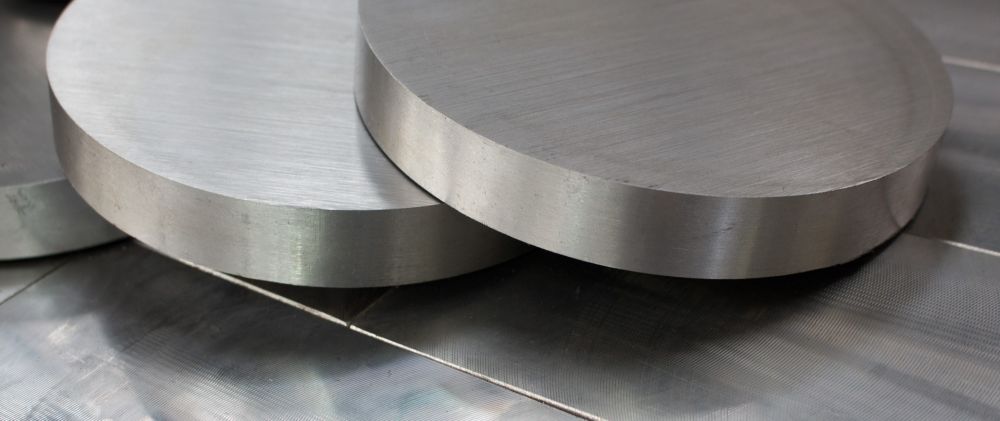
Toz enjeksiyon kalıplama (TEK) plastik enjeksiyon kalıplamadan türetilmiştir. 1896’da Hyatt kardeşler fildişinden yapılmış bilardo toplarının yerini alacak seluoiti icat etmişlerdir. 1872’de bu konuda patent almışlardır. Fakat plastik enjeksiyon kalıplamanın ticari başarıyı yakalaması 1930’ları bulmuştur. O zamanlar seramik enjeksiyon kalıplama da ilk defa ortaya çıkmıştır. Ancak seri üretim gerçekleştirecek makine kontrol sistemleri 1970’lere kadar olmadığı için TEK’in ticari ölçekte başarı göstermesi 1977’leri bulmuştur. Endüstrinin bu işten kar etmesi ise en az bir 15 yılı daha almıştır.
TEK teknolojisi karmaşık ve zor parçaların kaliteli bir biçimde ve yüksek miktarlarda üretilmesini gerektiren durumlarda diğer imalat teknolojilerine göre avantajlar taşımaktadır. Yüksek yüzey kalitesi, sıkı ölçü toleranslarını karşılayabilme kabiliyeti, yüksek yoğunluk nedeniyle üstün mekanik özellikleri, seri imalata yatkın işlemleri, malzeme tasarrufu sağlayan tasarım ve imalat seçenekleri, çevresel faktörler ve geri dönüşüm açısından gelişmiş uygulamaları ve hepsinden önemlisi maliyet avantajı TEK teknolojisinin diğer üretim metotlarına göre başlıca üstünlükleri olmuştur.
Proses Akışı
TEK yönteminde işlem seçilen tozlar ve bağlayıcıların karıştırılması ile başlamaktadır. Yüksek sinterleme yoğunluğuna ulaşabilmek için genellikle küresel şekle yakın ve ortalama çapı 20 µm altında olan parçacıklar kullanılır. Kullanılan bağlayıcılar termoplastik karışımlardır ve içlerinde mumlar, polimerler, yağlar, yağlayıcılar ve yüzey aktif maddeler vardır.
Bağlayıcılar viskoz akış özelliklerine yardımcı olarak karışımın karmaşık kalıp geometrisini doldurmasını sağlamaktadır. Bağlayıcı kalıpta donduktan sonra parça kalıptan çıkartılır. Ardından bağlayıcı uzaklaştırılır ve toz yapı sinterlenir. Ürün daha sonra yoğunlaştırılabilir, ısıl işlem veya talaş kaldırma yapılabilir. Sinterlenen parça enjeksiyon ile kalıplanmış plastik ile aynı şekil ve boyut hassasiyetine sahiptir. Ancak, bu metotla elde edilen parçanın performansına polimerlerin ulaşabilmesi mümkün değildir.
TEK’ de parça şekillendirme için kullanılan cihazlar, plastik enjeksiyon kalıplamada kullanılan cihazlarla aynıdır. Çoğu kalıplama makinesi, ısıtılmış ve basınçlı bir silindirdeki besleme stokunun bir girişten geçerek kalıbı doldurması şeklinde çalışır. Kalıbı doldurmak için gerekli basınç bir piston veya ileri-geri hareketli vida ile sağlanır. Besleme stoku besleme hunisinden soğuk granüller halinde silindire girer. Silindir boyunca ilerlerken bir taraftan da bağlayıcının ergime sıcaklığının üzerinde ısıtılır. Besleme stoku sıcak, kalıp ise soğuk olduğundan erken donma problemini engellemek için doldurma çok kısa sürede gerçekleştirilmelidir. Doldurma, vidayı piston gibi kullanarak yapılır. Kalıp dolumundan sonra, parçanın çekme boşluklarını en aza indirmek için besleme stoku katılaşıncaya kadar basınç muhafaza edilir. Yeterli soğumadan sonra sertleşmiş parça çıkarılır ve döngü tekrarlanır.
Önerilen Makale: Sementasyon çeliği malzemeler ve uygulamaları hakkında detaylı bilgi almak için
sementasyon çeliği sayfamızı ziyaret etmenizi tavsiye ederiz.
