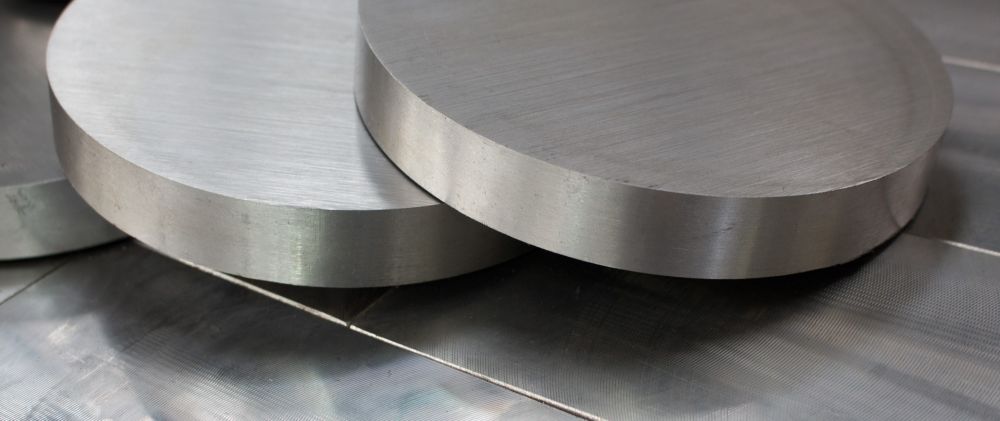
İleri bir imalat yöntemi olan toz metalurjisi, teknolojik malzemelerin üretilmesine çok uygun, küçük parçaların çok sayıda ve ekonomik üretimini sağlayan bir yöntemdir. Toz metalurjisi, son şekle yakın üretim süreçleri olarak sinterleme, sıcak izostatik presleme, toz metal enjeksiyonu, nano-parçacık teknikleri, mekanik alaşımlama gibi konularla sürekli büyüyen bir pazara sahip olan ileri teknolojilerden biridir. Çok karmaşık şekilli ürünlerin daha kolay bir şekilde elde edilmesinde uygulanan bir teknolojidir.
Toz metalurjisi, metalik ve metalik olmayan farklı malzemeler kullanılmasına olanak veren bir yöntemdir. Son ürünün metalurjik içeriği ve yoğunluğu kolayca kontrol edilmekte ve toz metalurjisi günümüz dizayn mühendislerinin gün geçtikçe dikkatini çekmektedir. Üretim hızı çok yüksektir, tozun kalıba doldurulması ve toz karışımının şekillendirilmesi bir saniyeden kısa sürede gerçekleşmektedir. İşlem esnasında meydana gelen toz kaybı sinterleme sırasında oluşan hatalı parçalarla oluşan kayıplar dışında oldukça düşüktür. Bu nedenle toz metalurjisinin maliyet verimliliği fazlasıyla yüksektir. Sinterlenmiş parçaların yüzeyleri oldukça düzgündür ve ikincil işlemlere gerek duyulmaz. Bu özellik tungsten karbür, titanyum karbür ve elmas matrisler benzeri işlenmesi zor malzemelerin işlenmesine imkan verir. Toz metalurjisi ile üretilen parçaların gözeneklilik miktarı kolaylıkla kontrol edilmekte ve filtre parçaları, kendinden yağlamalı burçlar gibi özel parçalar üretilebilmektedir. Ayrıca küçük, karmaşık şekilli parçalar da bu yöntemle basit bir şekilde üretilmektedir.
Toz metalurjisinin birçok üstünlüğü yanında bazı eksiklikleri de mevcuttur. Yüksek mukavemetli, aşınma direnci yüksek çelikler kalıp üretiminde kullanıldığından, toz metalurjisinde kullanılan kalıplar oldukça maliyetlidir. Toz metalurjisi yönteminin döküm, dövme gibi geleneksel yöntemlere alternatif olması, en az 15000 parça gibi yüksek üretim miktarları ile mümkündür. Az miktarda parça üretimi bu yöntemi ekonomik olmaktan çıkarır. Azami toz metalurjik parça boyutu presleme sırasında gerekli presleme basıncı nedeniyle sınırlanmakta, bundan dolayı küçük boyutlu parçalar üretilmektedir. Dizayn sınırlamaları da toz metalurji üretimini etkilemekte, üretilen parçalarda kalınlık/genişlik oranı 3:1 oranını geçmemektedir. Bazı toz karışımları kullanılarak üretilen sinterlenmiş parçalarda, kırılganlık problemi oluşmakta, bu problem parçaların tekrar preslenmesi ile asgari düzeye indirilmektedir.
