sağlar.
Yayınım hızı genellikle çok yüksektir ve tam yoğunluğa dakikalar içinde ulaşılabilir. Ancak, düşük çözünürlük veya iri taneli sistemlerde yoğunlaşma yavaştır. Sıvının hacim oranı arttıkça gözenekleri dolduracak sıvı miktarı daha fazla olduğundan yoğunlaşma da kolaylaşır. Ancak yerçekiminden dolayı ham parça çökmesi sorun olur.
Eğer sıvı yoksa sinterleme katı-hal işlemleri ile gerçekleşir. Fazla sıvı olması durumunda ise (yaklaşık %35 hacim oranı), sıvı oluşumu ile birlikte taneler arasındaki bütün gözenekler dolar. Ancak, bu durumda ham parça şeklini korumayabilir. Ara sıvı oranlarında, ham parça şeklini korur, ancak katı taneler arasındaki boşlukları doldurmak için yeterli sıvı yoktur. Bu tür durumlarda, toz karışımdaki kimyasal gradyanlardan dolayı sinterleme ısıtma sırasında olur. Sıvı oluştuğunda, kılcal kuvvetler taneleri yeniden düzenler, daha sonra tane şekli yerleşimi ye yoğunluğun daha artmasına yol açan çözelti-tekrar-çökelme oluşur ve son yoğunlaşma katı iskeletin sinterlemesine bağlıdır.
Sıvı Fazlı Sinterleme Çeşitleri
Sürekli Sıvı Faz Sinterlemesi
Bu yöntemde, sinterleme işleminin yüksek sıcaklık aşamasında içyapıda sürekli olarak bulunan sıvı faz, hızlı yoğunluk artışı ile tane büyümesine neden olur. Başlangıçta katıyı ıslatan sıvının katı parçacıklar üzerine uyguladığı kapiler kuvvetler yardımıyla parçacıkların yeniden düzenlenmesi ile hızlı bir yoğunluk artışı olur. Yeniden düzenleme ile erişilecek yoğunluk artışı, oluşan sıvı faz miktarına, parçacık büyüklüğüne ve katının sıvı fazda çözünürlüğüne bağlıdır. Sıkıştırılmış kütle içerisindeki gözenek miktarının azalması sıvı faz akışını güçleştirir. Bu nedenle yoğunlaşma hızı giderek azalır. Belirli bir aşamadan sonra çözünürlük ve yayınma (difüzyon) daha etkin hale gelerek, çözünme ve tekrar çökelme safhasına geçilir. Bu safhada yoğunlaşma ve tane büyümesine katkıda bulunan Ostwald olgunlaşması ve tane şekli oluşumunun her ikisi de difüzyon kontrollü işlemlerdir. Bu işlemin oluşabilmesi için katı fazın sıvı fazda çözünürlüğünün olması gerekir. Alaşım oluşumu ile ergime sıcaklığının düşmesi sinterleme özelliğinin iyileştiğinin bir göstergesidir.
Başarılı sistemlerde oluşan sıvı faz katı fazı ıslatır ve aynı zamanda katıyı çözer. En başarılı sıvı faz sinterlemesi özelliği gösteren sistemler ötektik sistemlerdir.
Solidüs üstü sinterlemede ön alaşımlı toz, solidüs-liküdüs sıcaklıkları arasında bir sıcaklıkta sinterlenir. Eğer solidüs-liküdüs sıcaklıkları aralığı geniş ise işlemin kontrolü daha kolay olur.
Isıtma sırasında her toz parçacığı içinde sıvı faz oluşur. Bu durum parçacıkların tekrar parçalanmalarına neden olmakta ve karıştırılmış tozlara oranla sıvı faz dağılımı daha homojen olmaktadır. Sıvı oluşumuyla birlikte yoğunluk artışı çok hızlı olmakta ve artan sıvı oranıyla artmaktadır.
Solidüs üstü sinterlemeye örnekler; yüksek karbonlu çelikler, takım çelikleri, nikel esaslı süper alaşımlar ve kobalt esaslı aşınmaya dayanıklı alaşımlardır.
Geçici Sıvı Faz Sinterlemesi
Sinterleme sırasında oluşacak denge fazı katı ise sıvı faz, difüzyon homojenizasyonu ile kaybolur. Bu yöntemde sıkıştırılabilirliği yüksek saf element tozları kullanılabilir ve sürekli sıvı faz sinterlemesinde (SSFS) görülen tane irileşmesi olmaz. Geçici sıvı faz sinterlemesi (GSFS)’ne örnek olarak civa ve gümüş esaslı diş amalgamları, gözenekli bronz yataklar, demir esaslı yapı alaşımları, bakır alaşımları, magnetik malzemeler ve alümina esaslı seramik malzemeler verilebilir. GSFS uygulanabilmesi için bileşenlerin birbiri içinde çözünebilmesi ve son bileşimin tek faz bölgesinde olması gerekmektedir.
Başlangıçta ergime noktası düşük olan bileşenin oluşturduğu sıvı, katı parçacık sınırına nüfuz ettikçe yerlerinde boşluk olur. Oluşan sıvı katıyı ıslatmalı ve difüzyon hızını artırmalıdır. Eğer artan alaşım elementi oranı ile ergime sıcaklığı düşüyorsa ve bileşenler birbiri içinde çözünüyorsa bu şart sağlanmış olur. Sıvı faz oluştuktan sonra hızlı bir sinterleme oluşur. Yoğunluk artışı oluşan sıvı miktarına ve sıvının içyapıda bulunma süresine bağlıdır.
Reaksiyonlu Sinterleme
Toz karışımı karşılıklı difüzyonla sıvı fazın oluştuğu sıcaklıkta sinterlenir. Oluşan sıvı faz geçici olup son ürün bir metaller arası bileşiktir. Bileşenler arasındaki reaksiyon çoğunlukla egzotermiktir. Sıvı oluşumu ve egzotermik reaksiyon sonucu ısınmasıyla birlikte hızlı bir sinterleme gerçekleşir.
Özellikle karşılıklı difüzyon hızlarının farklı olması ve bileşiğin teşekkül ısısının yüksek olması durumunda, sinterleme sırasında şişme olur. Gözenek oluşumu da söz konusudur. Sıvı akışı ve homojen bir içyapı oluşumu için reaksiyon sıcaklığının ötektik sıcaklığın üzerinde olması gerekir.
Reaksiyonlu sinterleme henüz geliştirme aşamasında olup metaller arası bileşiklerin, seramiklerin ve değişik bileşiklerin şekillendirilmesinde kullanılmaktadır.