Toz Enjeksiyon Kalıplama Tozları ve Özellikleri
Sinterlenen parçanın son özelliklerini tozun başlangıç özellikleri belirlemektedir. Bu yüzden toz özelliklerinin bilinmesi çok önemlidir. Yüksek paketleme yoğunluğu ve düşük maliyet için uygun boyut dağılımı, topaklanma olmaması, küresel parçacık şekli, hızlı sinterleme için 20µm altı parçacıklar, gözeneksiz toz parçacık ve temiz parçacık yüzeyi ideal TEK tozunda aranan özelliklerdir.
Partikül Boyutu, Dağılımı ve Şekli
Parçacık şekli; paketlenmeyi, akışı ve sıkıştırılabilirliği etkilemektedir. Aynı zamanda bir tozu üretmek için kullanılan şartların belirlenmesine yardımcı olmaktadır. Parçacık şeklinin sayısal ölçüleri, genellikle mikroskop görüntülerinden elde edilir. Basit bir tanımlayıcı ifade, en büyük parçacık boyutunun en küçük parçacık boyutuna bölümü olarak tanımlanan boyut oranıdır.
TEK için ideal tanecik şeklinin belirlenmesi kolay değildir. Çoğu kez bir işlemin bir basamağı için istenen özellik diğer bir basamak için istenmeyebilir. Örnek olarak; küresel bir toz, yüksek paketleme yoğunluğu sağlar ve böylelikle sinterleme sırasında oluşan çekme (daralma) miktarını azalttığı gibi, katılacak bağlayıcı miktarını da en aza indirger, ancak küresel parçalar arasında mekanik bağlılık olmadığından ham mukavemet düşer. Özellikle bağlayıcı giderme sırasında ve sinterlemede şekil kaybı olacaktır. Buna karşılık karmaşık şekilli ya da silindirik yumrumsu bir toz, düşük paketleme yoğunluğu verecektir. Bu durum daha fazla bağlayıcı gerektirmekte ve sinterleme sırasında daha fazla çekmeye neden olmakta diğer taraftan bu toz şekilleri daha iyi ham mukavemet sağlamaktadır. Karmaşık şekilli tozlar bağlayıcı giderme ve sinterlemede parça seklini daha iyi korumaktadırlar. Yüzey sürtünmesinin parçacıklar arası büyük güç haline geldiği çok küçük parçacıklarda (1 µm civarı parçacıklarda) şekil koruma sorunu bir ölçüde azaltılmıştır.
TEK için ideal toz şekli tanımlanmıştır. Toz partikül L/W oranı 1,2 ile 1,5 arası olan oval biçimli parçacıktır. Bu tanecik sekli tozlar arası yeterli bağlılığı sağladığı gibi küresel taneciklere nazaran daha yüksek paketleme yoğunluğu gösterir. Yüksek paketleme yoğunluğu da yapıda kullanılan bağlayıcı miktarını en aza indirir.
Ortalama tane büyüklüğü, TEK’ de çok önemli bir faktördür. TEK’ de ideal tanecik büyüklüğü 2 ve 8 µm arasında olduğunu belirtilmiştir. Tanecik büyüklük dağılımının genişliği de aynı derecede öneme sahiptir.
Partiküller Arası Sürtünme ve Yüzey Alanı
Genel olarak partiküller (tozlar) arası sürtünme, tozun akışkanlık ve paketlenme özellikleri üzerine önemli bir etkide bulunmaktadır. Partiküller arasındaki sürtünme, yüzey alanı, yüzey pürüzlülüğü ve yüzey kimyasına bağlı olarak gerçekleşir. Yüzey alanı arttıkça, toz kütlesindeki sürtünme miktarı artar. Bunun sonucunda partiküller düşük akışkanlık ve paketlenme özelliği gösterir. Sürtünme kavramı özellikle tozun otomatik olarak kalıba doldurulup sıkıştırılması, paketleme, transport ve karıştırma gibi durumlarda önemlidir.
Akmaya karşı direnç sürtünmenin esas göstergesidir. Yoğunluk ve paketlenme özellikleri yakın partiküllerin birbiri üzerindeki düşük akışı nedeni ile azalır. Bu durumda partiküller arası sürtünmenin ölçülmesine dikkat edilmelidir. Bir tozun görünür yoğunluğu, tozun yığın konumunda karıştırmasız elde edilen yoğunluğudur. Vurma yoğunluğu, herhangi bir dış basınç uygulanmaksızın titreşim ile elde edilen en yüksek yoğunluktur.
Teorik yoğunluk veya kütlesel yoğunluk, bir toz için çeşitli kitaplarda da belirtilen yoğunluk olup herhangi bir porozitenin yer almadığı yoğunluktur. Yığın açısı ise diğer bir sürtünme indeksini verir. Alfa (α) açısı, tozun bir yığın oluşturacak şekilde akması ile oluşur. Yığın açısı, doğal akışın gerçekleştiği durumlarda tozun eğilmesi veya döndürülmesi sonucu oluşturduğu açı olarak da belirlenebilir. Sonuç olarak akış hızı, tozun küçük bir açıklıktan aşağıya doğru yerçekimi altında beslenme hızı olarak ölçülür. Çok düşük boyutlu elekaltı tozlar yüksek partiküller arası sürtünme nedeni ile birbiri üzerinden akamazlar. Bu tür tozlar serbest akamayan tozlar olarak ifadelendirilir ve şekillendirilmeleri zordur.