Toz metalurjik ürünler değişik üretim metodlarıyla imal edilmekle birlikte, toz metalurjisi yöntemi; toz üretimi, tozun yağlayıcı ve karıştırıcı maddeler ile birlikte harmanlanması, soğuk presleme ve sonrasında yapılan gaz giderme işlemi, sinterleme veya sıcak presleme ve son olarak ikincil işlemler sıralaması ile gerçekleştirilmektedir.
Önerilen Makale: Çelik boru malzemeler ve uygulamaları hakkında detaylı bilgi almak için
çelik sanayi boruları nedir sayfamızı ziyaret etmenizi tavsiye ederiz.
Toz Üretim Yöntemleri
Toz metalurjik tozların üretiminde atomizasyon, mekanik alaşımlama, öğütme, elektroliz ve kimyasal indirgenme yöntemleri kullanılmaktadır. Endüstride kullanılan tozların % 60’dan fazlası atomizasyon yöntemi ile üretilmektedir.
Atomizasyon ile toz üretimi, bir indüksiyon fırınında hazırlanan ergiyik metalin bir veya daha fazla nozul vasıtasıyla sıvı metal huzmesi halinde bir hazneye akıtılması ve bu huzme üzerine basınçlı gaz veya su jeti uygulaması ile toz üretimi aşamalarından oluşmaktadır. Elde edilen toz malzeme haznenin altında toplanmaktadır. Genel olarak su ve gaz atomizasyon yöntemi olarak iki ana gruba ayrılır.
Gaz atomizasyon yönteminde gaz olarak su buharı, hava, hidrojen, azot ve argon gazları kullanılmaktadır. Ortamın inert olması sebebiyle üretilen tozun kirlilik içermemesi, tozun homojen ve küresel geometriye sahip olması bu yöntemin sağladığı üstünlüklerdir. Su atomizasyon yönteminde, ergiyik metal üzerine su jeti uygulanması ile toz malzeme üretilmektedir. Suyun soğutma hızının gaza nazaran yüksek olması, toz malzemede kimyasal ayrışmanın daha az, tozların şeklinin daha düzensiz, toz yüzeyinin daha kaba ve oksitli olmasına neden olmaktadır.
Mekanik alaşımlama, bilye ve elemental toz karışımı kullanılarak bir öğütücü veya yüksek enerji değirmeninde mikro alaşımlı kompozit toz üretme yöntemidir. Mekanik alaşımlama esnasında, metal tozunun karışma, soğuk kaynak, kırılma ve tekrar kaynak gibi işlemlere tekrar tekrar maruz kalması, malzeme içerisindeki inklüzyonların homojen dağılımını ve sonuç olarak homojen malzeme eldesini sağlamaktadır.
Öğütme işleminde, metallerarası bileşikler, demir alaşımları, demir-krom, demir-silisyum v.b. gibi kırılgan malzemeler mekanik olarak bilyalı değirmenlerde öğütülürler. Fakat öğütme işlemi birçok sünek metal için uygun değildir; çünkü bu metaller kolayca kırılmazlar. Sünek tanecikler kırılma yerine birbirleri ile soğuk olarak kaynaklanır ve daha büyük tanecik oluştururlar.
Elektroliz, elektrolitin kimyasal bileşimi ve mukavemeti, sıcaklık, akım yoğunluğu gibi şartları uygunca seçilerek, birçok metalin sünger veya toz durumunda katot üzerinde biriktirilmesi işlemidir. Daha sonraki işlemler olarak, yıkama, kurutma, indirgeme, tavlama ve öğütme gerekli olabilir. Bu yöntemle üretilen metallerin başında bakır gelir, aynı zamanda krom ve magnezyum da bu yöntemle üretilebilir.