TEK’te Kullanılan Tozlar
TEK işleminin başarılı kontrolü için toz özellikleri önemli faktördür. Optimum işlemler için gerekli partikül özellikleri bazı çelişkilere neden olmaktadır. Örneğin, düzensiz bir partikül ham mukavemeti arttırmaktadır. Bunun yanında düşük paketleme yoğunluğu karışımda yüksek viskozite, düşük sinterleme yoğunluğu sağlamaktadır. Küresel partiküllerde ise tam tersi özellikler sağlamaktadır.
TEK’te Kullanılan Bağlayıcılar ve Özellikleri
Bağlayıcı, tozu istenen şekle sokmak ve o şekli sinterlemeye kadar muhafaza etmek için geçici olarak kullanılan bir araçtır. Böylece, parçanın son bileşiminin belirlenmesinde bir etkisi olmamasına rağmen, bağlayıcının şekillendirme işlemi üzerinde etkisi vardır.
Bağlayıcılar etkili yapıştırıcılar olup ham kütlenin dayanımını sağlar. Kalıp aşınmasını en aza indiren yağlayıcılardan farklı olarak, bir bağlayıcı esas olarak dökülmüş kütlenin ham dayanımını arttırmak üzere seçilir. Sert parçacıklar için, bağlayıcının rolü, kusursuz şekil elde etme açısından yağlayıcının rolünden daha önemlidir. Ucuz olmaları ve ısıl ergime ile kolayca uzaklaştırılmaları nedeniyle genelde basit mum benzeri polimerler kullanılır. Başarılı bağlayıcılar kolay dağılma, kararlı viskozite, tozlara yapışma ve şekillendirilmiş parçalara iyi dayanım sağlama gibi şartları sağlar. TEK yönteminde kullanılan bağlayıcılar termoplastik karışımlardır ve içlerinde mumlar, polimerler, yağlar, yağlayıcılar ve yüzey aktif maddeler vardır.
Bağlayıcı viskoz akış özelliklerine yardımcı olarak karışımın karmaşık kalıp geometrisini doldurmasını sağlar. Bağlayıcı kalıpta donduktan sonra parça kalıptan çıkartılır. Ardından bağlayıcı uzaklaştırılır ve toz yapı sinterlenir.
Bağlayıcı Özellikleri
TEK’ de, toz özelliklerinin yanı sıra bağlayıcının özellikleri de önemlidir. Bağlayıcıdan, tozları istenilen şekilde paketlenmesi ve sinterlemeye kadar ön-ürün şeklinin korunmasına yardımcı olması ve bitmiş üründen ise tamamen uzaklaşması istenir. Bağlayıcılar, besleme stokunun kolay enjekte edilmesi için düşük viskoziteye sahip olmalı, homojen bir besleme stoku hazırlamak için kalıba yapışmamalı ve uçucu olmamalı, kademe kademe sistemden ayrılmalı, kolayca uzaklaştırılabilmeli, uzun raf ömrüne sahip olmalı, ucuz olmalı, düşük ısıl genleşme katsayısına sahip olmalı, kalıplama ve karışım sıcaklığında bozulmamalı ve akış esnasında tozdan ayrılmamalı, toz ile kimyasal tepkimeye girmemelidir. Bağlayıcılar mum veya yağ esaslı bağlayıcılar, su esaslı bağlayıcılar, polimer çözelti esaslı bağlayıcılar olmak üzere üç ana gruba ayrılır. Düşük viskoziteye sahip olan bağlayıcıya toz ilavesi viskoziteyi 10 ile 10000 kat arttırır. Saf bağlayıcı için gereken viskozite 10 Pa.s olabilir. Bu kısıtlama yüzünden, uygulamada çok düşük viskozitelere sahip mum ve küçük molekül ağırlıklı bağlayıcılar kullanılmaktadır.
Bağlayıcı, hataları en aza indirecek ve çıkarılma zamanını azaltacak şekilde tasarlanmalıdır. Genellikle bir bağlayıcı sistemi birbiri içinde çözünen çeşitli bileşenlerden meydana gelmektedir. Çoklu bileşenler çıkarılma sırasında aşamalı bozunmaya imkân verirler. Bileşenlerden biri kısmen açık gözeneklerden çıkarılır, kalan bağlayıcı, taneleri işlemin bu ön evresinde bir arada tutmaya yardım eder. Önürün seklinin muhafazası için iskelet bağlayıcı, tanecikleri ıslatarak onlar üzerinde bir kılcal çekim etkisi uygulamalıdır. Sonunda iskelet bağlayıcı da ön-ürünün yenilmesine yol açabilecek iç buhar basıncı oluşmadan gözeneklerden buharlaşarak çıkar. Bu yöntem tek bileşenli sistemlerden daha çabuk bir şekilde bağlayıcının ayrılmasını sağlar. Çoğunlukla bağlayıcının yavaş çıkarılması ön-ürünü gerilme kırıklarından korur.
Bağlayıcının bozunması ile oluşan kimyasallar sinterleme fırınında ön-ürünün korozyonuna yol açmamalıdır. Çünkü bağlayıcının ön-üründen tam olarak ve son ayrılması sinterleme sırasında meydana gelir.
TEK’te Kullanılan Bağlayıcılar
Genel sınıflamada TEK uygulamalarında kullanılan beş tür bağlayıcı bulunmaktadır. Bunların çoğu polimer esaslıdır:
• Termoplastik bileşikler
• Termosetler
• Su bazlı sistemler
• Jelleşen sistemler
• İnorganikler
Bunların çok çeşitli kombinasyonları mümkündür. Polimerler çok bilinen termoplastik ve termoset bileşikler kadar jelleşen sistemleri de içermektedirler. İnorganik bileşikler bir kaç sistem içerisinde kullanılırlar. Bunlar kristalleşen tuzlar ve sodyum silikat reaksiyonlarıdır.
Termoplastik ve termoset esaslı bağlayıcılar yüksek ham mukavemet değerleri verdiğinden dolayı sıkça kullanılırlar. Özellikle termoplastikler tam mukavemetlerinin yanı sıra düşük viskozite ve bağlayıcı giderme esnasında mükemmel sonuç verirler. Kısa molekül zincir uzunluğuna sahip termoplastikler düşük sıcaklıklarda kolaylıkla bünyeden uzaklaşırlar. Parafin, mikrogliserin mum ve doğal mumlar gibi termoplastikler ise düşük viskozite değerlerinin yanı sıra bağlayıcı giderme aşamasında düşük sıcaklıklarda bünyeden ilk uzaklaşan bağlayıcılardır. Termoset esaslı bağlayıcılar termoplastiklere göre daha yüksek ham mukavemet değerlerine sahiptirler fakat viskozite değerleri yüksektir.
Tipik bir bağlayıcı bileşimi parafin mumu veya diğer katı mumlardan oluşur ve birlikte %30 polipropilen ve tozun bağlayıcıya yapışmasını sağlamak amacıyla yağlar veya başka ıslatıcı maddeler bulunur. Su esaslı bağlayıcılar suda kolaylıkla eriyebilen polimer ve jel içerikli bağlayıcılardır. Genellikle düşük basınç ve sıcaklıkta kullanılırlar. Bağlayıcı giderme işlemi genellikle düşük sıcaklıklarda ve suda gerçekleştirilir. Paslanmaz çelikler gibi oksidasyon problemi taşımayan tozlarla kullanımı oldukça yaygındır.
Toz ve Bağlayıcı Karışımları
TEK işleminde toz bağlayıcı karışımının yani besleme stokunun kalıba basılabilirliği viskoz akışa bağlıdır. Bu kendine özgü reolojik karakteristikleri gerektirir. Kalıplamada en önemli özellik viskozitededir. Yüksek viskozite kalıplamayı zorlaştırır. İkinci özellik ise elastikiyettir ve Hook Kanunu ile ifade edilmektedir. TEK yönteminde toz bağlayıcı karışımının viskozitesi ile elastikiyet karakteristikleri beraber görülür ve buna viskoelastisite denir. Kalıplamadan sonraki soğuma anında bu karakteristik çok önemlidir.
Besleme stoku bileşimi, parçacıklar yüksek paketleme yoğunluğuna erişebilecek ve karışımın yoğunluğu düşük tutulacak şekilde hazırlanır. Parçacıkların arasındaki boşlukları dolduracak ve kalıplama esnasında parçacıkları yağlayarak kaymasını sağlayacak kadar bağlayıcıya ihtiyaç vardır. Tipik viskozite 100 Pa.s civarındadır. Kritik katı yükleme oranında parçacıkların bağlayıcı tabakası ile hiçbir nokta teması yoktur. Buna göre, kritik katı yükleme Φc, karışımın yoğunluğunda maksimuma karşılık gelir ve bu noktada karışımın viskozitesi sonsuza yaklaşır. Fazla katı içeren karışımlarda, parçacıklar arasındaki boşlukları dolduracak yeterince bağlayıcı bulunmadığından karışımın yoğunluğu azalır. Viskozite bileşime çok duyarlı olduğundan, besleme stokundaki herhangi bir homonjensizlik, karışımın kalıp boşluğuna düzgün akmasını engeller. Çok yüksek kayma hızlarında, ağır tozlar düşük yoğunluklu bağlayıcıdan ayrılır ve viskozitede ani bir artışa neden olur. Kalıp boşluğunun dolması karışımın viskozitesine bağlı olduğundan, bağlayıcıdan tozun ayrılması homojen parça üretimini engeller.
Toz-Bağlayıcı Oranı ve Karakteristiği
Tozun paketlenme özelliğine bağlı olarak bağlayıcı, karışımın hacminin %40’ını oluşturabilir. Düşük yoğunluklu tozlarda bağlayıcının ağırlık oranı %15 olabildiği gibi, yüksek yoğunluklu tozlarda bu oran %2’ye kadar düşebilir. Besleme stoku (toz ve bağlayıcı karışımı) oluşturulurken miktarları üzerinde karar vermek gerekir. Toz fazla, bağlayıcı az olursa, viskozite aşırı artar ve kalıplama zorlaşır, bağlayıcının az olması nedeniyle tozlar arasında bağlayıcılar hapsolur. Ayrışmada bu toz arasında kalan bağlayıcı çatlamaya neden olur. Çünkü içeride gaz oluşur. Bağlayıcının fazla olması da kabul edilemez. Hem çok artık maddelidir, hem takip eden işlemleri yavaşlatır, hem de sinterlemede büyük ölçüde boyut küçülmesine neden olur. Ayrıca fazla bağlayıcı kalıplama sırasında tozdan ayrılabilir, homojensizliğe ve muhtemel boyutsal kontrol sorunlarına, bağlayıcı giderme işleminde de çökmeye neden olur. İdeal durum toz parçacıkların temas halinde olması ve bağlayıcının içinde boşluk bulunmamasıdır. Her toz için optimal bağlayıcı konsantrasyonu bulunmaktadır. Optimal bağlayıcı oranı seçiminde ilk esas bağlayıcının toz parçacıkları arasındaki boşlukları iyi doldurması ve makul düşüklükte viskozite sağlamasıdır.