Kimyasal indirgenme, en çok demir tozlarının üretiminde kullanılmaktadır. Bu yöntemde seçilen cevher öğütülür, kokla karıştırılır, karışım indirgemenin oluştuğu sürekli fırından geçirilir ve kek şeklinde sünger demir elde edilir. Sünger demir daha sonra öğütülür, metalik olmayan malzemelerden ayrılır ve elenir. Tozların saflığı ham malzemelere bağlıdır.
Presleme Öncesi İşlemler
Metal tozlarının presleme işlemi ile şekillendirilmesini kolaylaştırmak ve tozlara istenen özellikleri kazandırmak için çeşitli ön işlemler gereklidir. Bu işlemler; tavlama, tozun karıştırılması, toz boyutunun azaltılması, toz granülasyonu (topaklaştırma) ve harmanlamadır.
Tavlama işlemi toz yüzeyinde bulunan oksijen, hidrojen ve azotun yüzeyden uzaklaştırılması ve tozun yumuşatılarak daha kolay preslenmesi için yapılır. Bu işlem için atmosfer korumalı veya vakum fırını kullanılmakta ve sinterleme etkisini azaltmak için tavlama sıcaklığı düşük tutulmaktadır.
Önceden çeşitli yöntemlerle hazırlanmış alaşımlı veya saf metal tozları parçada istenen bileşimi sağlayacak oranlarda bağlayıcı ve yağlayıcı gibi katkı maddeleri ile birlikte karıştırıcılarda homojen olarak karıştırılır. Karıştırıcı tipi, geometrisi, hacmi ve iç yüzeyinin alanı, karıştırma öncesi ve sonrası toz malzemesinin hacmi, karışımı oluşturan tozların karakteristik özellikleri, besleme ve boşaltma aletlerinin tipi, konumu ve sayısı, karıştırma hızı, süresi, sıcaklığı, ortamı ile nem gibi birçok değişken karıştırma işlemini etkilemektedir. Karıştırmanın verimliliği, toz karışımının karıştırıcı hacminin % 50-60’ını oluşturması ile maksimum seviyeye çıkmaktadır. Optimum karıştırma süresi 5-30 dakika olmakla birlikte, kullanılan malzeme ve istenen özelliklere göre değişim göstermektedir.
Boyut küçültme işlemleri çoğunlukla dar partikül boyut dağılımlarında yüzey alanını arttırmak amacıyla uygulanmakta ve homojen olmayan karışımlarda dağılım ve kimyasal reaksiyon oranının iyileştirilmesi hedeflenmektedir.
Preslemede kullanılacak metal tozları gerek presleme kolaylığı, gerekse parça dayanımı açısından aynı metal tozundan farklı partikül boyutlarında belli oranlarda biraraya getirilerek bir harman elde edilir. Bu işlem mekanik alaşımlama amacıyla farklı malzeme tozlarının da istenen oranlarda karıştırılması ile yapılabilir.
Tungsten, molibden ve WC-Co gibi düzgün sert tozların preslenmesi ve presleme sonrası kullanımı oldukça güçtür. Bu nedenle, bu tozlara granülasyon yöntemi uygulanarak büyük topaklar oluşturulur. Toz-organik bulamacı devamlı karıştırıcılarda karıştırılmakta ve oluşan topaklara ısı uygulanarak uçucu ajan ortamdan uzaklaştırılmaktadır. Sonuçta sert, sıkı paketlenmiş topaklar elde edilir.
Partiküllerin bir araya gelerek toplanmaları olarak tanımlanabilen paketlenme, presleme ve sinterleme davranışlarını etkilemesi açısından önemlidir. Özellikle presleme verimliliği partikül paketlenmesine bağlıdır.
Harmalamanın Etkisi
Koordinasyon sayısı veya bir partikülün temas nokta sayısı, paketlenme esnasında partiküllerin (paketlenme faktörü) geometrik düzenlenmesini tanımlayan önemli bir parametredir. Tek boyutlu partiküllerin paketlenmesi ile: (1) koordinasyon sayısı kesin aralıkta düzenlenmekte, (2) Paketleme metodu ile ortalama koordinasyon sayısı değişmekte, (3) Genellikle, yoğun paketlenmede yüksek koordinasyon sayısına ulaşılmaktadır.
Kepler 1611 yılında tek boyutlu partiküllerin hücrenin en fazla π/√18=≈0,740480 yani %74’lük kısmının doldurulabileceğini savunmuş ve bu teori Hales tarafından 1998 yılında kanıtlanmıştır. Farklı boyutlu partiküllerin paketlenmesinde ise partiküller arasında kalan boşluklar daha küçük boyutlu partiküller ile doldurulmakta ve paketlenme faktörü artmaktadır. Her defasında bir önceki partikülden daha küçük çapa sahip partikül eklendiğinde, boşluklar sonradan eklenen partiküller tarafından doldurulmakta ve teorik boşluk değeri azalmaktadır. Pratikte ise bu yüksek yoğunluklara oluşmak oldukça güçtür.
Farklı boyutlarda partiküllerin paketlenmesinde en önemli koşul, boşlukların ikinci bileşenin ilavesi ile tüm hacimde bir genleşme oluşmadan doldurulmasıdır. Partiküllerin tane boyutlarının birbirlerine yakın olması durumunda, temas noktalarında diğer partikülü temas noktalarından iterek hacimsel genleşme meydana gelerek yoğunluk değerinin düşmesine sebebiyet verir. Buna engel olmak için, Furnas bağıntısında faydanılabilir. Bu bağıntıya göre, maksimum paketlenme bileşiminde büyük partiküllerin hacim yüzdesi küçük partiküllerin hacim yüzdesinden daha büyüktür. Minimum spesifik hacim (maksimum paketlenme) doyma noktası olarak adlandırılır. Belli bir bileşim sınırına kadar büyük partiküllerin % miktarı arttığında paketlenme yoğunluğu artar.
Pinson, Zou, Yu, Zulli ve McCarthy yaptıkları çalışmada, farklı boyutlara sahip partiküllerin farklı hacim oranlarında porozitenin değişimine değinmişlerdir. İlk karışımda tek tip partiküller kullanıldığında en yüksek porozitenin oluştuğu, yapı içerisinde farklı boyutlarda partiküllerin kullanımı ile porozitenin azaldığı net olarak gösterilmiştir. Paketlenme içerisinde büyük partikül miktarının artması ile porozite azalmış, diğer bir anlamda daha yoğun bir yapı elde edilmiştir.
Presleme
Toz metalurjisinde presleme aşaması en önemli işlemi oluşturmaktadır. Preslemede ulaşılan yoğunluk değerleri toz metalurjisi yöntemi ile imal edilen parçaların mekanik özelliklerini birinci dereceden etkiler. Presleme ile imal edilecek parçanın istenen düzeyde şekil ve boyutlara, yoğunluğa ve mekanik dayanıma sahip olması amaçlanır. Metal tozlarının preslenmesi sırasında, presleme koşullarına ve toz malzemesinin özelliklerine bağlı üç önemli olay gerçekleşir. Bu olaylar:
a) Paketlenme (Toz tanelerinin düzen değiştirmesi, köprülerin çökmesi, boşlukların dolması) : Presleme amacıyla tozun kalıba doldurulması esnasında, toz taneleri arasında köprü oluşur. Özellikle toz karışımlarının harmanlanması hem presleme basıncının ve preslenmiş yoğunluğun artmasını sağlar.
b) Elastik-plastik deformasyon (Kontakt deformasyonu, toz tane yüzey yuvarlaklığının düzelmesi, oksitlerin kırılması, mekanik zincirleme): Tanelerin temas noktaları artan basınçla oluşan elastik-plastik deformasyon sonucu büyür. Bu esnada tane yüzeylerindeki oksitler kırılarak daha iyi zincirleme şeklinde temas yüzeyleri oluşur.
c) Sünek tozlarda soğuk sertleşme, kırılgan tozlarda kırılma: Plastik deformasyon gösteren tozlarda ilk olarak elastik deformasyonla sıkışan taneler basınçla toz malzemesinin akma sınırına ulaştığında taneler şekil değiştirir, boşluklar azalır ve relatif yoğunluk artar. Presleme işleminde kaba metal tozlarında ulaşılan yoğunluk değeri ince tozlara nazaran daha yüksektir.