Pek çok toz bağlayıcı karışımları için, basit bir viskozite ölçümü ergime akış indeksidir. (EAI) . EAI, önceden belirlenen bir basınç altında, kılcal bir borudan 10 dakikada akan besleme stokunun gram cinsinden miktarıdır. Besleme stokunun viskozitesi azaldıkça, daha küçük çaplı kılcal tüpler kullanılır. Diğer ölçüm yöntemleri karıştırma torku veya kılcal ekstrüzyon testleridir. Bağlayıcıya toz ilavesi arttıkça besleme stokunun viskozitesi de artar.
Kritik katı yükleme, viskozitenin akmayacak kadar çok büyük olduğu noktaya karşılık gelir. Bu nokta, toz için genellikle vurgu yoğunluğudur. Yüksek viskozite şekillendirmeyi güçleştirirken, düşük viskozite şekillendirme sırasında toz-bağlayıcı ayrışmasına ve ardından da çatlama ve çarpılmaya sebep olabilir.
Pek çok termoplastik bağlayıcının (mum-polimer sistemleri) artan sıcaklıkla azalan artan toz içeriği ile yükselen viskozitesi vardır. Bu nedenle, şekillendirme için hazırlanacak bir besleme stokunun uygulanacak şekillendirme teknolojisi için uygun olup olmadığının reolojik testler ile belirlenmesi gerekir.
Viskozite akışa karşı gösterilen direncin bir ölçüsüdür. Toz bağlayıcı karışımları için viskozite, toz miktarına bağlı olup besleme stokundaki katı yükleme ile ölçülür.
Karıştırma
Karıştırma; özel parçacık boyut dağılımı hazırlanması, sinterleme esnasında yeni alaşımların oluşturulması amacıyla tozların birleştirilmesi, sıkıştırma için yağlayıcıların eklenmesi ve şekillendirme için toz bağlayıcı karışımının hazırlanması için gereklidir. Tozların karıştırılmasının ana sebebi genel olarak taşıma esnasında titreşimler ile oluşan ayrışmanın engellenmesidir. Titreşim sonrasında tozlar boyutsal olarak ayrılır. Parçacık boyutunda olan bu tür ayrışma, sıkıştırma sinterlemede düzensizlikler yaratır.
Ayrışmanın üç nedeni olmasına rağmen (parçacık boyutu, yoğunluk ve şekildeki farklılıklar), boyut farkından ileri gelen ayrışma en baskın olanıdır.
Örneğin, küçük parçacıklar büyük parçacıklar arasındaki boşluklardan geçerse, toz kolayca ayrışacaktır. Boyut ayrışmasının bir sonucu, yoğunluk değişimi nedeniyle, genel görünür yoğunluğun noktadan noktaya azalmasıdır.
Düzensiz parçacık şekli boyuta bağlı ayrışmayı engelleyecektir. Aynı şekilde parçacık boyutunun yaklaşık olarak 100 µm’ nin altında olduğu tozlarda, parçacıklar arası sürtünmenin daha fazla olması nedeni ile boyuta bağlı ayrışma daha az olur. Taşımaya bağlı boyut ayrışmasının giderilmesinde karıştırma işlemi kullanılır.
Karıştırma işlemleri parçaların üretiminde yaygın bir sorun kaynağıdır. Karıştırmadaki değişkenler: malzeme, parçacık boyutu, karıştırıcı tipi, karıştırıcı boyutu, karıştırıcı içerisindeki tozun göreceli hacmi, karıştırma hızı, kesme ve karıştırma zamanıdır. Bunlara ek olarak nemlilik gibi çevresel faktörler de karıştırmayı etkiler. Bazı basit kurallar sorunları azaltır:
1- Taşıma sonrası kuru tozların yeniden harmanlanması
2- Kuru tozların titreştirilmemesi
3- Boyut ayrışmasının gerçekleşeceği durumlarda kuru tozun serbest düşüşle beslenmemesi
4- Toz-bağlayıcı karışımı için gereksiz kesmenin giderilmesi
Viskoz sıvı bağlayıcılar, parçacıklar arasında moleküler ölçekte dağılım için yüksek kesme kuvvetlerine ihtiyaç duymaktadır. Ergiyik bağlayıcıların tozlarla karıştırılması için kullanılan bileşik hazırlayıcıları parti tipi veya süreklidirler. Karıştırıcı, tozu ve polimeri ısıtırken yüksek darbeli kesme hareketleri uygular.
Karışım içerisindeki düzensizlikler iki ana şekilde oluşur. Bağlayıcının tozdan veya bağlayıcı içerisindeki farklı boyutlardaki tozların birbirinden ayrışması ve parçacıkların boyuta veya şekle veya yoğunluğa göre ayrılması düzensiz paketleme yoğunluğuna neden olur. Küçük veya düzensiz şekilli parçacıklar homojen yapı elde etmek için daha uzun karıştırma sürelerine ihtiyaç duyar ve karıştırma açısından özel sorunlar oluşturur. Küçük parçacıklar topaklaşarak homojen karışım için gerekli zamanın uzamasına neden olur.
Bazı durumlarda topaklanma hızı dağılımın karışım hızını dengeler ve karışım süresi ne olursa olsun karışım homojen olmaz. Parçacıklar üzerindeki polar molekül kaplamalar itici kuvvetler oluşturur ve böylelikle topaklanmayı ve parçacıklar arası sürtünmeyi azaltarak paketlemede iyileşme sağlar. Bu mikron altı parçacıklar açısından çok önemlidir.
Termoplastik bağlayıcılarda karıştırma, kesmenin baskın olduğu ara bir sıcaklıkta yapılır. Çok yüksek sıcaklıklarda yapılan karıştırma bağlayıcıyı bozar veya düşük bağlayıcı viskozitesi nedeni ile tozun ayrışmasına neden olur. İşlemin tekrarlanabilirliği için bileşim ve sıcaklık son derece iyi kontrol edilmelidir. Karıştırma esnasında oluşan homojensizlikler sonraki aşamalarda zorluklara neden olur. Karışımın her bir bölümü aynı toz miktarına sahip olmalı ve tozun parçacık boyut dağılımı da her bir bölümde aynı olmalıdır. Karışımın iyi olmadığı bir sistemin viskozitesi daha yüksek olur. Bu nedenle viskozite muhtemelen homojenliğin doğrudan en iyi ölçüsüdür. Örneğin ,enjeksiyon kalıplamada kullanılacak olan iyi karıştırılmış bir paslanmaz çelik besleme stoku; hacimce %67’si toz, karışım yoğunluğu 5,6 g/cm3 ,130 °C’ deki viskozite 87 Pa.s, oda sıcaklığı ham dayanımı 20 MPa’ dır.
Karışımın homojenliği, belirli noktalardan alınan yoğunluk, ısı kapasitesi, elektrik iletkenliği, viskozite ve hatta renk testleri kullanılarak bileşim farklılıklarının ölçümü ile belirlenir. Karışımın kalitesi geniş aralıkta alınmış numunelerin karıştırılması ile değerlendirilir.
Karıştırma esnasındaki eş zamanlı ayrışma ideal durumdan düşük kararlı-hal homojenliğine götürür. En yüksek homojenlik karışım oranının ayrışma oranına eşit olduğu durumlarda gerçekleşir
Granülasyon ve Peletleme
Her iki işlemin de amacı aynıdır; kalıplama makinesine doldurulacak karışımın kolaylıkla taşınabilmesi ve kalıplama işleminde artık, hurda ve hasarlı parçaların yeniden kullanılmasını sağlanmasıdır. Hurda malzeme, yolluk parçaları ve hatalı kalıplanmış parçaların yeniden kullanımı ekonomik avantaj sağlar.
Karıştırma sonrası hemen enjekte edilmeyecek besleme stokları karışımın daha homojen bir hale getirilmesi için iri katı parçalar haline getirilir, buna granülleme denir. TEK’ de besleme stokunun malzemenin granül hale getirilmesinin iki amacı vardır. Birincisi, besleme stokunun kalıplama makinesine kolayca taşıyabilecek kümelerin hazırlanmasıdır. İkincisi de hurda malzemenin tekrar kullanılabilmesidir.
Granülasyon; Düşük karışım homojenliği, düşük maliyet özelliklerinden dolayı yolluk ve dağıtıcılar için sıkça kullanılır. Peletleme; üniform biçim ve ölçü, ekstrüzyon için karışım homojenliği yüksek, yüksek maliyetli olduğu için ilk karışımlar için kullanılır.
Kalıplama ve Kalıplanabilirlik
TEK, yeterli bir sıcaklığa kadar ısıtılan besleme stoku içindeki bağlayıcının ergitildikten sonra kalıp boşluğu içerisine belli bir basınç altında doldurulması işlemidir. Kalıplama işleminde tozun homojen dağılması, hatasız ve boşluksuz bir parçanın elde edilmesi amaçlanmıştır. Bu nedenle ergimiş madde asgari zorlanma ile kalıbın içerisine akacak bir viskoziteye sahip olmalıdır.
TEK’ de parça şekillendirme için kullanılan cihazlar, plastik enjeksiyon kalıplamada kullanılan cihazlarla aynıdır. Çoğu kalıplama makinesi, ısıtılmış ve basınçlı bir silindirdeki besleme stokunun bir girişten geçerek kalıbı doldurması şeklinde çalışır. Kalıbı doldurmak için gerekli basınç bir piston veya ileri-geri hareketli vida ile sağlanır.
Kalıplama makinesi tekrarlayan döngüler halinde çalışır ve her bir döngüde bir veya daha fazla parça imal edilir.
Her döngü kalıbın kapatılması ile başlar, enjeksiyon ünitesi ile ileri doğru hareket eder, vida sıcak besleme stoku ile kalıbı doldurmak üzere ileriye doğru hareket eder ve bağlayıcı girişte donuncaya kadar basınç muhafaza edilir.
Soğutma devam ederken, giriş donduğu için vida silindirdeki karışımı karıştırarak veya plastikleştirerek bir sonraki besleme stoku yüklemesini hazırlar. Sonra parça sertleştiğinde kalıp açılır, parça çıkartılır ve döngü tekrar eder.
Kalıp boşluğu içerisine doldurulan karışım yüksek basınçta sıkıştırılarak yoğunluk ve homojenizasyon sağlar. Sağlanan bu yoğunluğun ve homojenizasyonun bozulmaması için karışım tam olarak katılaşıncaya kadar sıkıştırma basıncı uygulanmaya devam eder. Tutma aşaması olarak bilinen bu aşamada katılaşma tam olarak gerçekleştirilir. Katılaşma sonrasında tüm basınç kademeli olarak kaldırılır. Kalıplama işleminde kalıplama sıcaklığı ve basıncı işlem başarısını doğrudan etkileyen parametrelerdir.