Toz malzemelerin preslenmesi işleminde gerçekleştirilmek istenen amaçlar;
- Metal tozunu istenilen boyutta kompakt hale getirmek
- Sinterleme sonrası elde edilen son ürünlerde herhangi bir boyutsal değişikliğin oluşmaması
- İstenilen gözenek tipi ve oranının elde edilmesi
- Preslemeden sonra yapılacak işlemler için gerekli mukavemeti sağlamaktır.
Presleme işlemi genel olarak;.
- İletim için gerekli miktarda toz karışımının kalıba doldurulması,
- İstenen preslenmiş (green) yoğunluk ve mukavemete ulaşmak için presleme basıncının uygulanması,
- Üst zımbanın numuneden uzaklaştırılması (Preslenmiş numunenin zarar görmemesi için dikkatli davranılır),
- Numunenin kalıp içerisinden çıkartılması olmak üzere 4 ana bölümden oluşmaktadır.
Presleme Yöntemleri
Presleme yöntemlerini soğuk ve sıcak presleme olmak üzere iki gruba ayırmak mümkündür. Bu iki yöntem arasındaki fark, sıcaklığın uygulanış zamanıdır. Soğuk preslemede, preslemeden sonra sıcaklık (sinterleme) uygulanırken, sıcak preslemede presleme basıncı ve sıcaklık birlikte uygulanmaktadır.
Soğuk Presleme Yöntemleri
Soğuk presleme yöntemlerinde malzemeler herhangi bir ısıl işlem uygulanmadan sadece presleme basıncı uygulanarak şekillendirilir.
Tek Yönlü Presleme
Tek yönlü presleme işleminde presleme kuvveti tek yönlü uygulanır. Presleme basıncı arttıkça, paketlenme artmakta, gözeneklilik miktarı azalmaktadır. Yüksek presleme basıncında partiküller birbirleri ile soğuk kaynamakta ve deforme olmakta, preslenmiş numunenin mukavemeti artmaktadır. İşlem esnasında kalıp duvarları ile toz karışımı arasındaki sürtünmenin azaltılması amacıyla yağlayıcılar kullanılmaktadır. Presleme işlemi sonrasında numune kalıp içerisinden çıkartılır.
Soğuk İzostatik Presleme
Soğuk izostatik presleme işleminde kauçuk veya plastikten yapılmış esnek bir kalıp toz karışımı ile doldurulur ve yağ, su gibi bir sıvı vasıtasıyla presleme kuvveti kalıbın bütün kısımlarına eşit miktarda uygulanır. Presleme basıncı değerleri 1400 MPa’a kadar çıkmakla birlikte, bu işlem genellikle 380 MPa’dan daha düşük presleme basıncınında uygulanır.
Soğuk izostatik presleme işleminin, preslenmiş numunede homojen ve yüksek yoğunluk (tek yönlü preslemeye nazaran % 5-10 daha fazla), yüksek mukavemet, azaltılmış iç gerilimler, ilave malzeme kullanılmaksızın presleme yapılması, kompleks parçaların üretimi, düşük malzeme ve ikinci işlem maliyeti gibi üstünlükleri vardır. Bunun yanında, preslenmiş numunenin boyutsal kararlılığı, yüzey kalitesi, kalıp ömrü ve üretim hızı tek eksenli preslemeye göre daha kötüdür.
Sıcak Presleme Yöntemleri
Bu yöntemlerde sıcaklık ve basınç birlikte uygulanmaktadır. Şekillendirme ve sinterleme işlemleri aynı anda yapıldığı için, yüksek yoğunluk ve hızlı üretim sağlanır. Bu yöntemde soğuk preslemeye göre daha yüksek mukavemet, sertlik, yoğunluk yanında numunede gaz miktarı ve büzülmenin daha az olması gibi üstünlüklere sahiptir.