Kalıplama esnasındaki sıcaklık ve basıncın birbiri ile uyum içerisinde olması gerekir. Yüksek kalıplama sıcaklıkları ve basınçları parçalarda çapaklanma ve kalıp duvarlarında yapışma oluştururken, düşük sıcaklık ve basınç değerleri parçalarda boşluk meydana getirir.
Enjeksiyon sırasında sürtünme besleme stokuna, kayma hızına ve sıcaklığa bağlıdır. Basılan karışımın cinsine, parçanın geometrisine, giriş ve yollukların durumuna bağlı olarak, enjeksiyon nozulu ve kalıpta meydana gelen akış direnci belirlenebilmektedir. Karışımın nozul ve kalıp içerisinde akışında karşılaştığı direnç karışımın malzemesine, enjeksiyon hızına, kalıp içi geometriye ve kalıp içi boşluğa dolan karışım miktarına bağlı olarak değişir.
Kalıplama besleme stokunun aynı anda ısıtılmasını ve sıkıştırılmasını gerektirir. Kalıplama makinesi besleme stokunu 130 °C ile 190 °C arasında ısıtır. Kalıplama, ergimiş besleme stoku kalıba enjekte edilirken çok kısa sürede gerçekleşir. Besleme stoku silindirin sonundaki memeden çıkar, yolluk, dağıtıcı ve giriş kanalından geçerek kalıp boşluğuna akar. Parçalar kalıp ayrılma çizgisinde yerleştirilmişlerdir ve kalıp açılarak dışarı alınır.
Besleme stoku soğuk kalıpta akarken soğur ve viskozitesi artar. Kalıp boşluğu doldukça akışa karşı direnç artar, bu da basınç yükselmesine neden olur. Şekilde ayrıca kalıpta besleme stokunun sıkıştırmada kullanılan vidanın konumu da görülmektedir. En yüksek kalıplama basıncı kalıp geometrisi, bağlayıcı ve toz özelliğine bağlı olup, en fazla 60 MPa olabilir.
Kalıp ve Kalıplama Makineleri
TEK’ de son ürün ölçülerinden daha büyük bir kalıp oluşturulur. Bu şekil defalarca çoğaltıldığından kalıp malzemesi sert, dayanıklı ve işlenebilir olmalıdır. Sert kalıpların imalatı pahalıdır, ancak aşınma direnci yüksek olduğundan fazla miktardaki üretimler için tercih edilirler. TEK’ de kalıp ömrü 300.000 parçayı geçer, hatta bazen bunun on kat fazlası dahi gerçekleşebilir.
Kalıp seti, kalıp boşluğu ve bu boşluğa dolum yapılacak yolu içerir. Kalıp boşluğunun boyutu, parçada sinterleme sırasında meydana gelecek çekme de hesaba katılarak büyük tutulur. Kalıp boşluğunun etrafında kalıbı açma-kapama, parçayı çıkartma, kalıp bölümlerini ayarlama, hareketli ilave parçalar, parçayı soğutma ve yolluk, dağıtıcı ve girişi sağlayan mekanizmalar vardır. Kalıp seti tasarımlarında dikkat edilmesi gereken en önemli husus parçadaki çekmedir. Parçanın ölçülerindeki değişimin parçanın orijinal ölçülerine oranına çekme faktörü denir.
TEK’in önemli bir üstünlüğü, diğer alternatif teknikler ile üretilemeyecek kadar karmaşık şekilli parçaları üretebilmesidir. Bu nedenle karmaşık kalıp tasarımı TEK’e özgü bir husustur.
Kalıp malzemesinin dayanımı ile mukayese edildiğinde kalıplama basıncı çok düşük olduğundan, pek çok ilave parça, kızak ve diğer özellikler ilave edilerek kalıbın karmaşıklığı arttırılabilir. Kalıp boşluğunun eş parçaları kapanırken, kızak direk oluşturmak için hareketlendirilir.
Direk etrafında dolum yaptıktan sonra kalıp boşluğu açılırken kızak yukarı doğru hareket eder ve böylece kalıp ayrılma çizgisine paralel delik oluşur.
Bu tür hareketler parçanın bütün yönlerinde detay oluşturur ve üç boyutlu karmaşıklığa fırsat verir. Kalıbın ömrü kalıp malzemesinin dayanabileceğinden daha düşük basınç uygulamasına bağlıdır.
TEK’te kullanılan enjeksiyon makineleri birçok bakımdan farklı çeşitlerdedir. Fakat pratikte en çok kullanılan üç temel tip enjeksiyon makinesi mevcuttur. Bunlar; hidrolik, pnömatik ve karşılıklı hareket eden vidalı enjeksiyon makineleridir. Bu makineler genel amaçlı enjeksiyon işlemlerinde kullanılmakla birlikte her birinin üstünlük ve kısıtlamaları mevcuttur. Aşağıdaki şekilde basit bir vidalı enjeksiyon makinesinin çalışma prensibi görülmektedir.
Bağlayıcı Giderme
Bağlayıcı giderme, toza çeşitli sebeplerle katılan bağlayıcıların sinterleme öncesi farklı yöntemlerle uzaklaştırılmasıdır. Bağlayıcının ön-üründen çıkarılması için ısıtma, kimyasal çözücülerde çözme, besleme stokunda kullanılan tozdan daha küçük tane boylu tozlar içine gömerek ısıtma (kılcal çekim ile bağlayıcıyı ayrıştırma: fitilleme) ve suda çözme gibi işlemler tek başına veya ardışık olarak uygulanabilmektedir. Tüm işlemler kendi içinde bazı zorluklar içermekte ve üretilen ön-ürünün firesine yol açabilmektedir. Ön-ürünün ısıtılması, bağlayıcının ergitilip, bozundurulup veya buharlaştırılması ile uzaklaştırılmasını sonuçlanmaktadır.
Bağlayıcı ısıtılınca yumuşar ve bu nedenle yerçekimi ile içerideki buhar keselerinde oluşan gerilmelere karşı koyamaz. Bundan dolayı toz taneleri arasında sürtünmeye gerek duyulur. Parçayı bozmadan ve kirletmeden, gözeneklerden bağlayıcıyı sıvı ve buhar halinde çıkartmak gerekir. Bağlayıcı uzaklaştırmanın en uygun ve kolay yolu çok bileşenli bağlayıcı formülü kullanmaktır. Bağlayıcı bileşenlerinden ana bağlayıcı uzaklaştırılırken tozları bir arada tutacak olan iskelet bağlayıcı parçanın bozulmasını önleyecektir. Çözücü ve ısıl olmak üzere iki tip bağlayıcı giderme yöntemi mevcuttur. Çözücü bağlayıcı giderme; daldırma, süper kritik çözücü ve katalitik olmak üzere üç çeşittir. Isıl bağlayıcı giderme de; yayınma, geçişme, kılcal çekim olmak üzere üç çeşittir. Sistemde kullanılan bağlayıcılara göre bağlayıcı giderme çeşitleri tek başına veya ardışık olarak uygulanabilir. Her yöntemin kendine göre avantaj ve dezavantajları mevcuttur.
Isıl bağlayıcı giderme metotları uygulamada sıkça kullanılan metotlardandır. Bunlar da kılcal çekim kuvvetleri ile bağlayıcının sıvı fazdan alınması, parçanın bir toz kümesi içerisine gömülmesi ve daha sonra uygulanan ısı ile parça içerisindeki bağlayıcının belli bir akışkanlığa ulaşıp toz kümesi tarafından emilerek çekilmesidir.
Bağlayıcının ısı etkisi ile gaz fazında uzaklaştırılması ise bağlayıcının okside edilmesi, dipolarize olması veya zincir bağının kopması ile buharlaşması şeklinde olur. Eğer basınç düşük ise yayınma ile, eğer boşluklar büyük ve basınç yüksek ise bağlayıcının alınması geçişme seklinde olur. Bu yöntemler uygulamada birlikte kullanıldığında işlem hızlanır.
Isıtma hızlarının düşük tutulması, bitmiş numunede kalıcı kusurların oluşumuna engel olur. Isıtma hızının özellikle bağlayıcıların bozulma sıcaklığına kadar 1 0 C/dk’ dan daha fazla olması halinde çökme, kabarma ve çatlak gibi kusurlar meydana gelir.
Hızlı bağlayıcı giderme için kullanılan süperkritik çözücü yönteminde, çözücü yüksek basınç ve sıcaklık uygulandığında sıvı- gaz kritik noktasını geçerek süperkritik bölgeye geçer. Bu bölgede çözücünün buhar ve sıvı fazları farksız olur.
Böylece sıvıdan buhara geçme ve hacim değişimi problemi kalmadan bağlayıcı bünyeden çözücü yardımıyla çözülerek uzaklaştırılır. Diğer bir çözücü yardımıyla bağlayıcı giderme metodu ise katalist metodudur.
Poliasetal bağlayıcı içeren bir parçanın asidik gaz atmosferinde dipolarize edilerek buharlaştırılması ve formaldehit olarak bünyeden uzaklaştırılmasıdır. Bağlayıcı doğrudan katı halden gaz fazına geçerek uzaklaşır.
Çözücü yardımıyla bağlayıcı giderme yöntemi ancak belirli bazı bağlayıcı sistemlere uygulanabilmektedir. Bu bağlayıcının trikloretan gibi uygun bir çözücü ile çözülerek uzaklaştırılmasıdır. Isıtma, son aşama olarak bağlayıcının ayrışma işleminin buharlaştırılarak tamamlanması için gereklidir. Su bazlı bağlayıcıların önüründen yalnızca su ile uzaklaştırılabilmeleri önemli bir avantaj oluşturmaktadır. Bu işlemin gerek düşük maliyetli olması, gerekse ön-ürünün bağlayıcı çıkarma işleminden daha az etkilenerek şeklinin bozulmaması TEK işlemlerinde dikkatleri su bazlı bağlayıcılara çekmektedir.
Burada uygulama ön-ürünü belirli sıcaklık derecesindeki suda tutmaktan ibarettir. Reometre deneylerinde iyi kılcal akış gösteren örneklerin 30 ºC suda sekiz saat bekletmekle bağlayıcının ön-ürünün şekli bozulmadan ayrıldığı gözlenmiştir. Bağlayıcının çıkarılması sırasında kompaktın dayanımı önemli oranda azalır, bu yüzden bağlayıcı çıkarma işlemine tabi tutulmuş parça sinterleme aşamasına dikkatli bir şekilde taşınmalıdır.
Bağlayıcı giderme aşamasında parçadaki gözenek yapısı, bağlayıcıların kimyasal özellikleri, bağlayıcı giderme koşulları ve işlem süresi bağlayıcı giderme aşamasının başarısını belirler. Bağlayıcı gidermede en uygun ve en kolay çözüm çok bileşenli bağlayıcı formülleri kullanmaktır. Bağlayıcı bileşenlerinden biri uzaklaşırken diğeri partikülleri bir arada tutar.