Sıcak Presleme
Sıcak presleme, sıcak ekstrüzyon ve sıcak dövmeye göre daha sınırlı uygulanan bir yöntemdir. Genellikle seramik ve sert metal tozlarının yoğunlaştırılmasında tercih edilir.
Sıcak İzostatik Presleme
Sıcak izostatik presleme içerisinde ısıtıcı bulunan yüksek basınç kabı ve gövdeden oluşan tesisat içerisinde gerçekleştirilir. Toz karışımı ilk olarak kalıp içerisine doldurulur ve vakumlama işlemi uygulanır. Daha sonra kalıba her yönden eşit miktarda basınç ile sıcaklık uygulanır ve son ürün elde edilir. Yöntemin en önemli üstünlüğü, üç boyutlu ve homojen yüksek yoğunluk sağlamasıdır. İzostatik presleme için genellikle 100 MPa basınçlara kadar argon gazı kullanılır. İzostatik preslerin dizaynında temel problem, içine toz doldurulmuş kalıbın prese kolay ve hızlı şekilde boşaltma yapamamasıdır.
Sinterleme
Sinterleme, preslenmiş parçaların temel bileşeninin ergime derecesi altındaki bir sıcaklıkta koruyucu atmosfer altında uygulanması, parçada bulunan gözenekli yapının ortadan kaldırılması ile mukavemet ve sertlik kazandırma işlemidir. Mikroskobik ölçekte incelendiğinde, partiküllerin temas noktalarında boyun oluşumu ve bu oluşumun büyüdüğü gözlenir. Sinterleme işleminde itici güç tozun yüzey enerjisinin azalmasıdır. İtici güç bileşenlerden birinin ergime derecesinin üstünde sinterleme sıcaklığı uygulanması ile artmaktadır. Sinterleme işlemi malzeme taşınımı (difüzyon) ile gerçekleşir. Malzeme taşınımı; tane sınırları, yüzey ve malzeme hatalarından tane difüzyonu, tane sınırlarından sınır difüzyonu, malzeme yüzeyinden yüzey difüzyonu ve malzeme yüzeyinden gaz fazı taşınımı olmak üzere altı değişik şekilde gerçekleşmektedir.
Preslenmiş parçaların sinterlenebilirliğini ve sinterlenmiş mikroyapılarını etkileyen değişkenler malzeme değişkenleri ve proses değişkenleri olmak üzere iki kategoriye ayrılır. Malzeme değişkenleri, tozun kimyasal bileşimi, tozun boyutu ve boyut dağılımı, tozun şekli ve tozun topaklaşma derecesi gibi değişkenlerden oluşur ve tozun preslenebilme ile sinterlenme kabiliyeti etkiler. Bilhassa, iki tip toz içeren preslenmiş parçalarda toz karışımının homojenliği birincil öneme sahiptir. Proses değişkenlerinin çoğunluğunu ise, sinterleme sıcaklığı, zamanı, atmosferi, basıncı, ısıtma ve soğutma hızı gibi termodinamik değişkenler oluşturur.
Sinterleme işleminde ilk olarak, preslenmiş parça sinterleme fırınına yavaşça yerleştirilir. Sinterleme fırını içerisinde sıcaklık, sinterleme sıcaklığına ulaşana kadar ön ısıtma bölgesinde yavaşça artar. Parça fırın içerisinde ilerledikçe, ön ısıtma zonunda, parça içerisindeki bağlayıcı malzemeler buharlaşır, hareketli gaz çıkışı ile uzaklaştırılır. Sıcak sinterleme bölgesinde, toz taneleri arasında metalurjik bağlar oluşur ve parça soğutma bölgesinden fırının dışına alınır.
Sinterleme işlemi genel olarak katı faz ve sıvı faz sinterlemesi olarak ikiye ayrılır. Tozu oluşturan malzemelerin ergime sıcaklıkları birbirinden farklıdır. Sinterleme sıcaklığı ergime sıcaklığı en düşük olan toz bileşiminin altında ise taneler birbirleri ile katı fazda bağlanır ve katı faz sinterlemesi gerçekleşir. Katı faz sinterlemesi işlemi; Toz partiküllerinin arasında boyun formlarının oluşumu, gözenek geometrisinin değişmesi ve malzemenin büzülmesi, tane büyümesi ile gözeneklerin izolasyonu ve artık porozitenin ortadan kalkması olarak üç kademede gerçekleşmektedir. Bu üç kademe esnasında porozitenin azalması, numune yoğunluğunun artmasını sağlamaktadır.
Eğer sinterleme sıcaklığı, tozu oluşturan bileşenlerden birinin ergime sıcaklığı üzerinde seçilirse bu durumda sıvı faz sinterlemesi söz konusudur. Sıvı faz sinterlemesinde ergiyen bileşen, katı halde bulunan tanelerin yüzeyini ıslatarak bağlanmayı sağlar. Ergiyen faz gözenekleri doldurarak veya sıvı-katı hareketi ile gözenek miktarını en aza indirmektedir. Sonuçta çok daha yüksek yoğunlukta sinterleme gerçekleşir.
İkincil İşlemler
İkincil işlemler sinterleme işleminden hemen sonra uygulamaya konmaktadır. Bu işlemler, ikinci presleme, yağ emdirme, yüzey sertleştirme ve temperleme, yüzey kaplama, talaşlı imalat, çapak alma, infiltrasyon gibi işlemlerden oluşur.
İstenilen mekanik ve manyetik özelliklerin sağlanmasında gerekli olan parça yoğunluğunu elde etmek için bir gözenek azaltma işlemi olan ikinci presleme kullanılır. Preslenmiş parçanın 700-800°C arasında ön sinterlenmesi ile yağlayıcılar yanar ve yeniden kristalleşme meydana gelir. İç gerilmeler ve pekleşme kaldırıldığından malzeme sünekliğini tekrar kazanır. İkinci preslemeden sonra parçalar ikinci defa sinterlenir.
Yağ emdirme yöntemi, opsiyonel bir uygulamadır. % 25-30 oranında gözenek içeren parçalar içerisine bu gözenekleri dolduracak şekilde yağ emdirilir. İlk olarak parça içerisindeki hava vakumla ortamdan alınır, yağ emdirilir ve vakum kaldırılır. Sonuç olarak mikrogözeneklerine yağ emdirilmiş parça elde edilir. Bu yöntemle üretilen en yaygın parçalar kendinden yağlamalı burçlar olarak bilinen sinter burçlardır.
Sinterlenmiş parçaların yüzeyi elektrokaplama, galvanizleme ve kimyasal buhar biriktirme benzeri işlemlerle kaplanabilir. Elektrokaplama işlemi esnasında elektrolit korozyon problemi yaşamamak için emdirme işlemi yapılır. Buhar biriktirme ise takımlarda aşınma dayanımını arttırmak için uygulanır.
Sinterlenmiş parçaların üretilmesindeki en önemli çekicilik karmaşık şekiller ve dar toleransa sahip parçaların üretilebilmesi olmasına rağmen, bazı sınırlamalar bulunur. Bundan dolayı frezeleme, delik delme (presleme doğrultusuna dik delikler), diş açma gibi talaşlı imalat operasyonları, kalıpta presleme ile elde edilemeyen şekillerin başarılabilmesinde kullanılır. Sinterlenmiş metallerin talaşlı imalatı genellikle aynı bileşimdeki döküm-dövme alaşımlarınkinden daha kolaydır. Presleme ve talaşlı imalattan kaynaklanan çapakları almak için tamburlama en yaygın kullanılan yöntemdir ve bazı durumlarda içinde aşındırıcı toz bulunan sıvı ortamlar kullanılmaktadır.
İnfiltrasyon işleminde, parça içerisindeki birbirleri ile bağlantılı gözenekler, ana metalin sinterleme sıcaklığından daha düşük bir ergime sıcaklığına sahip bir alaşımla doldurulur. İnfiltrasyon yöntemi uygulanan parçalar sızdırma yapmaz ve mekanik özelliklerinde artış meydana gelir. Ancak bu parçaların boyut hassaslığı azalır.